Bridge Report: (1433) BESTERRA
![]() President Yoshihide Yoshino | BESTERRA CO., LTD. (1433) |
![]() |
Company Information
Market | TSE 1st Section |
Industry | Construction business |
President | Yoshihide Yoshino |
HQ Address | Kiba Park Bldg, 3-2-6 Hirano, Koto-ku, Tokyo, Japan |
Year-end | End of January |
Homepage |
Stock Information
Share Price | Share Outstanding (exc. Treasury Stock) | Market Cap. | ROE (Act.) | Trading Unit | |
1,434yen | 8,226,770shares | 11,797 million yen | 23.8% | 100 shares | |
DPS (Est.) | Dividend Yield (Est.) | EPS (Est.) | PER (Est.) | BPS (Act.) | PBR (Act.) |
16.00 yen | 1.1% | 44.61 | 32.1x | 317.49 yen | 4.5x |
*The share price is the closing price on March 18. The number of shares issued was taken from the latest brief financial report. ROE and BPS are the values of the pervious term.
Consolidated Earnings
Fiscal Year | Net Sales | Operating Income | Ordinary Income | Net Income | EPS | DPS |
Jan. 2015 (Actual) | 3,060 | 384 | 388 | 219 | 36.48 | - |
Jan. 2016 (Actual) | 3,846 | 447 | 464 | 292 | 42.85 | 90.00 |
Jan. 2017 (Actual) | 4,182 | 397 | 404 | 271 | 32.85 | 40.00 |
Jan. 2018 (Actual) | 4,496 | 386 | 373 | 263 | 31.69 | 15.00 |
Jan. 2019 (Actual) | 4,927 | 497 | 495 | 621 | 75.25 | 15.00 |
Jan. 2020 (Forecast) | 5,700 | 525 | 521 | 367 | 44.61 | 16.00 |
*From the term ending January 2019, consolidated performance will be posted, and net income means profit attributable to owners of parent (hereinafter called “net income.”)
* Stock split 1:4 in May 2015, 1:2 in February 2016. 1:3 in February 2017 (EPS has been revised retrospectively)
*unit: million yen, yen
This Bridge Report reviews on the outlook of BESTERRA’s earnings results for the fiscal year January 2019 and its business plans from fiscal year January 2020.
Table Contents
Key Points
1.Company Overview
2.Fiscal Year January 2019 Earnings Results
3.Fiscal Year January 2020 Earnings Forecasts
4.Medium-term management plan 2021 (from the term ending January 2020 to the term ending January 2020
5.Conclusions
<Reference: Regarding Corporate Governance>
Key Points
- For the fiscal year ended January 2019, sales and operating income increased 9.6% and 28.8% respectively from non-consolidated results of the previous year. Although large-scales projects in the petroleum/petrochemical industry, which boosted the construction revenue in the previous term, declined, sales in the electricity industry, where equipment efficiency is being improved, grew largely and were also healthy in the steel and gas industries. Gross profit margin improved due to highly-profitable projects, and absorbed the increases in selling, general and administrative expenses. The company plans to pay a term-end dividend of 10 yen/share (15 yen/share per year combined with the dividend at the end of the first half).
- Sales are expected to increase 15.7% year on year, and operating income is projected to grow 5.5% year on year in the fiscal year ending January 2020. While sales in the electric power industry are projected to continue rising, sales in the petroleum/petrochemical industry, which declined in the previous term, are forecasted to improve. As for profits, increased recruitment and personnel costs resulting from active recruitment, as well as R&D investments and other investments in creating a framework that ensures a safe working environment, etc. will be absorbed. The company plans to pay a dividend of 16 yen/share, up 1 yen from the previous term.
