ESG Bridge Report:(1716)DAI-ICHI CUTTER KOGYO vol.1
![]() President Masamitsu Takahashi | DAI-ICHI CUTTER KOGYO K.K. (1716) |
![]() |
Company Information
Market | TSE 1st |
Industry | Construction |
President | Masamitsu Takahashi |
HQ address | 833 Hagisono, Chigasaki-shi, Kanagawa |
Year-end | June |
Homepage |
Financial information
Sales | Operating profit | Ordinary profit | Net profit | Total assets | Net assets | ROA | ROE |
¥17,440 million | ¥2,296 million | ¥2,482 million | ¥1,523 million | ¥15,533 million | ¥12,548 million | 17.2% | 13.5% |
*Results for the term ended June. 2020. Net profit means profit attributable to owners of parent. ROA stands for return on asset.
Table of contents
1. Corporate Overview
2. Interview with President Takahashi
3. Issues, Materiality, and Measures
4. Progress of Medium-term Business Plan (from FY2019 to FY2021) and future strategy
5. Financial and non-financial data
<For reference>
1. Corporate Overview
DAI-ICHI CUTTER KOGYO is providing maintenance and repair services for social infrastructure based on its expertise in diamond and water jet method, as well as services of building maintenance and reuse and recycling of IT equipment. The diamond method uses industrial diamonds to saw and drill roads and structures. In the conventional concrete crushing method, it was always necessary to be conscious of nuisances such as noise, vibration, dust, but in the diamond method, the operation can be executed safely, speedily, accurately and without having an adverse effect on the environment. On the other hand, the water jet method destroys concrete bonds by jetting water under extremely high pressure. With this method, a concrete structure can be repaired with pinpoint accuracy without damaging reinforcing steels.
The Group includes 5 consolidated subsidiaries, WALLCUTTING Co., Ltd which engages in wire saw and core boring works; KOUMEI Corporation which is strong in offshore engineering (underwater sawing and drilling works); Shin Shin Corporation which is based in Okinawa Prefecture; ASIRE Corporation which is strong in architecture-related water jet method; Movable Trade Networks Corporation which engages in reuse and recycling business; and Diamond Kiko Corporation, which is an equity method affiliate.
Including subsidiaries, the Company has 23 offices across Japan.
1-1 Corporate History
The founder of the Company, who worked at the construction company that introduced road cutters for the first time in Japan, foresaw the expansion in demand for that in the future. He then founded the Company in Chigasaki in Kanagawa Prefecture in August 1967. He did this to engage in the sawing and drilling work of asphalt and concrete structures with the diamond method.
The Company had few projects at first. However, the Ministry of Construction (no Ministry of Land, Infrastructure, Transport and Tourism) issued a directive making it mandatory to use cutters from a safety perspective when performing road cutting work. This triggered an increase in the amount of this work.
While other companies in the same industry were doing business locally, the Company expanded to Chiba, Tochigi, Mito and Takasaki upon opening its Sapporo Office in June 1969. At the same time, it also expanded the scope of its operations to include the drilling and cutting work of concrete structures in addition to road cutting. The mobility to respond quickly to customer needs, the level of operation quality, and the wealth of knowledge and expertise on materials and machines used in operations have been highly appreciated by the Company’s customers. Therefore, its business operations steadily expanded and it registered its stock over the counter with the Japan Security Dealers Association in 2004.
In the 2000s, the Company further accelerated its diversification of methods and expansion of offices across Japan through M&As. It then listed on the First Section of the Tokyo Stock Exchange in December 2017. It is working to solve the social issues faced by Japan (e.g., aging infrastructure).
【1-2. Corporate Philosophy】
The company's management philosophy is “aiming to be the best group by contributing to the society with specialized technologies and high-quality services".
The Company provides specialized technologies at various job sites with the keywords of "Sawing" "Chipping" "Cleaning" "Stripping" and "Grinding". The Company develops its respective businesses for the entire world and aims to become the best company.
Business Policy | We intend to pursue aggressive sales strategies by utilizing our organizational capacity and business development capability. |
Operation Policy | We improve our quality operation power. |
Safety Policy | We promote the health and safety of our employees. |
【1-3. Business Overview】
The business is divided into several categories, Sawing and Drilling Business, Building Maintenance Business, and Reuse and Recycling Business. The Sawing and Drilling Business is handled by DAI-ICHI CUTTER KOGYO, WALLCUTTING, KOUMEI Corporation, Shin Shin Corporation, ASIRE Corporation, Diamond Kiko and UNIPEC Co., Ltd (100% non-consolidated subsidiary). The Building Maintenance Business is handled by DAI-ICHI CUTTER KOGYO and the Reuse and Recycling Business is handled by Movable Trade Networks respectively.
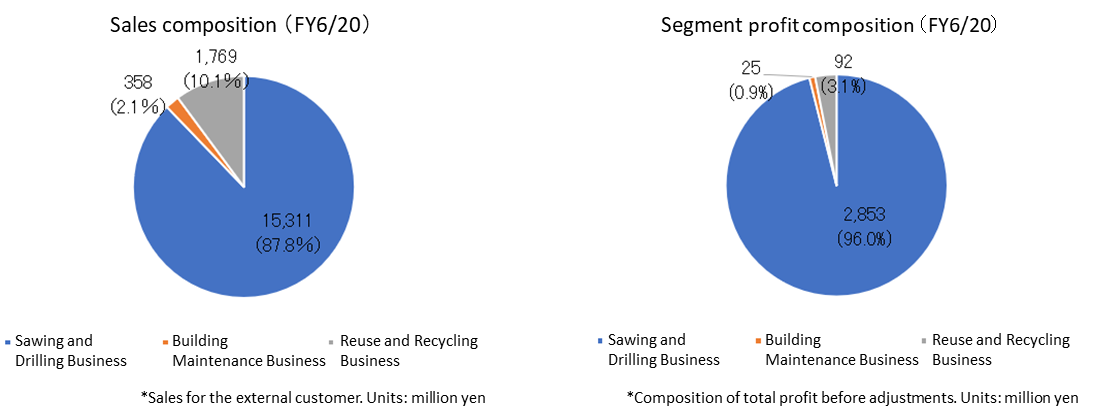
Sawing and Drilling Business
“Sawing and drilling” refers to the sawing and drilling work necessary for various types of road pavement and the demolition and removal of concrete structures. The Company’s Sawing and Drilling Business mainly focuses on the diamond method using industrial diamond (Diamond Method is a registered trademark of DAI-ICHI CUTTER KOGYO) and the water jet method using water pressure. Wastewater generated from sawing and drilling work is collected and neutralized at a large intermediate treatment facility to be reused as cutting water. Waste generated from sawing concrete is dehydrated and recycled into raw materials for concrete.
The Group operates nationwide. DAI-ICHI CUTTER KOGYO’s sales operation covers all eastern Japan. ASIRE has sales based in Kanagawa and Osaka. WALLCUTTING has sales based mainly in the Tokai region. KOUMEI has sales based in Osaka and the Chugoku and Shikoku regions. Shin Shin has sales based in Okinawa prefecture. Diamond Kiko has sales based in the Kyushu region.
As a contractor, the Group plays a major role in the work and maintenance of infrastructure, and its main clients are general contractors, road contractors, and facility providers. When they receive an order, they order sawing and drilling work of concrete to the Group. Since its clients mainly engage in public works, most of the works carried out by the Group are public works (except ASIRE whose clients are from the private sector). On the other hand, works other than public ones include maintenance of chemical plants, oil refineries, electric power plants as well as cleaning by water jet method. Works are classified into civil engineering works, architecture-related works, urban civil engineering works, road and airport works, and plant maintenance.
Main Clients
TAISEI CORPORATION, OBAYASHI CORPORATION, KAJIMA CORPORATION, SHO-BOND CORPORATION, TEKKEN CORPORATION, TOTETSU KOGYO CO., LTD., JFE Engineering Corporation, IHI Infrastructure Systems Co., Ltd., Nomura Real Estate Partners Co., Ltd., Taisei Rotec Corporation, KAJIMA ROAD CO., LTD., Sankyu Inc., Mitsubishi Jisho Community Co., Ltd., Mitsui Fudosan Residential Service Co., Ltd., NIPPO CORPORATION, THE NIPPON ROAD Co., Ltd., SHIMIZU CORPORATION, Sumitomo Mitsui Construction Co., Ltd. (in random order).
Civil Engineering Work DAI-ICHI CUTTER KOGYO undertakes repair and removal services for large structures, such as bridge, port and dam, as well as sawing and drilling services under special environments such as underwater operation. In those specific cases, services are carried out by the Company’s exclusive engineers. |
Architecture-Related Work Various kinds of services for demolition and renewal works are carried out, such as demolition work of a building, base isolation work, seismic retrofit, repair work, and new construction. In addition, the Company can carry out service which is difficult by conventional methods, using alternative methods suitable for reducing the environmental load on the surrounding facilities. |
Urban Civil Engineering Work The Company performs civil engineering related works in urban infrastructure, such as railway operation, waste treatment facility, and waterworks facility, and is also involved in environment-related works that can be handled in total from planning to operation. |
Road and Airport Work The Company carries out various types of sawing and surface treatments for road repair, removal of deteriorated concrete, core drilling for installing lights, runway grooving at airports and others. Its strength is its ability to do the operation even under specific conditions thanks to unique equipment such as grooving machines and custom-made vehicles for core drilling. |
Maintenance of Production Facilities In the maintenance of production facilities, the Company carries out cleaning for plant maintenance, fireless sawing for remodeling work, repainting of floors, and surface treatment. The Company ensures the quality and safety of the work by stationing certified workers for industrial cleaning. |
◎ Main technology : The Company’s original method
Diamond Method
The method is to saw and drill roads or structures by using an industrial diamond. Based on the five basic methods of flat sawing, core drilling, wall sawing, wire sawing, and grooving, the Company has developed a wide variety of diamond methods with its unique ideas.
The tools used in the diamond method are “Diamond Blade”, “Diamond Bit”, and “Diamond Wire”, each of which uses diamond segments. “Diamond Blade” is a blade whose edge is attached with segments made by hardening diamond powder with metal bond. The object is cut by rotating “Diamond Blade” at high speed (using different sizes depending on the type of material and the depth of sawing). “Diamond Bit” is a cylindrical tool with a cutting edges of diamond tips. It is rotated at a high speed to bore an object (using different bits depending on the size of a hole and the depth of the hole). “Diamond Wire” is made by attaching beads made by sintering diamond segments with metal bond to a wire at fixed intervals. “Diamond Wire” can cut any object even in a complicated shape.
Flat Sawing
Generally, flat sawing is the most suitable solution to sawing horizontal surfaces such as floors, floor slabs and pavement. The machine is mounted with a diamond blade. An operator walks from behind and operates the machine by only himself as the machine progresses. It is used for joint sawing, sawing concrete parts for replacement and removal of damaged pavement, and sawing pavement parts when laying pipes under the pavement such as electricity, telephone, gas, water, and sewer pipes. The power source of the machine is gasoline, diesel, electricity and oil pressure. Water is set to come up to the sawing edge during the sawing process in order to cool the cutting edge heated by sawing (dry flat sawing uses compressed air for cooling).