- For the foreseeable future, business performance will depend on the development of human resources, but the business environment is sound. The demand for dismantlement and upgrade is expected to rise as a result of deterioration of equipment established after the period of rapid economic growth, economic obsolescence, reorganization of companies, overseas transfer, etc. Also, the number of nuclear reactors to be decommissioned is forecasted to grow with the progress of conformity assessment of the new regulatory standards. Dismantlement of nuclear power generators is challenging as it must be carried out efficiently while preventing radiation exposure, but its potential demand is high. As for decommissioning, the surrounding equipment of nuclear reactors must be dismantled first, which is the same process as it is for the thermal power generators. It will be a task as well as the focus point for the company to quickly materialize the effects of collaborating with Hitachi Plant Construction and DAI-ICHI CUTTER KOGYO with the business related to dismantlement of nuclear reactors in mind.
1. Company Overview
As a specialist in plant dismantlement, BESTERRA manages the dismantlement of plants (metal structures) for iron-making, power generation, gas, petroleum, etc. Its core competence is “the method and technology for dismantling plants,” and it has many patented methods including international patents. The company concentrates its managerial resources on engineering (proposal, design, and work planning) and management (supervision and work management), and outsources actual dismantlement work to its affiliates, and so it does not own heavy machinery or construction teams (the risk of owning assets can be avoided), and it is unnecessary to procure materials, etc. and make transactions for material production (the inventory risk can be avoided). The corporate name “BESTERRA” was coined by combining the English word “Best (the superlative of ‘good’)” and the Latin word “Terra (the earth),” and infused with the hope of “making the earth splendid.”
1-1 Corporate ethos and the code of conduct
Under the corporate ethos “We will contribute to the earth environment with our flexible way of thinking, creativity, and technologies using these concepts,” the company enacted the following code of conduct.
Code of conduct
We will fulfill our responsibilities as professionals.
We constantly develop new technologies, “put a higher priority on safety than anything else,” and offer our services to clients while increasing assurance under the motto “Swifter, more affordable, and safer.”
1-2 Trend of performance
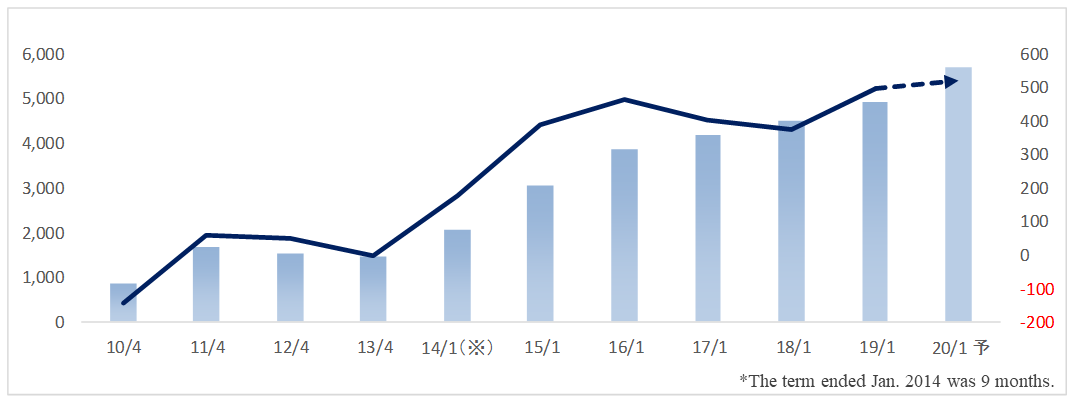
1-3 Characteristics of the business
The plant dismantlement business accounts for over 97% of total sales (the company also offers staffing services, etc.). The clients for plant dismantlement are leading companies that own plants for ironmaking, electric power, gas, petroleum, etc. In most cases, the equipment installation companies of the corporate groups of clients or leading general contractors are entrusted with dismantlement, and then BESTERRA serves as the primary or second-tier subcontractor. In the term ended January 2019, electric power companies accounted for 35% (22% in the term ended January 2018), steelmakers 41% (37% in the previous term), petroleum/petrochemical companies 9% (27% in the previous term), gas companies 14% (13% in the previous term), and other manufacturers 1% (1% in the previous term).