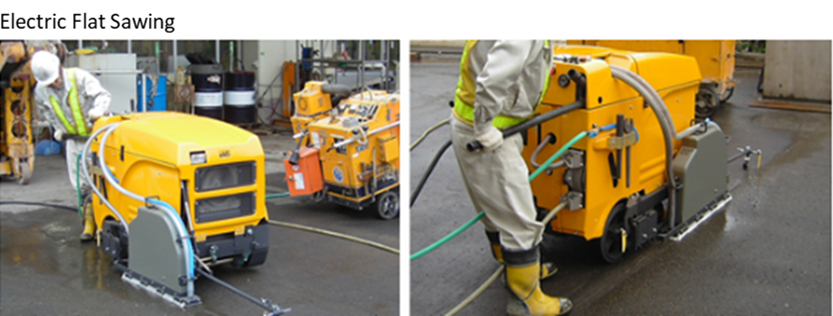
(Source: The Company’s website)
Core Drilling
In this method, holes are made on objects that are drilled by a diamond bit. Core drilling is used in the field where accurate circular sawing is required. Any diameter of hole can be easily perforated, for water supply and drainage pipes, electric wiring, ducts for air-conditioning system, seismic reinforcement, and others. Core drilling can be very useful when the accuracy of the finish is especially required, such as when collecting samples for strength inspection, drilling holes for anchor bolts, and stitch drilling when removing a part of a thick wall.
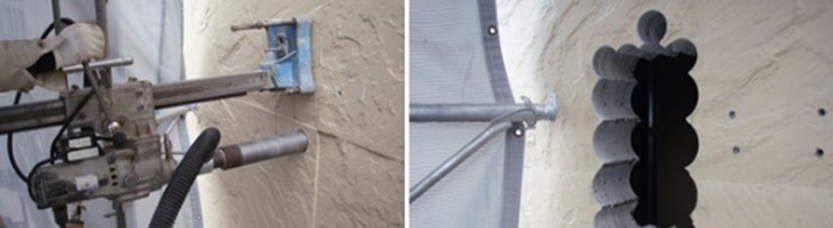
(Source: The Company’s website)
Wall Sawing
In this method, a traveling guide rail is fixed to a wall, a slope, a floor or the like with anchor bolts, and an object is cut by high-speed rotation of a diamond blade and movement of a machine on the track. Wall sawing is often used to install door openings, vents, and windows, and can be cut at both right and oblique angles. As it saws along the rail, it can accurately secure an opening. It can also be operated remotely, making it safe to work in any situation. The compact and lightweight machine makes it easy to carry and provides excellent mobility even in places with limited work space such as buildings, expressways and subways.
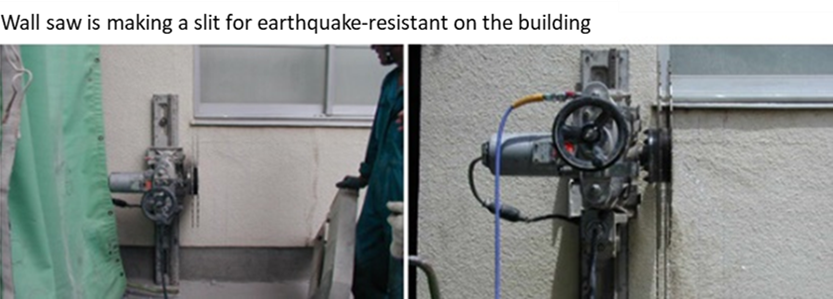
(Source: The Company’s website)
Wire Sawing
In this method, an object is cut by rotating the wire saw at a high speed by a hydraulic or engine type machine while maintaining a constant tension in the wire saw. The method can easily saw a thick and complicated structure regardless of the shape of the object. It can also be operated remotely or automatically, so it can be used safely and freely in all environments, including underwater, high places, and undergrounds.
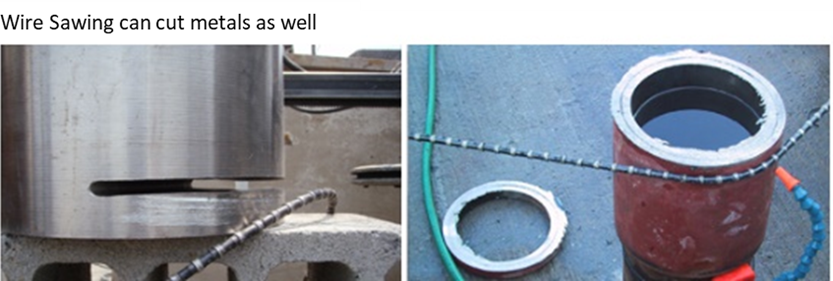
(Source: The Company’s website)
Grooving
In this method, multiple shallow grooves (safety groove) are carved on a road surface in a direction parallel or perpendicular to the traveling direction of vehicles. Diamond blades are attached to a cylindrical device called a drum at a predetermined pitch, which is rotated to cut a road surface (to improve quality of the road surface by improving slip resistance and drainage). And a drum is attached with a grooving machine. There are both dry method and wet method, and by carving grooves on runways, paved roads and steep slopes, slippage can be prevented. This method was first used at an airport in England in 1956, and has spread throughout the world.
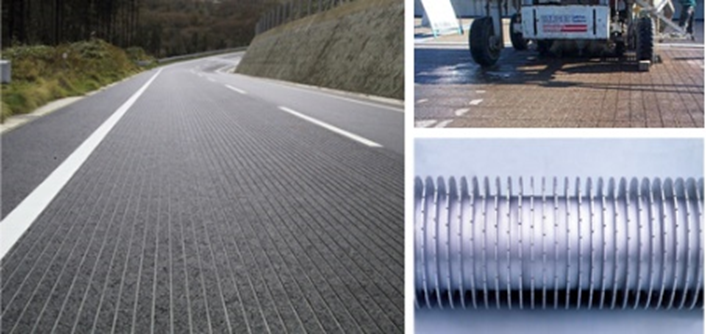
(Source: The Company’s website)
Water Jet Method
In this method, high-speed water, pressurized and compressed by a high-pressure water generator and jetted from a nozzle, is used for chipping and washing. This method is attracting attention from the industry as an excellent method with consideration for the environment, because it has features such as generating less distortion, few microcracks, and less vibration.
The Company uses the method in a wide range of fields, including civil engineering, architecture, plant maintenance and the environment. In civil engineering and architecture, it is used in concrete removal, molding (opening through concrete walls, selective demolition of concrete structure), surface treatment, coating removal, cleaning, and others. In plant maintenance, it is used in cleaning work (including scale removal, and others.) of plant equipment such as tank reactors, and others. In addition, this method can be used for sawing metal (abrasive sawing), so it can be deployed in places where fire is strictly prohibited.
(The strong point of Water Jet Method)
Less Vibration | Unlike the impact crushing by breakers, rock drills, and others, it is characterized by the mechanism to destroy cement mortar bond of concrete by the energy of ultra-high-pressure water jetted from the nozzle. |
Minimal Impact on the Structure | Since deformation, strain and residual stress given to the object are small and microcracks are hardly generated, it is possible to work with the minimized impact on the structure. |
Pinpointed Removal | By setting the appropriate pressure and flow rate, only the deteriorated part of the concrete can be removed with pinpoint accuracy without damaging the reinforcing steels. |
Removing only Coating and Stains | By adjusting the pressure, only the coating or stains of the object can be removed. |
Remote Operation | Remote operation of the machine is easy because the nozzle does not contact with the object. This allows operation in curves and on curved surfaces with uniform quality. |
Building Maintenance Business
DAI-ICHI CUTTER KOGYO is the only one in the group which handles with this business. In complex housing and office buildings, the Company carries out drain pipe cleaning, water tank cleaning, water supply facility inspection, floor cleaning, fiberscope survey, mechanical pit cleaning and so on.
Reuse and Recycling Business
Reuse and Recycling Business is undertaken by Movable Trade Networks, a non-consolidated subsidiary, not subject to the equity method, and two non-equity method affiliates. In the Reuse Business, used IT-related equipment and office automation equipment, such as tablets, PCs, server, and liquid crystal displays (LCD displays), are purchased mainly from companies, and this equipment are sold mainly to corporate clients after data erasing and repairing. The Company also provides data erasing services of IT-related equipment and office installation services of office automation equipment mainly for corporate clients. Used products that are difficult to reuse are dismantled, carried out intermediate processing, and then sold to material manufacturers, who carry out recycling. The items that the Company sells to recyclers range from general materials to “rare metals” such as gold, silver, cobalt and others.
【1-4. Flow of value creation】
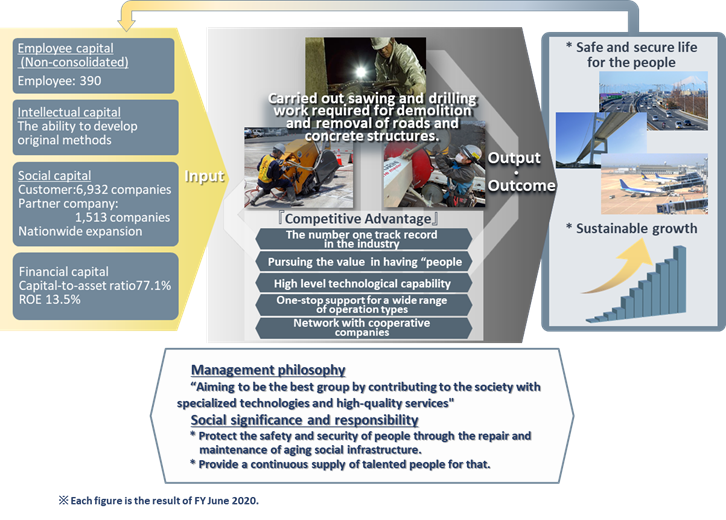
(made by Investment Bridge Co., Ltd)
The Company is involved in a variety of operations to repair and improve the aging social infrastructure in Japan using its advanced technological skills with its core competence of people as a top company in the industry. In this way, it is providing safe and secure lives to people while realizing a sustainable improvement in corporate value.
2. Interview with President Takahashi
● Social Responsibility and Social Meaning of Existence
Q. In recent years, as society as a whole is aiming for sustainable growth, the philosophy, mission and social meaning of existence has been emphasized in companies that are key players in that. First, please tell us about the social responsibility and meaning of existence of your company as you see it.
Japan’s social infrastructure, such as roads, bridges and water and sewer services, were developed together with rapid economic growth. However, now, almost 60 years later, the aging of that social infrastructure has become a major challenge for Japan as a whole. For example, many of the sudden road collapse accidents that have occurred in various places in recent years have been caused by the aging of sewer pipes. It also became clear in the wake of the Great East Japan Earthquake that many facilities lack seismic strength. Moreover, in Japan, where there are many natural disasters in the first place, damage caused by typhoons and heavy rains has become severe in recent years. The aging infrastructure has been greatly damaged and this has had a massive impact on the lives of people. |
![]() |
Under such circumstances, the seismic reinforcement, water pipe renewal work, maintenance, highway repair, bridge and river reconstruction and restoration work we perform are extremely important efforts for Japanese people to live with peace of mind. We believe that protecting the safety and peace of mind of people is our social responsibility and meaning of existence.
In addition, as the amount of aging social capital stock continues to increase, we must hire and train excellent personnel and then continuously send them to job sites to perform a variety of operations appropriately and reliably.
We strongly believe that the supply of such human capital is also an important responsibility of our company.
● Awareness and Way of Thinking about ESG
Q. Please tell us about the relationship between the responsibility and meaning of existence of your company that you just told us about and the environment, society and governance (ESG).
As I mentioned earlier, it is our social meaning of existence to protect the safety and peace of mind of people by engaging in the repair and maintenance of Japan’s aging social infrastructure. We recognize that the supply of personnel for that is a major responsibility we must fulfil.
In other words, this social responsibility and meaning of existence is truly the “S” itself in ESG.
Moreover, in terms of the “E” as well, we have worked on the development of methods to reduce the noise and vibrations that come with various operations as a measure against nuisances since our foundation. We have also been focusing on carbon offset in recent years.
In that sense, we think that the sustainable promotion of business activities while being clearly aware of our social responsibility and meaning of existence will solve social and environmental problems. Furthermore, we also believe it will lead to an improvement in our corporate value.
● Business Model, Characteristics, Strengths and Competitive Edge
Q. What is your company’s business model, characteristics, strengths and competitive edge?
“Expanding the number of orders by specializing in subcontracting”
What I would like everyone to know first in terms of the characteristics in our business model is that we are involved in business specializing in subcontracting instead of being a general contractor.