The company sticks to fabless management, in which it does not own necessary heavy machinery or engineers for dismantlement (so that they can handle any kinds of equipment of plants that have complex structures).
1-3-1 Flowchart for order receipt and outsourcing
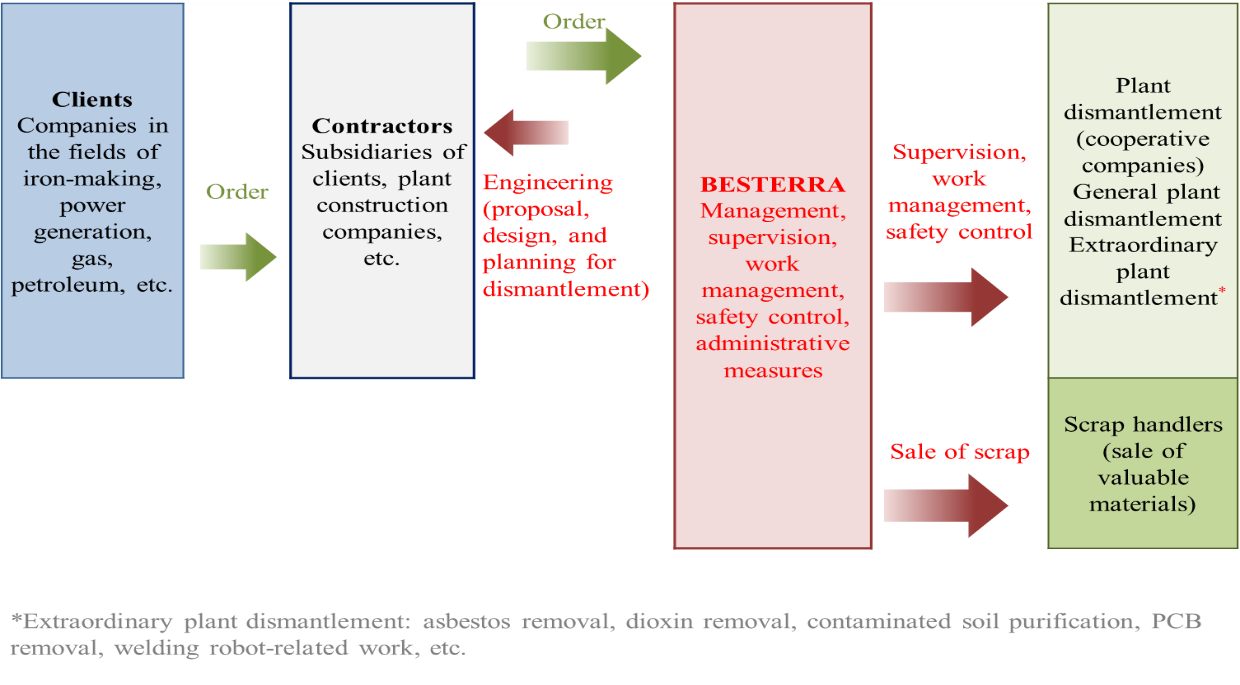
BESTERRA receives valuable materials generated through dismantlement, such as scrap, and sells them to scrap handlers. Accordingly, the company estimates the value of valuable materials while comprehensively considering material, quantity, price (market price of each material, such as iron, stainless steel, and copper), etc. and negotiates with clients about the fee for dismantlement work. In accounting, the gain from sale of valuable materials is included in revenue from dismantlement work, and posted as part of sales from completed dismantlement work. In some cases, contractors (clients) dispose of (sell) scrap, etc. by themselves.
1-3-2 Amount of completed work (rough estimates)
| FY 1/18 (non-consolidated) | Ratio to sales | FY 1/19 (consolidated) | Ratio to sales | YOY |
Electric power | 975 | 22% | 1,667 | 35% | +71% |
Steelmaking | 1,639 | 37% | 1,952 | 41% | +19% |
Petroleum/petrochemical | 1,196 | 27% | 429 | 9% | -64% |
Gas | 576 | 13% | 667 | 14% | +16% |
Other | 44 | 1% | 48 | 1% | +9% |
Amount of completed work | 4,429 | 100% | 4,761 | 100% | +7% |
*unit: million yen
1-4 Strengths: an excellent client base, efficient dismantlement management based on plenty of experience, and intellectual property, such as patented methods
The strengths of the company are excellent client assets, efficient dismantlement management based on plenty of experience, and intellectual property, such as patented methods. Because the clients are basically engineering subsidiary companies of leading companies in ironmaking, electric, gas and coal oil fields, which are easily trustable excellent clients, and it is predicted that they will receive orders continuously. The clients of the leading companies highly evaluate its company’s total management (low cost and high efficiency) of plant dismantlement that it cultivated experiences for 40 years, and it elect a barrier to entry. Furthermore, the company possesses a variety of technologies and know-how, which have been accumulated through environmental work, etc. (14 patents granted and 7 patents pending).
Concerning 2 revenue recognition methods and seasonality of revenue recognition.
There are 2 revenue recognition methods for construction contracts: 1) a completed-contract (CC) method in which revenue is recorded at the end of the construction, and 2) a percentage-of-completion (PC) method in which revenue is recorded as construction progresses. For the projects from which valuable materials, such as scrap, are generated through plant dismantlement, the company basically applies the PC method to large-scale projects whose contract amount exceeds 50 million yen and whose period exceeds 3 months (from the term ended January 2018), and the CC method to other projects. Meanwhile, the timing of revenue recording (completion of construction) using the CC method is often influenced by facility investment plans of the clients. In case of the company, the revenue is often recorded during the first quarter (February to April) and the fourth quarter (November to January) (seasonality of revenue recognition). With this method, however, changes of quarterly results may mislead investors、Therefore, the company is expanding the scope of application of the PC method step by step, and makes continuous efforts to smooth revenue.
2. Fiscal Year January 2019 Earnings Results
2-1 consolidated results
| FY 1/18 (non-consolidated) | Ratio to sales | FY 1/19 (consolidated) | Ratio to sales | YOY | FY 1/19 (non-consolidated) | YOY |
Sales | 4,496 | 100.0% | 4,927 | 100.0% | +9.6% | 4,826 | +7.3% |
Gross profit | 904 | 20.1% | 1,054 | 21.4% | +16.6% | 1,041 | +15.2% |
SG&A expenses | 518 | 11.5% | 556 | 11.3% | +7.3% | 532 | +2.8% |
Operating income | 386 | 8.6% | 497 | 10.1% | +28.8% | 509 | +31.9% |
Ordinary income | 373 | 8.3% | 495 | 10.0% | +32.7% | 506 | +35.6% |
Net income | 263 | 5.9% | 621 | 12.6% | +136.1% | 632 | +139.8% |
|
*Figures include reference figures calculated by Investment Bridge Co., Ltd. Actual results may differ (applies to all tables in this report)
*unit: million yen
Sales and operating income grew 9.6% and 28.8%, respectively, from non-consolidated results of the previous year.
Sales improved 9.6% from non-consolidated results of the previous year to 4,927 million yen. Large-scale dismantlement projects of ethylene production equipment increased amount of completed projects in the previous term. Sales in the petroleum/petrochemical industry decreased 64%, but sales in the electricity industry, where equipment efficiency is being improved, grew largely by 70% and also increased almost 20% in the steel industry. Sales marked a record high.
In terms of profit, SG&A rose because of posting of head office relocation and rental expenses to improve the efficiency of assets (company-owned building ⇒ on rent), but they were absorbed by gross profit margin that improved due to increased sales and number of highly profitable projects. Operating income marked a record high with 497 million yen, up 28.8% year on year. Net income exceeded the ordinary income as gains from the sale of noncurrent assets (the head office building) amounting to 388 million yen were recorded as extraordinary income.
The company plans to pay a term-end dividend of 10 yen/share and the annual dividend will be 15 yen/share per year combined with the dividend at the end of the first half.