In general, it is often considered that an aim to be a general contractor with high profitability is advantageous in the construction industry which has a multiple-level subcontracting structure.
However, general contractors must keep an eye on all aspects of projects – from upstream to downstream. Our company, which specializes in subcontracting, can handle only the operation that is our greatest strength. Accordingly, we are good at completing jobs. As a result, we can steadily accept orders for new operation. This means it is easy to aim to scale up.
“The number one track record in the industry for expansion across Japan”
In addition, we are involved in a niche line of business in the specialized contractors.. Therefore, we expanded nationwide from an early stage as it was necessary to secure a certain level of projects and customers to pursue a size of sales and profits.
We currently have 23 offices across Japan. We are also utilizing our network with partner companies to engage in approximately 60,000 projects a year ordered by approximately 7,000 customers – from local contractors to super general contractors. Moreover, we are the only company that has expanded across Japan. It is also only our company that can engage in so many projects.
One of our major strengths is that we can diversify risk by accepting orders from diverse customers.
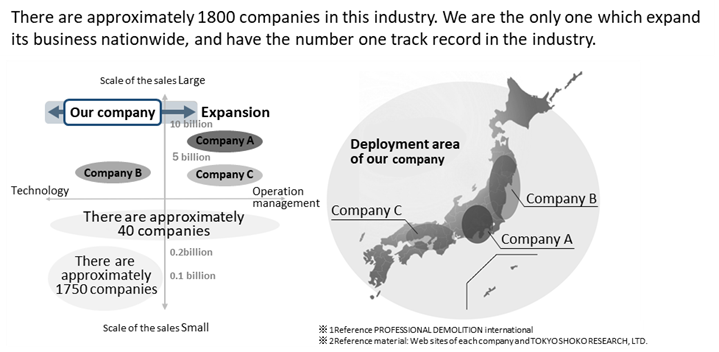
(Provided by the Company)
Pursuing the value in having people
Next, I would like everyone to understand that our core competence is people.
With the declining birthrate and aging population, it is said that the one third of the approximately 3.4 million construction workers there are currently will leave their jobs due to aging by 2030 in the labor-intensive construction industry. The impact of that will be enormous.
Against this backdrop, there is no doubt that the value in having people will increase incomparably in the next 10 years. To put it another way, the competitive advantage of companies with people will increase dramatically.
To that end, we value people and are striving to secure as many excellent people as possible under a recognition that supplying excellent people is a social responsibility as I mentioned earlier.
Of course, labor saving will also be an issue in the future. Nevertheless, we would like to strengthen our competitiveness and pursue our social responsibility with a strong awareness of the value in having people rather than passively curbing recruitment.
Responding to a wide range of work types in a one-stop service with high level technology
There are approximately 1,800 companies in this industry. However, there are very few companies that extensively provide specialized technologies under the keywords of cutting, chipping, cleaning, stripping and grinding with many people like our company. That point is highly appreciated by many of our customers.
For example, if work to cut roads, drill holes in concrete and remove pillars is necessary at one job site, we have a big advantage because we respond to a wide range of work types in a one-stop service with high level technology rather than designating contractors suitable for each job.
Network with partner companies
Moreover, our network with partner companies is a very important key to our competitive advantage.
We recognize that our partner companies are important partners. We do not allow them to be called “subcontractors” in our company.
Currently, we share operations roughly 50-50 between our company and our partner companies. As a result, we always maintain our high operation even in a situation when the amount of operation is slightly reduced. We are also able to handle even unexpected operations thanks to our partner companies. It is also thanks to our partner companies that we have been able to expand across Japan.
Our partner companies feel it is meaningful to help the work of our company at the top of the industry. Accordingly, we are working to solve social issues through co-existence and co-prosperity instead of taking advantage of them or looking down on them.
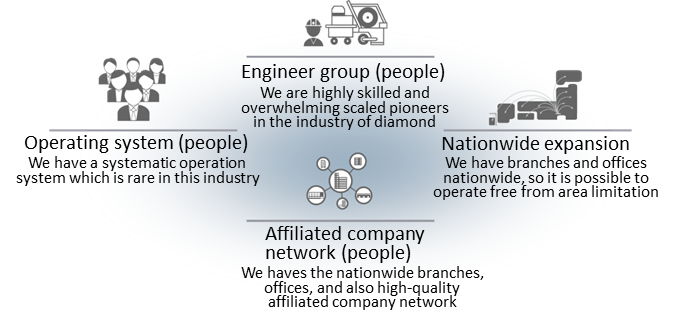
(Supplied by the Company)
● Efforts in Major Materialities
Q. Your company has now selected 11 materialities for the first time. (Refer to “3. Challenges, Materialities and Efforts.”) Of these, I would like to ask you about the particularly important materialities for the sustainable growth of your company.
First, I would like to ask about human capital. What do you think about the position of human capital in your company?
As I mentioned earlier, human capital is an indispensable and important asset to responsibly fulfill our responsibilities in our company for which the repair and maintenance of Japan’s aging social infrastructure is our social meaning of existence.
I am proud to think of our employees working in job sites as “cool.”
I think it is really cool to work without forgetting to smile with a sense of mission in various environments – even if they are sometimes covered in mud, sweaty from being in the intense heat or frozen from working in the extreme cold.
However, they themselves have yet to realize how cool they are. That is a great shame. There are also cases in which people don’t pay attention to their appearance, for example, because they have not realized that yet.
Instead, I want them to change their awareness to understand that they are doing good work, wonderful work and work for society.
In that way, more people will understand the work of our company. The number of people who want to join our company will also increase and our relationship with our customers will also become stronger.
In that sense, while strongly recognizing the importance of human capital, I believe it is my mission as president to work on creating an environment that changes the awareness of our employees.
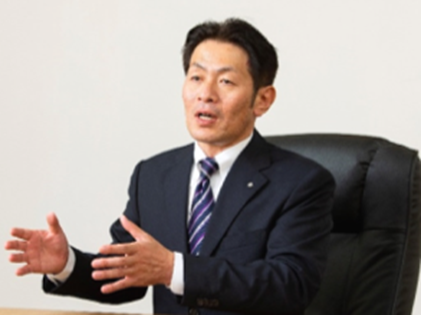
(Provided by the Company)
I think that one of the efforts necessary for that is branding. I believe that branding is especially important in the company. The Daiichi Cutter Management School made a video to train managers and executives.
The participants brought together as one the scenarios they had come up with imaging the ideal state of the company under the theme of “Daiichi Cutter 10 Years from Now.” These included the future social situation, their private lives, the people they work with and cooperation in the reconstruction of disaster-affected areas. They even arranged the cast before appearing in the video as the performers themselves.
The work we do of cutting roads, cleaning scale, removing structures and eliminating things does not result in deliverables that remain as a shape like in the manufacturing and construction industries. Consequently, it is kind of difficult to feel a sense of accomplishment and there are parts that depend on each individual’s resourcefulness.
Accordingly, we had the trainees attempt to make a video as a deliverable in this training.
Designing the process, producing the video and working together with coworkers in the work we do daily is the same as manufacturing. It is possible to really feel a sense of accomplishment. The participating members could really feel this through this training and video production.
In addition, when making a presentation to all employees, I received good impressions and positive opinions from many of them.
I think that working on their awareness made it possible to provide the realization that their work is “cool.”
We have published this video on our website. Please take a look at it.
(URL: https://youtu.be/JywTRAXxLYs)
Moreover, in addition to this, I repeatedly send messages through various opportunities, such as management briefings, in-house newsletters, morning meetings and evening meeting to all employees.
We are also working to turn women into valuable assets.
At present, we have four women working in job sites. They brighten the atmosphere of job sites and our customers also love them. We have seen good aspects from that.
We would like to connect their opinions to reform and improvement of job sites in the future.
For example, the weight of machines is a challenge that needs to be solved for women to work. Moreover, solving this will also help those who are getting older in addition to women.
Moreover, it was said that you could only be called a fully qualified worker once you had done everything for yourself – from steps 1 to 10 – for the first time. However, it is fine for strong male employees to do steps 1 to 7 and then women to take charge of finishing off steps 8 to 10.
Dividing labor can also improve efficiency. Therefore, I tell offices which have been assigned women to favor those women to the fullest to discover many realizations like that.
In other words, creating an environment in which women can work easily has many benefits over the entire job site.
It is likely that those women will transfer to operation management and sales after working in job sites for several years. The fact those women will be active for a long time will bring about opportunities that will lead to our next female employees joining the company. We have high expectations for the success of those women while creating the right environment.
On the other hand, we also need to secure personnel with expertise in addition to site personnel for our company to continue growing.
For example, in the fields of finance, human resources, public relations and R&D.
I believe it is necessary to strengthen our team focused on mid-career employment in this respect.
Q. Please tell us what kind of efforts you are making under what kind of thinking in regards to fostering the worth of working for your employees, your education and training systems, and the health and safety of your workers.
The thing we are most aware of in terms of training our employees is to give them the opportunities to work and take on challenges.
For example, by allowing a second-year employee to participate in the planning and implementation of exhibitions for recruitment, he becomes aware that he was chosen to be a part of our company. On the day, he can look back at himself to talk to students in an easy-to-understand manner about what he has been doing since he joined our company. This also serves as training to speak in public.
We give meticulous education by year and rank. Moreover, in parallel with training, we want to provide various opportunities and challenges to lead to personal growth.
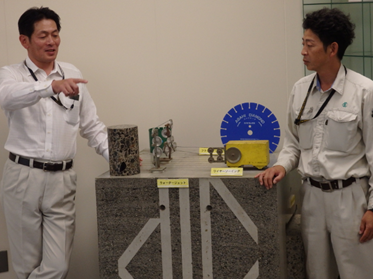
(Provided by the company)
We also encourage motivated employees to enter university as mature students.
Of course, it is difficult for those people to create the time to continue studying for two to four years while working. That is a challenge. Overcoming that challenge gives them confidence. They also contribute greatly to the company, so we consider this an extremely important program.
Moreover, we have enhanced various subsidy programs that apply not only to employees but to their families For example, we assist with influenza vaccination subsidies for families and help with the physical examinations of spouses of employees with a set of gynecological examinations.
This is a message to families that our employees can work because they are supported by healthy families.
Q. Next, please tell us about your efforts and innovations to strengthen the competitiveness of your company.
We work on R&D under the keywords of troubles, safety and energy saving. In addition, we are also aware that our important tasks include environmental measures such as the ECOA hydraulic drive system driven by water without using oil that we developed recently and labor saving under a declining birthrate and aging population.
In terms of labor saving, we are also focusing on research and development to create an environment in which it is also easy for women to work, and environment in which people with disabilities can work in the same way as those without disabilities and an environment in which elderly people can continue to work on job sites.
If we achieve these, I believe it will also greatly contribute to society in addition to creating business opportunities. This is because we will have refined remote and automation technologies that are the future of laborsaving operation. It will also be because we are able to reliably capture the demand for the maintenance and construction of infrastructure – including the decommissioning of nuclear power plants.
Nevertheless, it is difficult to complete everything by ourselves. Therefore, we are working on open innovation with various universities and companies.
Strengthening our development capabilities will serve as a source of our competitive advantage in addition to enhancing our human capital. Accordingly, we will continue to invest in and refine management resources on this in the future.
Q. What are your thoughts about environmental challenges? For example, greenhouse gas emission control, vibration and noise suppression, and water and sewage management?
We have worked on developing methods to reduce noise and vibrations that come with various projects as measures against nuisances since the foundation of our company. In recent years, we have promoted carbon offset with two services: Intermediate Sludge Treatment Service with Carbon Offset and PlaCon floor®. We are the only company in the industry that has introduced carbon offset.
In addition, various plants across Japan that currently emit carbon dioxide will be forced to undergo large-scale renovations to reduce those emissions according to the target set by the Japanese government in 2020 to realize a carbon neutral society by 2050.
This will lead to a significant increase in business opportunities through the resolution of social issues for our company. We would like to expand out human capital to steadily meet such demands and expectations.
Q. Please tell us your thoughts and efforts with regards to corporate governance.
We recognize that improving our corporate value over the mid- to long-term by building a corporate governance structure in which we co-exist and co-prosper with our customers, shareholders, local residents, employees and other stakeholders is an important management issue.
We are a company with an audit & supervisory board. We appoint two outside audit & supervisory board members and two outside directors to ensure management transparency and soundness. We plan for all four outside audit & supervisory board members and outside directors to be independent officers in the near future. This will further strengthen our management monitoring functions.
● Mid-term Management Plan
Q. Next, please tell us about the current self-evaluation of your mid-term management plan that is underway at present. What are the key points in your next mid-term management plan?
Our current mid-term management plan will end this term (fiscal year ending June 30, 2021). I think I can give us a passing mark for the expansion and retention of employees, the expansion of our sales range, and strengthening of our partner company structure at present.
In particular, we have intensified mutual understanding with regards to building and deepening relationships with partner companies. We have also been able to thoroughly deal with unexpected operations, so I would give us a high score there.
On the other hand, we are still in the process of building a system to further strengthen our sales structure. That is still something for the future.
We will continue to focus on personnel strategy and human capital efforts in the next mid-term management plan that we are currently formulating. Above all, an overtime hour and how the management with that is pushed forward are clear problems.
If we can achieve that, I think we will become a company a stage or two above what we are now in terms of internal fortitude in addition to size.
The work style reforms we are aiming for are not easy; it will be a difficult process of course. However, when we overcome those difficulties, we will be an attractive workplace compared to others in industry in addition to those in the construction industry for the first time. We will look to make great progress in terms of securing personnel.
We would like to pursue quality instead of just size.
● ROE
Q. What do you think about your ROE?
Our ROE has been at a level of around 12 to 13% over the past few terms.
We will continue to invest, but we would like to raise our asset efficiency and maintain our ROE at the same level to meet the expectations of our shareholders and investors.
● Other Risks and Challenges
Q. Please tell us about the impact of COVID-19.
Anxiety rose throughout Japan and various economic activities stagnated in the first wave in the spring of 2020. Nevertheless, virtually no job sites stopped except for the maintenance work for condominiums. This reminded us that we are needed in society.
On the other hand, employees who came to job sites while being asked to avoid leaving their homes were also worried about their families. Therefore, we provided them with an allowance to express our feelings of gratitude.
It is expected that capital investment will continue to be curtailed depending on the situation in our customers in the future. Accordingly, I am not optimistic. Nevertheless, there is no doubt that we have a presence needed by society. Therefore, I don’t think we will be overly affected by COVID-19.
On the other hand, although not directly related to COVID-19, the public budget allocation for disaster prevention and mitigation under the national resilience plan will be a major supporting factor for our orders involving maintenance and repairs.
Q. I think it is necessary to work on improving profitability and productivity as a company at the same time as working to improve the workplace environment – including the payment of overtime pay – toward securing craftsmen. What are your thoughts on that?
Securing craftsmen is an effort that will further strengthen our competitiveness. On the other hand, we are fully aware that there are risks if things do no go as we expect.
We will focus achieving that as our biggest challenge to reduce risks and sustainably grow the corporate value of our company.
As I mentioned earlier, we have created a mechanism in which it is possible to stably undertake orders by linking up with partner companies while fully operating our own operation.
First, we are aiming to maintain and improve profitability and productivity and to realize appropriate time management by further strengthening our relationship with those partner companies.
In addition to that, we have started developing technologies such as the laborsaving and work visualization technologies I talked about before. We are looking to maintain and improve profitability and productivity through these efforts.
● Message to Stakeholders
Q. Thank you for talking to us about various matters. Finally, please can you give a message to your stakeholders?
We are an extremely modest company. We are a company that is rarely seen by customers. Nevertheless, as I said at the start, we are a company shining bright with an extremely large social responsibility and social meaning of existence to solve the challenges faced by Japan with aging social infrastructure.
We will continue to aim to be a company that shines even brighter so that we satisfy our customers, partner companies, employees, communities, shareholders and all our other stakeholders by realizing sustainable growth and by providing value to society in the future.
On the other hand, although we have started to disclose ESG information with the issuance of this ESG report, we do not think we have made sufficient concrete efforts or data disclosure on ESG from a perspective of completeness. We will continue to work on this as an important challenge with a focus on developing our internal structures.
I would like to ask all our shareholders for your continued warm support. Thank you.
3. Issues, Materiality, and Measures
The following are the challenges and materialities that Daiichi Cutter Kogyo is aware of currently.
We also conducted interviews with those outside the Company when selecting the materialities.
Challenge | Materiality |
Environment
| Control of greenhouse gas emissions |
Suppression of vibrations and noise | |
Water and drainage management | |
Social capital | Specialized technologies and high standard services |
Contribution to local communities | |
Human capital
| Fostering of the job satisfaction of employees |
Education and training system | |
Employee health and safety | |
Business model and innovation | Efforts and innovations to strengthen competitiveness |
Risk management and governance | Expansion of the corporate governance structure |
Risk management (accidents and laws/ordinances) |
*Prepared with reference to the SASB Materiality Map.
3-1 Materialities in Environment Challenges
The Company recognizes that contributing to environmental problems is one of its important responsibilities. In addition to reducing its environmental burden with various methods, it is possible for its client companies to implement carbon offset using the Company’s services as below. This also leads to the creation of business opportunities.
(1) Reduction of Greenhouse Gas Emissions
The Company is promoting carbon offset* with two services incidentals to its main business: The Intermediate Sludge Treatment Service with Carbon Offset and PlaCon floor®. It does this to reduce greenhouse gas emissions.
*Carbon Offset
Companies are making efforts to reduce greenhouse gas (GHG) emissions (e.g., CO2) that cannot be avoided in daily life and economic activities. Carbon offset is the concept of contributing to the environment by offsetting the amount that cannot be reduced despite that with credits created from reduction and absorption activities implemented elsewhere.
(i) Intermediate Sludge Treatment Service with Carbon Offset
The Company started offering the Intermediate Sludge Treatment Service with Carbon Offset on July 1 2020. This is the first effort in the industry to carbon offset the energy of the facility operation used when performing the intermediate treatment of sludge discharged through its flat saw operations in-house.
Overview of the Effort
When Daiichi Cutter Kogyo performs in-house the intermediate treatment of sludge discharged through its flat saw operations, its carbon offsets one year’s worth of CO2 generated from the energy used when operating the treatment facilities.
Sludge becomes neutralized water and dehydrated cakes when it is intermediately treated. The neutralized water is reused as cutting water and the dehydrated cakes are reused as the raw materials of concrete to be environmentally-friendly.
The Company has also now furthermore decided to carbon offset the energy used in the operation of its sludge treatment facilities as its corporate responsibility.
Emission credits used for carbon offset are an effort that responds to the opportunity to utilize renewable energy that includes the supply chain by adopting renewable energy credits.
The Company has acquired Carbon Offset Certification, third-party authentication, for this service. This ensures a certain level of reliability and transparency for this effort. Moreover, there is no additional charge for carbon offset. Therefore, it is possible for customers to contribute to the environment just by asking the Company for intermediate sludge treatment.
Background to the Introduction of This Service
The Company provides sophisticated technology by implementing a variety of operations in a wide range of fields including construction, architecture and facilities with a focus on the sawing and drilling of concrete structures. In recent years, global warming has become more serious. Against this backdrop, it has become necessary to balance conflicting matters in terms of urban development and conservation of the global environment. Accordingly, the Company decided to provide this service to reduce its environmental burden to also be able to continue its business activities in the future.
(ii) PlaCon floo Carbon Offset Compatible Operation
Damage to the floor and around cracks is liable to occur in factories and warehouses. This is caused by the adhesion of oil, the impact from falling objects and repeated loads from the movement of heavy objects. If the flooring peels from the damaged points on coated floors and oil permeates the peeled surface, the concrete floor itself will weaken and its functions as a floor will be impaired.
The Company implements operation called PlaCon floor in response to this challenge. PlaCon floor involves grinding and polishing the low-strength surface layer to produce floors that take advantage of the inherent durability of concrete.
Like the intermediate sludge treatment service, the Company is deploying PlaCon floor as carbon offset compatible operation to support the activities of its customers to proactively reduce their environmental burden.
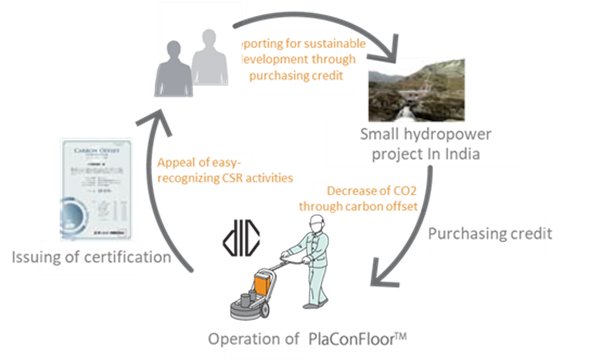
(2) Suppression of Vibrations and Noise
As touched upon in “1-3. Business Description,” the major feature of the diamond method and water jet method employed by the Company is the reduced vibrations and noise. The adoption of these methods is expanding as an alternative to conventional methods with lots of vibrations and noise despite being inexpensive.
The low vibrations and noise also have a significance in anti-aging work in addition to not adversely affecting local residents when implementing operations in urban areas.
The Company cares for part of existing old structures with repairs and reinforcements when extending the life of those structures. However, if adopting a method with lots of vibrations on those parts, it is possible that cracks will occur even on the parts it is not working on.
In contrast to that, the diamond method and water jet method are highly rated because it is possible to suppress the generation of cracks that cannot be seen with the eyes.
(3) Water and Drainage Management
Water is used in the work when implementing the diamond method and water jet methods that are the main methods of the Company. Therefore, it generates wastewater in which sludge (chips) and water are mixed together by cutting.
The Company is implementing the following methods to appropriately treat this wastewater without burdening the environment.
Method | Overview |
Water recycling method | This is a system in which it is possible to collect and reuse wastewater used for cooling water. The flat saw wastewater at the time of road cutting is pumped up as it is and collected as mud (slag). It is then separated into water and solids by filtration, pH treatment and solidification treatment. The water can be reused as cooling water while the solids can be reused as cement materials and other resources.
![]() (From the materials of the Company) |
Dry diamond method | This is a method that does not use cooling water for cutting. It was difficult to cut without water in the past because the diamond segments could not endure. However, the quality of diamond segments has improved in recent years enabling a dry cutting. This does not generate dirty water, so it is environmentally-friendly. In addition, it also has the benefits of being able to significantly reduce the amount of industrial waste and cut costs while making post-treatment easier. There is a dry flat sawing method, dry core drilling method, dry wall sawing method and dry wire sawing method among others.
![]() (From the materials of the Company)
The Company is also developing its own machines and tools that assume use under conditions with a high level of difficulty (e.g., nuclear power plants). |
Intermediate disposal site | The Company has its own dedicated plant to perform the intermediate treatment of wastewater approved by the local government (intermediate disposal business). The Company opened a large intermediate treatment facility dedicated to flat saw wastewater that can process more than 10 cubic meters a day for the first time in Japan in 2014. Having an intermediate disposal site enables the Company to provide a one-stop service from cutting work to wastewater disposal. |
The Company is taking comprehensive measures against discharged slurry by using the water recycling method and by operating the intermediate disposal site.
Another major feature is that it is possible to provide variations in slurry disposal to the customer according to the actual conditions at each job site.