2-2-1 Completion of projects (estimates)
| construction of completion | Ratio to sales | YOY | New Orders | Ratio to sales | YOY |
Electric power | 1,659 | 35% | +70% | 275 | 27% | -69% |
Steelmaking | 1,928 | 41% | +18% | 429 | 42% | -52% |
Petroleum/petrochemical | 429 | 9% | -64% | 224 | 22% | +40% |
Gas | 699 | 14% | +21% | 51 | 5% | -81% |
Other | 48 | 1% | +9% | 40 | 4% | +82% |
Amount of completed work | 4,761 | 100% | +8% | 1,019 | 100% | -54% |
*unit: million yen
2-2-2 Amount of orders received and the backlog of orders
| FY 1/18 | FY 1/19 | YOY (end of the same term) |
Backlog of orders at the beginning of the term | 2,303 | 2,218 | -3.7% |
Amount of orders received | 4,344 | 3,565 | -17.9% |
Amount of completed projects | 4,429 | 4,761 | +7.5% |
Backlog of orders at the end of the term | 2,218 | 1,021 | -53.9% |
*(unit: million yen)
Backlog of orders at the end of the term declined temporarily as the amount of completed projects increased over the term-end, but the number of inquiries remained heathy with a large number of expected orders.
2-2-3 Breakdown of SG&A (individual results are shown in brackets)
| FY 1/18 (non-consolidated) | Ratio to sales | FY 1/19 (consolidated) | Ratio to sales | YOY | Major change factor |
Salaries and allowances | 271 | 6.0% | 280 (268) | 5.7% | 5.7% | Increase of employees, excluding dismantlement supervisors, and subsidiaries |
R&D cost | 8 | 0.2% | 9 (9) | 0.2% | 0.2% | Robot development |
Commissions and remunerations paid | 66 | 1.5% | 52 (51) | 1.1% | 1.1% | Decrease in cost for changing stock markets |
Recruitment cost | 15 | 0.3% | 12 (12) | 0.2% | 0.2% | Decrease in commission for introduction of workers and ad media |
Advertisement | 13 | 0.3% | 17 (17) | 0.3% | 0.3% | Increase of exhibitions held |
Other | 142 | 3.2% | 182 (172) | 3.7% | 3.7% | Head office relocation and rental expenses |
Total SG&A expenses | 518 | 11.5% | 556 (532) | 11.3% | 11.3% | *2.8% increase year on year on a non-consolidated basis |
*unit: million yen
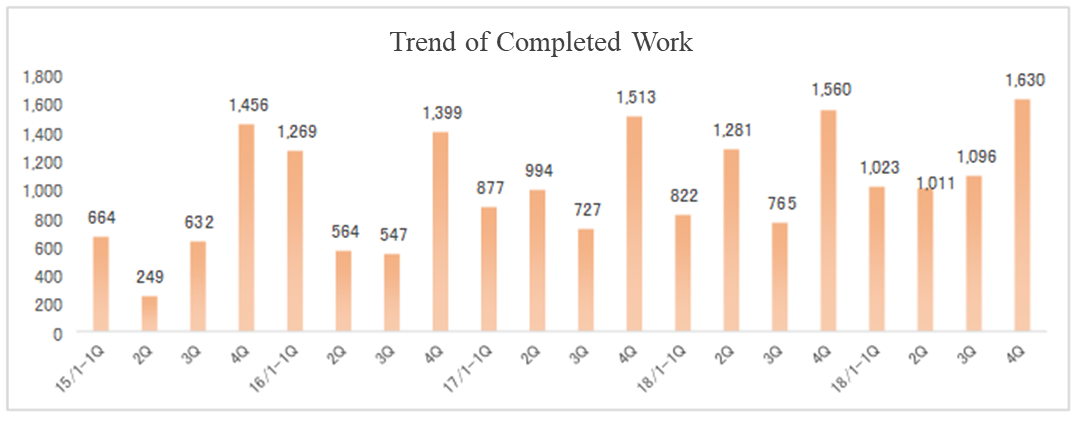
2-3 Financial condition and cash flow(CF)
2-3-1 Financial condition
| Jan. 18 | Jan. 19 |
| Jan. 18 | Jan. 19 |
Cash | 752 | 2,032 | Payables | 820 | 1,357 |
Receivables | 2,570 | 1,785 | Taxes Payable | 23 | 250 |
Current Assets | 3,521 | 4,112 | Borrowings | 450 | 7 |
Tangible Assets | 325 | 265 | Liabilities | 1,572 | 1,949 |
Investments, Others | 46 | 159 | Net Assets | 2,332 | 2,614 |
Noncurrent Assets | 383 | 451 | Total Liabilities, Net Assets | 3,905 | 4,564 |
*unit: million yen
Free CF increased from 365 million yen in the previous term to 2,051 million yen due to a high proportion of sales in the electricity industry, whose accounts were settled in cash, and sale of noncurrent assets. While repayment of borrowings progressed and some portion of surplus funds was invested in safe assets (investment securities), cash and deposits rose significantly. Accounts payable augmented as the amount of dismantlement projects increased. Capital adequacy ratio was 57.2%.
2-3-2 Cash Flow(CF)
| FY 1/18 (non-consolidated) | FY 1/19 (consolidated) | YOY | |
Operating Cash Flow(A) | 369 | 1,753 | +1,384 | +374.5% |
Investing Cash Flow(B) | -4 | 298 | +302 | - |
Free Cash Flow (A+B) | 365 | 2,051 | +1,686 | +462.0% |
Financing Cash Flow | -314 | -777 | -462 | - |
Cash and Equivalents at Term End | 752 | 2,031 | +1,278 | +169.8% |
*unit: million yen
Reference: Trend of ROE and ROA
| FY 1/15 | FY 1/16 | FY 1/17 | FY 1/18 | FY 1/19 |
ROE | 21.89% | 18.43% | 12.81% | 11.7% | 23.81% |
ROA | 9.41% | 10.26% | 7.28% | 6.49% | 13.63% |
Net income margin | 7.18% | 7.60% | 6.59% | 5.96% | 12.62% |
Total asset turnover [times] | 1.31 | 1.35 | 1.10 | 1.09 | 1.08 |
Leverage [times] | 2.33 | 1.80 | 1.76 | 1.8 | 1.75 |
*ROE = Net income margin × Total asset turnover × Leverage
*ROA = Net income margin x Total asset turnover
*Total asset and Equity are the average balance in the term. Equity Ratio which was mentioned in Finacial Statements and Finacial Repor is calculated by the balance at the term end, therefore that inverse number and the above Leverage are not necessarily corresponding.
3. Fiscal Year January 2020 Earnings Forecasts
Consolidated Earnings
| FY 1/19 | Ratio to sales | FY 1/20 (forecast) | Ratio to sales | YOY |
Sales | 4,927 | 100.0% | 5,700 | 100.0% | +15.7% |
Operating income | 497 | 10.1% | 525 | 9.2% | +5.5% |
Ordinary income | 495 | 10.0% | 521 | 9.1% | +5.2% |
Net income | 621 | 12.6% | 367 | 6.4% | -41.0% |
*unit: million yen
Sales and operating income are expected to grow 15.7% and 5.5% year on year, respectively.
Sales are projected to increase 15.7% year on year to 5.7 billion yen. Sales in the electric power industry, which is reviewing its equipment to improve efficiency, are expected to continue growing, and sales in the petroleum/petrochemical industry, which declined in the previous term, are forecasted to rise.
Operating income is expected to augment 5.5% year on year to 525 million yen. The company plans to increase the number of employees from 66 in the previous term to 92 at the end of the current term (no. of dismantlement supervisor will increase from 32 to 47) through active recruitment for its business expansion. In addition to the increase in personnel and recruitment costs due to the increase the number of employees, investments for further growth are also expected to rise, such as in R&D related to new methods of dismantlement, recruitment activities and improvement of the work environment (creating a framework that ensures a safe work environment), and installment of a system realizing an efficient operational control. As a result, the growth of operating income is projected to be lower than the previous term’s result, but will continue to mark a record high.