(4) Other
ECOA Hydraulic Drive Cutting Method
It was common to work with hydraulic equipment and air tools in operations at the waterside or underwater for which electric tools cannot be used. Measures to prevent oil leaks from hydraulic equipment were a big challenge and were a lot of stress.
The Company developed a drilling machine equipped with a motor driven hydraulically (force by circulating water) instead of driven by oil (force by circulating hydraulic oil) to solve this problem. In addition to eliminating the risk of oil leaks, it is also not necessary to treat the waste oil. This contributes to a reduction in the Company’s environmental burden.
3-2 Materialities in Social Capital Challenges
(1) Specialized Technologies and High-level Services
Social infrastructure is aging. In 15 years, 63% of the approximately 726,000 bridges and 52% of the approximately 44,000 port facilities in Japan will have been built more than 50 years ago. This trend is the same as the changes in the demographics and is an almost accurate estimate of the future.
Let’s also look at long-term trends in the Japanese construction market. Construction investment has halved from its peak at the time of the financial crisis in 2008. While it has been recovering in recent years, the upward trend in the total amount of net social capital since 2000 has returned to normal. It has been flat or slightly downward recently. This indicates that construction investment has shifted from construction and building to maintenance and repairs. As described above, the majority of infrastructure have been around for nearly 50 years since when they were built. Against this backdrop, there has been a shift from tearing down and rebuilding to repairing and using for longer. In other words, the necessity of maintenance and repairs is rapidly increasing with the aging of social infrastructure.
This is proven by the fact the maintenance and repair expenses announced by the Ministry of Internal Affairs and Communications have been showing steady growth every year while public works projects have been curtailed. The increasing need for maintenance and repairs is an unchanging trend against the background of the aging of social infrastructure.
![]() |
![]() |
(From the materials of the Company)
Under such trends, the work the Company is involved in is mostly maintenance and repairs under the assumption that existing structures will be used in the future.
Moreover, as touched upon in “(2) Suppression of Vibrations and Noise” in “3-1. Materialities in Environmental Issues,” the great feature of the diamond method and water jet method employed by the Company is that they have few vibrations and little noise. Customers also highly rate the ability of the Company to suppress cracks which cannot be seen by the eyes that damage structures during anti-aging work.
In this way, the Company is an important player in contributing to solving this social issue by having the technologies to deal with the aging of social infrastructure that will become increasingly serious over time and having many craftsmen who support these technologies as full-time employees.
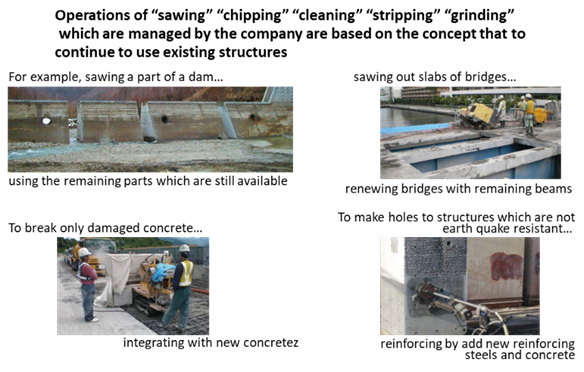
(From the materials of the Company)
(2) Contribution to Local Communities(i) Takeout Subsidy for COVID-19
The Company has 16 sites across Japan by itself. It emphasizes connections with each region and is deploying regional contribution activities in various aspects.
The introduction of a takeout subsidy in May 2020 is one of them.
The purpose of this was to support, as far as possible, restaurants in regions suffering due to requests to avoid going out in response to the declaration of a state of emergency because of COVID-19. The Company paid a subsidy to all employees, including those who have been furloughed and those who are working from home, for purchases from restaurants that newly started offering takeout due to the requests to avoid going out.
The Company recommended purchasing lunch during working hours at restaurants that were trying takeout meals for the first time. It subsidized the cost of that up to 500 yen per meal. The Company believes that this increased communication between its employees and local restaurants and thereby leading to an evolution in its connections with the community. The Company plans to continue contributing to a sustainable society in a variety of ways in the future.
(ii) Selected as Chigasaki’s First Naming Rights Partner
The Company was selected as a partner in a naming rights contract for Chigasaki, the city’s first attempt at such, in January 2021.
Chuo Park, a place of relaxation for the people of Chigasaki, will be nicknamed Daiichi Cutter Kiiro Park from April 2021.
Background to the Naming Rights Contract
Many of the employees of the 54-year-old company headquartered in Chigasaki are from the city. It has been supported and developed by this region.
The Company bid to be a partner through these naming rights because of its desire to raise the social contribution awareness of its employees in addition to contributing to the local economy.
Origin of the Daiichi Cutter Kiiro Park Name
Yellow (kiiro) is the corporate color of the Company and it is also the color of the sun that shines brightly in the center of the sky.
This color represents the image of the park located in the center of Chigasaki which serves as a base of communication that brings tranquility and joy to the people of the city who use it.
The naming rights contract is for five years from April 1, 2021 to March 31, 2026.
The Company has made the following comment: “We hope that Daiichi Cutter Kiiro Park will become a place that offers a calm time to many people.”
(iii) Donation of Yellow Safety Hats for First Grade Elementary School Students
Chigasaki City used to distribute yellow hats to elementary schools free of charge, but due to financial difficulties, the city planned to shift to a system in which safety hats are purchased by respective households in fiscal 2021. Receiving the information, the Company decided to purchase 2140 hats for first-year pupils and school cloth badges to be attached to them, and donated them via the city.
President Takahashi said “I hope that elementary school students enjoy life without accidents.”
3-3 Materialities in Human Capital Challenges
The shortage of personnel and engineers in the future due to various factors (e.g., the impact of the declining birthrate and aging society and the image of the industry) is becoming a challenge in the construction industry.
The Company has set securing and training future leaders, reforming work styles and improving productivity as priority measures under the keyword of personnel in its mid-term management plan. Under this, it has been touting many new efforts ahead of others in the industry. These include the creation of an environment in which women and those with disabilities can work comfortably and the recruitment of foreign workers with a view to expansion overseas in the future.
The Company recognizes that it is people who support its core competence. It plans to proactively further strengthen its efforts to secure and train personnel and its competitive advantage by “winning with people” at the core in its future strategy.
(1) Fostering of the Awareness and Job Satisfaction of Employees
● Labor Management and Work Styles
The upper limit on working hours has been relaxed by special provisions in the construction industry. However, a curb on working hours is being sought toward 2024.
The workplace of employees is job sites away from the company for specialized contractors. Therefore, travel time is inevitably included in working hours. This means there are many challenges to reducing working hours. Nevertheless, it is necessary to be an attractive company compared to other industries from the perspective of securing personnel.
Accordingly, the Company, which considers people to be its most important asset, has been striving to reduce working hours under its own standards in anticipation of a gradual tightening of regulations in the industry.
It sets an upper limit on overtime per month of less than 60 hours in the fiscal year ending June 30, 2021. Moreover, it is running a Work-Life Balance Project. This is a large company-wide project to conform to the standards in 2024.
The Company recognizes that working hours include the following time. The time traveling from the Company to the job site, the time returning to the Company, and the one performing miscellaneous tasks in the company. Therefore, there is a structure in which several hours of overtime arise per day just by moving back and forth even if work at the job site is completed within the scheduled time.
It is common in this industry to only perceive the time spent working at the job site as working hours. Recognizing that working hours include travel time itself is rare. However, because it is necessary to be an attractive company compared to other industries from a perspective of securing personnel, it is tackling this challenge. It is working on designing a system in this project in a form that brings together many members well-versed in business from all over the Company and divides them into subcommittees. It is working to improve working conditions from all directions and to build attractive workplaces as a prerequisite to fostering job satisfaction. This includes employing a flexible paid vacation system, adopting a complete five-day workweek system, increasing salaries periodically and enhancing the retirement allowance system in addition to curbing overtime hours.
In addition to introducing attendance management using tablets, it is building a structure that can manage overtime (holiday) hours on a daily basis. It is also streamlining coordination with office work (e.g., the digitalization of work slips). In this way, it is also reducing the burden of work other than job site work for craftsmen.
This labor management structure is at a level that is also highly rated by the Labor Standards Bureau.
Moreover, it is backing the diverse work styles of its employees. It is also working on creating a job site environment that can accept female employees in addition to the selection of work over the whole of Japan or limited to a certain region and the establishment of work hours according to work style.
The Company is also taking measures from the perspective of raising the awareness of its employees.
As mentioned above, it offered a takeout subsidy to support local restaurants suffering from COVID-19 in May 2020. This encouraged communication with local residents and led to improved employee engagement.
● Brand Value Improvement
The Company is also working to improve the brand value of craftsmen to foster job satisfaction.
The Company has been active with an inconspicuous existence rarely seen as a company specializing in subcontracting since its foundation. However, the Company believes it needs to stand out by showcasing its charms as an important player that supports social infrastructure in an industry in which there is an increasing gap between supply and demand in terms of the increased demand for the repair of aging structure and the lack of craftsmen due to the decrease in population in the future. It is promoting its own branding strategy under that belief.
The Company thinks it can honestly express the sight of its craftsmen working as “cool.” It is promoting efforts to showcase this coolness to those inside and outside the Company to give it a presence seen by many people. In this way, it is striving to have pride in its own work.
The Company has released an interactive video on recruitment sites that emphasizes the coolness of working in job sites. It consists of a story that develops by the viewer selecting answers. The purpose is to give the view an image of working at the Company by watching this cool video.
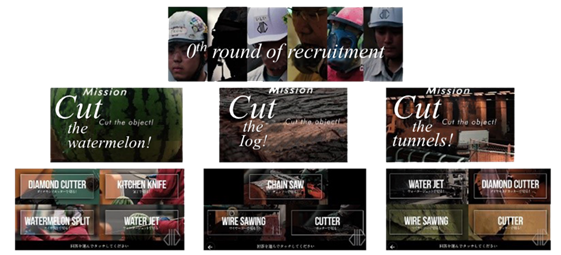
(Provided by the Company)
In addition, four women currently work as craftsmen. The Company would like to develop an environment that enables women to work as craftsmen from all angles in the future.
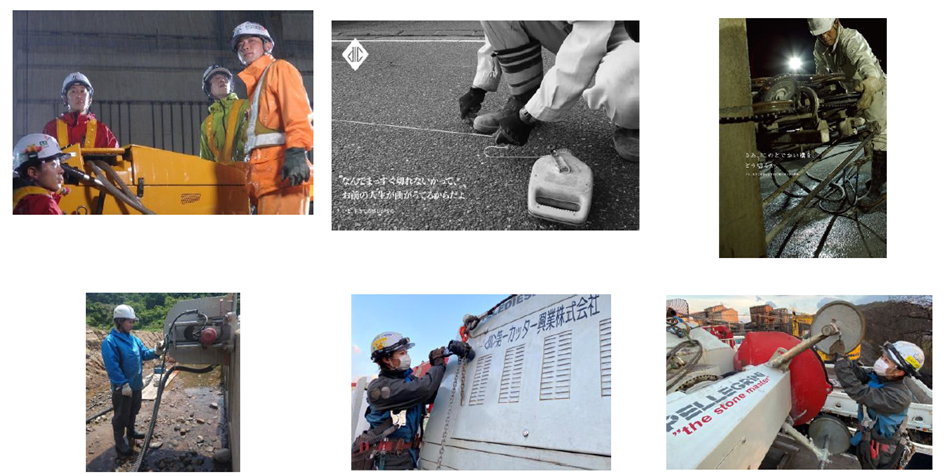
(Provided by the Company)
(2) Education and Training System
The Company performs operations under conditions that are different at each site. Therefore, in addition to various techniques, the Company’s craftsmen need to have a wide range of skills (e.g., extensive peripheral knowledge and strong communication skills).
To support this, the Company provides training on a group basis. This training is divided into various categories (e.g., safety, techniques, qualification acquisition, acquisition of peripheral knowledge and cultivation of humanity).
Taking craftsmen away from job sites to give them educational opportunities leads to a decrease in productivity in the short term. This means that “learning by observing” – so-called OJT – is common in other companies in the same industry. However, the Company has adopted this education system from a long-term perspective in that forming a group of craftsmen equipped with advanced skills will lead to a continuous improvement in results in the end.
For example, third-year training given to employees in the Service Division in their third year in the Company aims to give experiences of special methods and to promote understanding of the Company for 30 days or more. The Company believes that long-term training is essential for the growth of mid-career employees who will represent the company in the future.
The education system is based on a personnel development roadmap of “improve technical capabilities → acquire qualifications → expand technical fields → improve resourcefulness →become a leader.” This system secures differentiation and superiority in the industry. At the same time, it forms depth in the engineer group. This leads to the further strengthening and growth of the Company’s competitive advantage.
In addition to this, the Company also endorses admission to university as mature students (correspondence system) for its employees. It has adopted a mechanism to reduce the financial burden of this on its employees.
(3) Employee Health and Safety
The Company attaches great importance to the health and safety of its employees. This has led it to running a work-life system ahead of others in the industry. It is focusing on building a workplace environment in which its workers, an important management resource, can work easily. This includes an enhanced welfare system in addition to the aforementioned job site work management and office work optimization (systemization).
● Health
The Company has enhanced various subsidy programs that can be applied to families in addition to its employees themselves.
*Influenza vaccination subsidies
*GLTD insurance systems (lifetime leave compensation)
*Spousal physical examination subsidies
*Quitting smoking subsidy system
*Infertility treatment subsidy system, etc.
● Safety
The Company prioritizes improving literacy against dangers associated with operations through its training system and many internal rules over costs. It thoroughly puts into practice safety first operation.
Operation is often accompanied by the removal of large concrete blocks. This can easily lead to serious accidents. There are an especially large number of rules for the technology to remove these large concrete blocks. Together with this, the Company provides education using a safety manual made with illustrations, photographs and videos.
This safety manual is more than 50 pages long. It contains precautions, work procedures, preventative measures, damage mitigation measures and advice on all aspects that may lead to dangers relating to the work to remove large concrete blocks.
3-4 Materialities in the Business Model & Innovation Challenge
(1) Efforts and Innovations to Strengthen Competitiveness
● Development of New Methods and TechnologiesThe Company has been developing its own technologies, including the diamond method, and leading the industry. The ability to develop such methods and technologies is the source of its competitiveness.
It successfully developed a new method called the eCOA core drill method in 2020. In addition, it is investing to establish laser technologies relating to the five keywords of cutting, chipping, cleaning, stripping and grinding.
TOYOKOH Inc. (Shizuoka Prefecture) is a technological startup company. It developed the CoolLaser technology that can be used in job sites by bringing stripping and grinding technologies outdoors for the first time in the world with a laser that had only previously been used in factories.
Many bridges built during the period of rapid growth in Japan are at increasing risk of collapse due to rust that has advanced deeply into the bearing points and other important parts. Moreover, many of the fire accidents at petrochemical industrial complexes are due to deterioration from rust. There is an increasing need across the world to safely remove the harmful substances contained in paints and materials. Cool Laser removes stains using light. Accordingly, it has advantages such as prolonging the life of structures, improving workability and reducing the environmental burden,
Daiichi Cutter Kogyo participated in TOYOKOH’s series A round investment and intends to create new business. Currently, TOYOKOH has completed fundraising up to the series B round. In addition to Daiichi Cutter Kogyo, Maeda Corporation, Digital Information Technologies Corporation, NYK Line, Suzuyo Kensetsu Co., Ltd., Yamamoto Kogaku Co., Ltd. and The Shizuoka Bank, Ltd. have become investors and are supporting commercialization.
Daiichi Cutter Kogyo is one of those investors and is playing a role as a partner in operations. It is aiming to use laser technology to cultivate markets such as the removal and decontamination of rust on aging steel infrastructure structures.
It will continue to further strengthen its competitiveness by developing such new methods and technologies in addition to fine tuning existing methods in the future.
● Visualization of Technologies
The Company started research that contributes to the development of personnel from the fiscal year ended June 30, 2020.
In terms of the technologies handled by the Company, in addition to a large number of machines, it needs to provide custom-made operation each time because the operation environment differs at all job sites. There is a difficulty to maintenance and repair work unlike new construction. The level of technical capabilities is determined by the ability to respond flexibly in the situations where the conditions are all different from site to site, and the most appropriate response must be made for each.
Therefore, this is an area in which it is difficult to apply automation and other general-purpose technologies. The technical capabilities of individual craftsmen lead to superiority. Nevertheless, without being content with that, the Company has started efforts to improve the speed at which they acquire techniques by visualizing the techniques of skilled workers.
The Company visualizes the operation procedures of machines, systematizes the movement of the line of sight and mounts motion sensors to the heads, arms and lower backs of skilled workers. This allows it to analyze how they move, at what angle they move and at what speed they move.
In addition, the Company is working on visualizing the level of each worker who has learned the techniques of these skilled workers. It is developing an environment that produces spontaneous improvement in technical capabilities by preparing an achievement stage table and hand gun master system.

(From the materials of the Company)
● Expansion of the Development Structure
The Company had been using part of its head office premises to perform trial operations and operations relating to research and development. However, the number of projects brought to it by its customers has also been increasing in addition to its in-house development. This led to the space becoming cramped. Accordingly, the Company remodeled a large warehouse of approximately 1,800 m2 into a trial operation and research and development yard to further focus its efforts on promoting research and development.
The Company cites three hints to development: troubles of customers, troubles of itself and energy saving.
The Company is putting the troubles of each to the fore and promoting development with a sense of speed by working together with its customers, suppliers, universities and third parties (e.g., in-house/large general contractors and plant manufacturers) on a project basis.
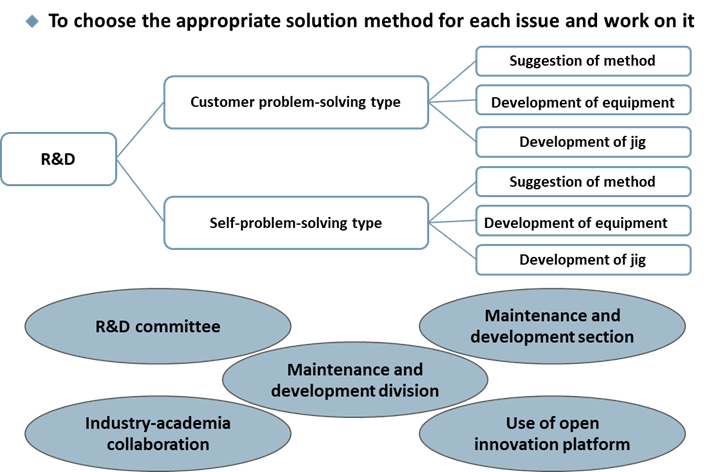
(From the materials of the Company)
Development Example
Hydro-Jet RD Method
This technology has been developed by three companies unitedly. . Tobishima Corporation and Daiichi Cutter Kogyo applied to take part in a communication-style joint study recruited by Hanshin Expressway Co., Ltd.
There was a challenge in removal technology. The replacement of slabs for synthetic girder bridges conventionally required a long closure period. It took time and effort to remove the cements between the steel girders and the concrete slabs.
Consequently, the Hydro-Jet RD method makes it possible to remove those cements in the preparation period up to the start date of the closure without traffic restrictions. There is no need to remove the cements after the start of the closure. This means it is possible to shorten the slab removal period and traffic restriction period by removing a large slab at one time wherever the steel girder is located.
3-5 Materialities in Risk Management and Governance Challenges
(1) Corporate Governance
The Company recognizes that improving its mid- to long-term corporate value by building a corporate governance structure in which it is possible to coexist with its stakeholders (e.g., customers, shareholders, local residents and employees) is an important management challenge.
The Company has an audit & supervisory board. It is looking to strengthen its management monitoring functions by electing outside auditors and outside directors to ensure transparency and soundness in management.
(Excerpt from the Corporate Governance Report: Updated on October 2nd, 2020) |
Principle 1-4. Strategically Held Shares The Company has a policy not to hold shares in principle. However, if it determines that maintaining and strengthening stable business relationships in total consideration of the nature and scale of transactions will contribute to the improvement of its corporate value, it may strategically hold the shares of its business partners. The Company’s board of directors annually examines whether the shares held by the Company contribute to an improvement of the Company’s corporate value. If it determines that the significance of the holding of shares no longer exists or has diminished as a result of its examination, the Company will proceed with selling the shares as deemed appropriate. Regarding the exercise of voting rights in shares held by the Company, the Company will exercise it after examining whether there is any possibility of damaging the concerned company's corporate value.
|
Supplementary Principle 4-11 (i). Overall Balance, Diversity and Size of the Board of Directors The Company’s way of thinking about the overall balance of knowledge, experience and abilities and diversity of the board of directors and the policies and procedures relating to the election of Directors is the same as its way of thinking on nominating candidates to be director. Therefore, these are as described in Principle 3-1 (iv). They are disclosed in the report on corporate governance. Moreover, the Company currently elects three internal directors, two outside directors (of these, both are independent outside directors), an internal auditor, and two outside auditors. This is in consideration of the appropriate size to promote a highly efficient management system. One of the outside directors is an expert in labor problems while the other serves as the representative director of another company and is well-versed in corporate management. In addition, the audit & supervisory board is comprised of a certified public accountant & tax counsellor, a CSR consultant and a person with a wealth of internal audit experience. The Company considers the overall balance of the board of directors so that it can achieve sound and sustainable growth. |
Principle 5-1. Policy on Constructive Dialogue with Shareholders The Company’s Corporate Planning Office serves as the department responsible for investor relations. It holds semiannual financial results briefings and individual meetings for shareholders and investors. In addition, the Company recognizes that building and maintaining relationships of trust with shareholders and investors is important to promote constructive dialogue with them. It also recognizes the appropriate information disclosure is indispensable for that. To put that awareness into practice, in addition to disclosure based on laws/ordinances, the Company actively discloses information on its website about its business strategies and situation. For example, it proactively discloses information (including non-financial information) it deems important to shareholders and other stakeholders. The formulation and disclosure of policies relating to the establishment of a structure and efforts to promote constructive dialogue with shareholders is a matter it will consider in the future. |
(2) Risk Management (Accidents and Laws/Ordinances)(i) Efforts to Ensure Safety
The Company is making the following efforts in addition to its training system to ensure the safety of its employees as introduced in “Human Capital.”
| Safety environment division | Operating headquarters | Offices |
Safety check on the projects involving block removal |
| ◎ | ○ |
Safety patrol (site observation) | ◎ | ◎ | ○ |
Check system of Legal inspection (machine, car, and drivers’ license) |
|
| ◎ |
Safety and health council (safety education) | ◎ |
| ○ |
Others (training related to safety) | ◎ | ◎ | ○ |
Accident handling | ◎ | ◎ | ○ |
◎:Leading division, ○:Related division
Training contents are incidental to site operations such as Dust operation, scaffold assembly, asbestos scattering prevention
(Provided by the Company)
Accidents are more likely to occur when performing the cutting work that accompanies the removal of concrete blocks. Therefore, the Company has built a structure to identify all projects involving the removal of concrete blocks from its more than 60,000 projects a year and to then check the consideration of their safety from the time when the project comes into existence (the time when planning starts or when a quotation is given) across multiple departments.
The Company aims to reflect changes to the methods and procedures that ensure safety in the planning stage. It also looks to for its craftsmen who actually perform the operation to do so with an awareness of the dangers by grasping the situation in advance.
Safety patrols are on-site patrols at job sites. The Company uses a special check sheet that clarifies the check points for each type of work it handles.
The sawing and drilling work performed by the group belongs to scaffolding/earthworks and civil engineering business that are subject to regulations by the Construction Business Act.
It is necessary to operate most of its corporate activities according to the Construction Business Act. Consequently, the Management Department is responsible for operations from the management of permits to the management of various qualifications. The Risk Management Committee, a separate independent organization, periodically identifies risks associated with the Company’s business activities. This structure is designed to perform efforts aimed at reducing risks.
4. Progress of Medium-term Business Plan (from FY2019 to FY2021) and future strategy
Outline of Medium-term Business Plan
DAI-ICHI CUTTER KOGYO is part subcontractors who dispatch engineers directly. However, it has established a unique position specializing in sawing and drilling work as a "specialized contractor," and the formation of a group of engineers with high technical capabilities essential for sawing and drilling work is the key to growth. For this reason, the Company’s Medium-term Business Plan is pursuing four basic strategies with a focus on human capital.
The quantitative targets for Sales, Profits, number of employees and others were achieved a year ahead of schedule in FY ended June 2020, but DAI-ICHI CUTTER KOGYO will continue to further strengthen its activities in the transportation infrastructure and industrial infrastructure sectors in the Sawing and Drilling Business (increasing the Sales Composition Ratio). In addition, growth investment (human capital, productivity improvement, expansion of business fields, and research and development) will continue. The Company will also fulfill its responsibilities for CSR and SDGs through a disaster recovery volunteer system and disaster support agreements with public institutions. Regarding transportation infrastructure and industrial infrastructure, the Company aims to raise the Sales Composition Ratio in the FY ending June 2024, 5 years later, to 50% (FY ended June 2018 living infrastructure: transportation infrastructure and industrial infrastructure = 56.9%: 43.1%).
4-1 Quantitative Targets
| FY 2019 Plan | FY 2019 Act. | FY 2020 Plan | FY 2020 Act. | FY2021 Plan |
Net Sales | 14,318 | 14,871 | 15,700 | 17,440 | 17,400 |
Operating Profit | 1,624 | 1,760 | 1,730 | 2,296 | 1,910 |
Operating Profit Margin | 11.3% | 11.8% | 11.0% | 13.2% | 11.0% |
Profit Attributable to Owners of Parent | 1,014 | 1,251 | 1,080 | 1,523 | 1,190 |
EPS | 178.24 | 219.80 | 189.75 | 267.73 | 209.08 |
|
|
|
|
|
|
Number of Employees (Consolidated) | 500 | 501 | 525 | 568 | 550 |
*Unit: Million-yen, yen, person
The quantitative targets for all items were achieved a year ahead of schedule in FY ended June 2020, the second year of the Medium-term Business Plan.
4-2 Sales Composition Ratio by Infrastructure
| FY 6/16 | FY 6/17 | FY 6/18 | FY 6/19 | FY 6/20 |
Living Infrastructure | 62.0% | 59.1% | 56.9% | 58.9% | 54.8% |
Transportation Infrastructure | 23.5% | 26.6% | 27.0% | 29.0% | 32.2% |
Industrial Infrastructure | 14.6% | 14.3% | 16.1% | 12.1% | 12.9% |
The sales composition ratio of transportation infrastructure is increasing year by year because the demand of measures against the deterioration of expressways (renewal of floor slabs and earthquake resistance), redevelopment of railways, and strengthening of airport functions due to increasing inbound tourists etc. were captured. As for anti-aging measures, we are proceeding with a sales strategy to secure systematic sales, and the results are becoming apparent.
4-3 Growth Investment
| Content | FY 2019 Act. | FY 2020 Plan | FY 2020 Act | FY 2021 Plan | 3 years accumulative |
Human Resource Development | Recruitment and Training | ¥170 million | ¥100 million | ¥200 million | ¥100 million | ¥470 million |
Productivity Improvement | Improvement of workplace environment and promotion of work style reforms | ¥400 million | ¥300 million | ¥410 million | ¥300 million | ¥1,110 million |
Expansion of Business Fields | Establishment of new offices, M&A | ¥120 million | ¥700 million | ¥870 million | ¥200 million | ¥1,190 million |
Research and Development | Investment in R&D and new technologies | ¥30 million | ¥50 million | ¥80 million | ¥50 million | ¥160 million |
Total | ¥720 million | ¥1,150 million | ¥1,560 million | ¥650 million | ¥2,930 million |
As a result of aggressively investing in human resources (engineers), the Company’s core competence, the actual result was 1.56 billion yen in FY ended June 2020, the second year of the Medium-term Business Plan. As a result of the acquisition of two companies in FY ended June 2020, the cumulative investment forecast for 3 years is expected to increase to 2.93 billion yen (when the Medium-term Business Plan was formulated, it was planned to be 2 billion yen in 3 years).
In research and development, DAI-ICHI CUTTER KOGYO released “ECOA,” an eco-friendly water pressure-driven drilling method (initiatives related to “Goal 6,” “Goal 9,” “Goal 14” and “Goal 15” in the 17 SDGs). Conventionally, hydraulic pressure (oil) was used to drive the machine, and oil scattering at the time of rupture was a big risk, but since ECOA is a water pressure-driven drilling, there is no risk of environmental pollution at the time of rupture. In addition, the Company is working on “visualization” of experienced workers’ skills. It has already completed the visualization of operation procedures and movements of eyes and body parts, and is now using it for employee training (initiatives related to “Goal 5,” “Goal 8” and “Goal 13” in the 17 SDGs).
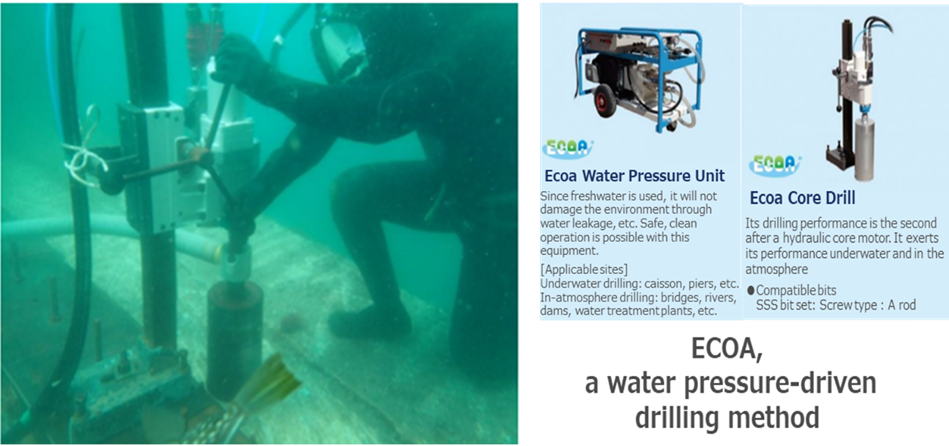
(Source: the reference material of the Company)
Investment Effect and Future Agendas
Regarding human resources development, mid-career recruitment improved, and the retention rate increased. The Company intends to support recruitment activities by further improving the working environment, and to further improve the retention rate by diversifying career paths. Regarding productivity improvement, the monthly volume index (target 1.7 million yen ⇒ actual 2.04 million yen) and productivity per unit time (target 1,700 yen ⇒ actual 17,019 yen), which are KPIs, improved. In the future, it will be necessary to achieve results with optimized placement for reducing working hours. In research and development, DAI-ICHI CUTTER KOGYO will use ECOA, an eco-friendly water pressure-driven drilling method the Company has developed at actual worksites to generate Sales. In expansion of business fields, the Company strengthened the private sector and the industrial infrastructure units through M&A and will continue to gather M&A related information and promote overseas business expansion with a focus on plants.
4-4 SDGs Activities
DAI-ICHI CUTTER KOGYO aims to contribute to the achievement of the SDGs based on the idea that “as a player who supports social infrastructure, contributions to stakeholders including local communities are the repayment of favors and are indispensable for continuing its business in the future.” Specifically, the Company provides “Takeout Subsidy” to employees (initiatives related to “Goal 8,” “Goal 11” and “Goal 17” in the 17 SDGs), and intermediate processing services with carbon offset (initiatives related to “Goal 6,” “Goal 11,” “Goal 12” and “Goal 13” in the 17 SDGs).
The Takeout Subsidy encourage employees to use nearby restaurants to support small restaurants in the area suffering from the COVID-19 outbreak. Meanwhile in the intermediate treatment service with carbon offset, carbon offset is applied to the intermediate treatment service of slurry generated during the cutting process. DAI-ICHI CUTTER KOGYO provides free carbon offset as an ancillary service for the collection and treatment of slurry. While the intermediate disposal service for slurry alone reduces the environmental burden, the Company aims to further contribute to the global environment.
4-5 Future Strategy
While responding to the impact of the COVID-19 infection, DAI-ICHI CUTTER KOGYO will continue to work on human resource strategy, productivity improvement, research and development, and expanding business fields.
Impact of the COVID-19 Outbreak and Countermeasures
Both the private and public orders are expected to gradually fall. However, since orders for anti-aging repairment is expected to be more stable than construction for other purposes including new construction, the business policy of the Medium-term Business Plan (focus on transportation and industrial infrastructure) is considered to be effective even as a countermeasure against COVID-19 and will be continued. DAI-ICHI CUTTER KOGYO will also build a business structure to minimize the impact of employee infection. The Company will aim to minimize close contact in its business activities, specifically through remote work for employees other than engineers, online meetings, measures to prevent droplet infection, minimization of contact between outside and inside work, maintenance of action records, abolition of gathering events across regions and others. In addition, the Company will continue employee training after taking measures against infectious diseases.
Human Resources Strategy
DAI-ICHI CUTTER KOGYO will promote work style reforms and a work-life balance project in line with the industry standards. In work style reforms, the Company will promote a work style reform that precedes the following industry regulations from the viewpoint that it is necessary to complete an attractive workplace compared to other industries in order to secure human resources.
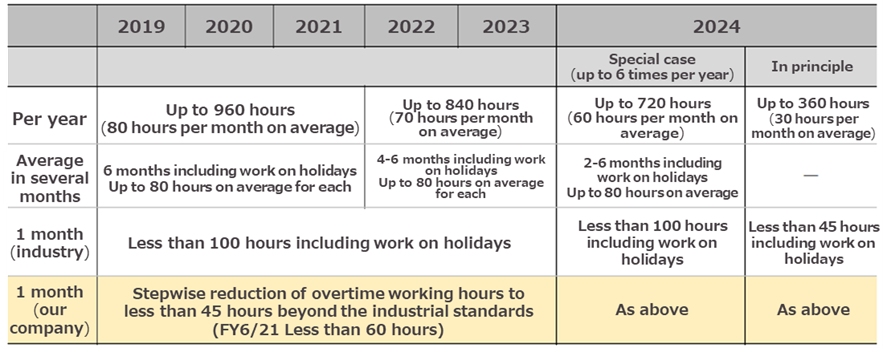
(Source: the reference material of the Company)
Furthermore, in the work-life balance project, the Company aims not only to comply with overtime regulations but also to pursue a more attractive working style compared to other industries.
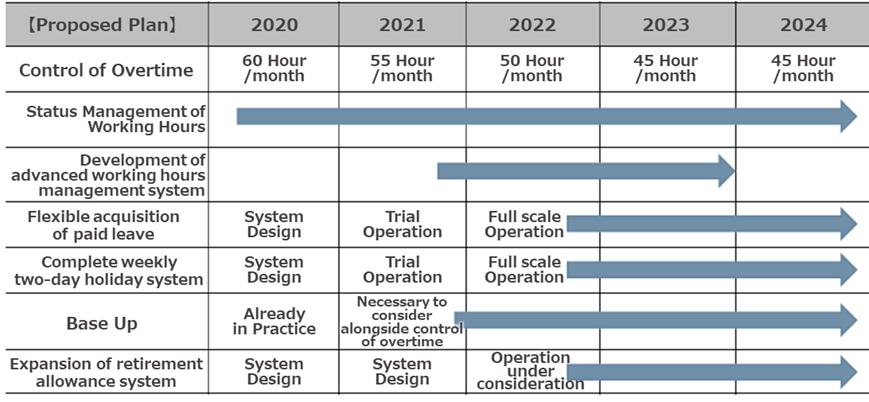
(Source: the reference material of the Company)
In addition to the above, in order to improve productivity, DAI-ICHI CUTTER KOGYO is building a system that can handle everything from sales activities to orders/dispatch management, slip creation, billing processing, and credit management. In research and development, the Company will increase the size of the trial operation/R&D yard and develop new methods and new technologies through the project method. In expanding the business fields, the Company will promote overseas business expansion and M&A. In overseas business expansion, the Company will focus its research on plants in Southeast Asia. In M&A, the Company will target specialized contractors with the 5 keywords of cutting, chipping, cleaning, stripping, and grinding, companies operating around the construction in the supply chain (research, designing, and maintenance), and companies with specialized technologies, systems, and clients.
5. Financial and non-financial data
(1) Financial data
◎BS/PL
| FY 6/16 | FY 6/17 | FY 6/18 | FY 6/19 | FY 6/20 |
Sales | 12,857 | 12,840 | 16,283 | 14,871 | 17,440 |
Operating profit | 1,733 | 1,412 | 2,187 | 1,760 | 2,296 |
Ordinary profit | 1,780 | 1,473 | 2,263 | 1,843 | 2,482 |
Net profit | 1,115 | 990 | 1,487 | 1,251 | 1,523 |
EPS (¥) | 196.01 | 174.01 | 261.37 | 219.80 | 267.73 |
ROE(%) | 16.9 | 13.1 | 17.0 | 12.5 | 13.5 |
ROA(%) | 19.4 | 14.5 | 19.4 | 14.2 | 17.2 |
Total assets | 9,737 | 10,597 | 12,707 | 13,304 | 15,533 |
Net assets | 7,396 | 8,333 | 9,822 | 10,956 | 12,548 |
Capital-to-asset ratio (%) | 73.2 | 75.9 | 74.3 | 79.3 | 77.1 |
*Unit: million yen
◎CF
| FY 6/16 | FY 6/17 | FY 6/18 | FY 6/19 | FY 6/20 |
Operating CF | 1,354 | 913 | 2,224 | 1,231 | 2,515 |
Investing CF | -825 | -594 | -622 | -649 | -1,699 |
Free CF | 529 | 319 | 1,602 | 581 | 815 |
Financing CF | -90 | -113 | -140 | -179 | -198 |
Cash and cash equivalents | 3,628 | 3,834 | 5,295 | 5,698 | 6,316 |
*Unit: million yen
(2) Non-financial data
① Social capital-related data
| FY 6/16 | FY 6/17 | FY 6/18 | FY 6/19 | FY 6/20 |
Number of shareholders | 1,774 | 4,086 | 4,015 | 2,644 | 2,298 |
Number of partner companies | 1,330 | 1,379 | 1,420 | 1,470 | 1,513 |
Number of customers | 6,481 | 6,538 | 6,565 | 7,136 | 6,932 |
② Employee capital-related data (Non-consolidated basis)
| FY 6/16 | FY 6/17 | FY 6/18 | FY 6/19 | FY 6/20 |
Number of employees | 336 | 347 | 359 | 364 | 390 |
Of these, the number of female employees | 28 | 27 | 29 | 30 | 38 |
Ratio of female employees | 8.33% | 7.78% | 8.08% | 8.24% | 9.74% |
Number of new employees | 21 | 25 | 26 | 28 | 46 |
Number of retirees (including those at retirement age) | 32 | 27 | 20 | 41 | 22 |
Number of retirees within three years of joining the Company | 29 | 13 | 7 | 21 | 11 |
Ratio of the those retiring within three years of joining the Company* | 37.7% | 17.1% | 9.7% | 26.6% | 11.0% |
Employment continuation rate of new graduate employees* | 88.5% | 93.1% | 100.0% | 84.4% | 89.2% |
*Ratio of those retiring within three years of joining the Company: number of retirees ÷ number of employees joining the Company over the last three years
*Employment continuation rate of new graduate employees: number of new graduate employees who survived over the last three years ÷ total number of those employed in the same period
| FY 6/16 | FY 6/17 | FY 6/18 | FY 6/19 | FY 6/20 |
Number of projects | 59,219 | 59,169 | 60,225 | 64,415 | 62,044 |
Number of work accidents (Including partner companies) | 54 | 39 | 46 | 47 | 45 |
Number of work accidents (lost time of four or more days –personal injuries including partner companies) | 5 | 3 | 0 | 6 | 1 |
Ratio of work accidents with lost time of four or more days* | 0.005% | 0.003% | 0.000% | 0.006% | 0.000% |
*Number of work accidents during the period with lost time of four or more lost days ÷ Number of projects during the period
<For reference>
For publishing ESG Bridge Report, the company enlisted significant cooperation from Mr. Ryohei Yanagi (PhD. in economics from Kyoto University, Executive Vice President and CFO of Eisai Co., Ltd., and a visiting professor of Graduate School of Accountancy, Waseda University).
This section mentions the purpose of publishing ESG Bridge Report and outlines the “Yanagi-Model” proposed by Mr. Yanagi, while citing a passage from his literature “CFO Policy 2nd edition.”
(1) Regarding ESG Bridge Report
While ESG investment became mainstream, investors demand that Japanese companies disclose ESG information proactively. Accordingly, an increasing number of companies produce integrated reports.
However, the production of integrated reports requires the understanding and involvement of executives, some human resources and some budgets. Accordingly, many companies still cannot produce integrated reports.
Also, for producing integrated reports, it is necessary to take many steps, including the summarization of various data, the identification of materiality, and the setting of indicators and goals. It seems that many companies are not prepared enough, so they are reluctant.
However, Mr. Yanagi mentioned, in “CFO Policy 2nd edition,” that “if Japanese enterprises shed light on their potential ESG value, their PBR will probably be at least the same level (around 2x) as that of companies in the UK” and “by actualizing Yanagi-Model, it is possible to double the value of Japanese companies, probably improving investment, employment, and pensions and maximizing national wealth, which have a high probability.” Investment Bridge Co., Ltd. considers that the provision of ESG information of Japanese companies is meaningful for the entire Japan and should be promoted actively.
Under these circumstances, for companies who deeply recognize the necessity to disclose ESG information although they still cannot produce integrated reports, our company cooperatively produces “ESG Bridge Report” based on currently available data and resources, to provide investors with ESG information as needed by investors as much as possible.
Japan Exchange Group actively encourages Japanese companies to disclose EGS information, and published “Practical Handbook for ESG Disclosure.” Page 6 of this handbook mentions “We do not mean that you cannot disclose information unless all of the elements mentioned here are covered. We expect that this handbook will provide you with some clues when you start with what you can do while considering your situation for disclosing ESG information to communicate with investors and proceed with more initiatives.” We believe that “ESG Bridge Report” is a tool for “starting with what you can do for disclosing ESG information.”
Mr. Yanagi mentioned that in order to achieve full-scale Yanagi-Model, it is necessary to conduct empirical research indicating positive correlation between ESG and corporate value and disclose concrete cases in which companies’ contribution to society helps increase long-term economic value. Accordingly, the actual hurdle is high, but we would like to explicitly describe how ESG initiatives of each company lead to the improvement in corporate value.
Based on the feedback from many investors who have read our reports, we would like to improve the quality of our reports. We would appreciate your candid opinions.
Kaoru Hosaka
Managing Director and Chairman
Investment Bridge Co., Ltd.
k-hosaka@cyber-ir.co.jp
(2) Regarding “Yanagi-Model”
(Increasing value of non-financial capital, rapid increase of ESG investment, and production of a conceptual framework for connecting ESG and corporate value)
Recently, many empirical studies have verified the increase in importance of non-financial information in corporate value evaluation, and it can be inferred that invisible value (intangible assets) and non-financial capital value account for about 80% of corporate value.
In addition, it can be considered, from the results of many empirical studies on the relation between non-financial information and corporate value, that ESG may be positively correlated with corporate value.
On the other hand, as ESG investment is becoming mainstream globally, Japanese enterprises, whose PBR is less than one or stagnant in many cases although they have latent ESG value, need to transform non-financial capital into future financial capital with the “Yanagi-Model” for raising PBR, or produce and disclose a conceptual framework for connecting ESG and corporate value.
(Overview of the “Yanagi-Model”)
Out of shareholder value, the book value of shareholders’ equity, which corresponds to “the part where PBR = 1,” is composed of current financial capital and financial value.
On the other hand, out of shareholder value, market value added, which corresponds to “the part where PBR exceeds 1,” is composed of non-financial capital (which can be said to be future financial capital), and the sum of current value of cash flow of equity spread (= ROE – Cost of shareholders’ equity) in the residual profit model.
Therefore, Mr. Yanagi proposed “the synchronization model of non-financial capital and equity spread” = “Yanagi-Model” as a conceptual framework for synchronizing ESG and corporate value, as a result of non-financial strategy.
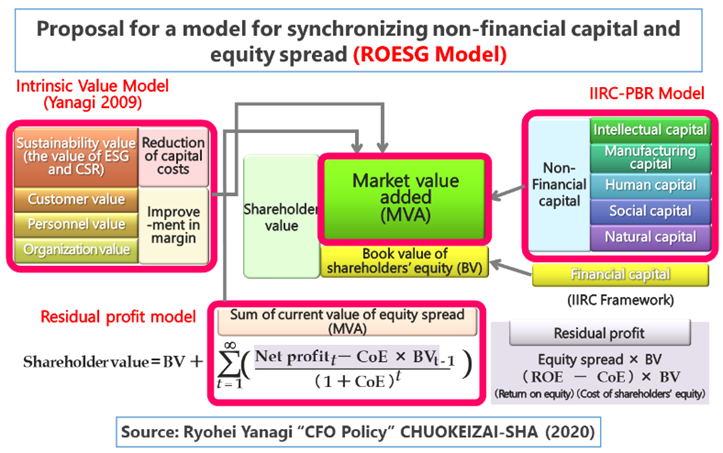
In the “Yanagi-Model,” non-financial capital has a mutually complementary relation with equity spread, which is the sum of current value of residual profit through “market value added.” Namely, the value creation with equity spread is consistent in the long term because of the delay, via the creation of value of non-financial capital, including ESG, and market value added.
Therefore, ESG management can be synchronized with long-term investors, who demand capital efficiency, via marked value added, and cooperation is possible.
According to Mr. Yanagi’s survey on investors for supporting the model, many investors around the world demand that “the relation between ESG and ROE values is explained” and answered that “100% or a significant proportion of the value of ESG is taken into account in PBR.” It can be considered that the “Yanagi-Model” is supported directly or indirectly by most of long-term investors.
(For details about his “Yanagi-Model,” refer to “CFO Policy 2nd edition” authored by Ryohei Yanagi, CHUOKEIZAI-SHA (2021).)
The purpose of this report is to provide information only and not for soliciting or promoting you to make investments. The information and opinions contained in this report are provided by our company based on data which are publicly available. The information in this report is based on the sources that we judge to be reliable. However, we cannot wholly guarantee the accuracy or completeness of the data. We do not guarantee the accuracy, completeness or validity of the information and opinions, nor do we bear any responsibility for the same. All rights relating to this report belong to Investment Bridge Co., Ltd., which may change the contents thereof at any time without prior notice. All investment decisions shall be made by the responsibility of individuals with thorough consideration.
Copyright(C) 2021 Investment Bridge Co., Ltd. All Rights Reserved.