As the company specializes in construction management of dismantling work, there is a need to place a supervisor in every construction site. Therefore, it is necessary to hire more dismantlement supervisors for the company’s sustainable growth and the company as a whole will engage in recruitment activities in order to achieve the medium-term management plan.
The company plans to pay a term-end dividend of 10 yen/share, and the annual dividend will be 16 yen/share combined with the dividend amounting to 6 yen/share (up 1 yen) at the end of the first half (projected dividend rate: 35.9%). It plans to provide a stable dividend with a target dividend rate of 40%.
4. Medium-term management plan 2021 (from the term ending Jan. 2020 to the term ending Jan. 2022)
4-1 Numerical goals
| FY 1/20 | FY 1/21 | FY 1/22 |
Sales | 5,700 | 6,400 | 7,200 |
Operating income (Rate) | 525(9.2%) | 570(8.9%) | 650(9.0%) |
Ordinary income | 521 | 566 | 645 |
Net income | 367 | 403 | 457 |
*unit: million yen
BESTERRA’s medium-term management plan uses a rolling system, in which the plan is reviewed and revised every term in order to deal flexibly with changes in the business environment. The basic strategy of the 2021 medium-term management plan (which began in the term ending January 2020) is to restructure earning and human resources systems, pursue the value of the 3D business, and consider M&As as basic strategies. The company aims to achieve sales and profit growth of 10% or greater, with sales of 7.2 billion yen and an operating income of 650 million yen in the term ending January 2022.
4-2 Approaches in the term ending January 2019 Profit structure reform, Personnel structure reform, Pursuit of 3D business values, M&A strategy
4-2-1 Reform of the earnings structure
The company will expand the number and scale of projects for which it receives orders, enrich demolition methods, and strengthen its sales capabilities.
Increase in the number and scale of projects for which the company receives orders
Companies with heavy industrial plants are the backbone of the Japanese industry. BESTERRA proposes safe and innovative dismantling work to these companies, aiming to maximize the plant dismantling business. Specifically, individual targets and strategies will be set for the fields of “electric power,” “steel,” “petroleum and petrochemicals,” and “gas and others.”
<Electric Power Industry Market size: 13.6 trillion yen (BESTERRA’s estimate)>
In pursuit of an energy mix that utilizes more desirable methods of generating power, it is anticipated that power plants will be improved to run more efficiently with a smaller environmental footprint. According to the “Survey of Electric Power Statistics” by Japan’s Agency of Natural Resources and Energy, the ratio of power generated by thermal power plants (which have larger environmental footprints) is expected to decrease from 63% to 56% by 2030. This process will likely include the modernization of inefficient equipment. The ratio of nuclear power is also expected to increase from 15% to 21%. Currently, there are 19 nuclear power plants (60 reactors) in Japan, and half of those have been operating for more than 30 years, so reactor decommissioning is expected to increase.
The company has extensive experience in dismantling boilers, smokestacks, and tanks. They also have numerous patented demolition methods (particularly the “Ringo☆Star” apple peeling demolition method for tanks, which boasts superior safety and price competitiveness). In addition, the company uses fireless methods for dismantling power-related equipment, such as transformers, so no harmful gases are released.
<Steel Industry Market size: 1.7 trillion yen (BESTERRA's estimate)>
The steel manufacturing industry requires advanced technology, and is constantly forced to reorganize and make innovations, so a demand for new equipment is expected. While blast furnace manufacturers produce three-fourths of crude steel and the other one fourth is produced by electric furnace manufacturers and metal rolling manufacturers, the company has made transactions with all the blast furnace manufacturers, electric furnace manufacturers, and metal rolling manufacturers. The blast furnaces (coke ovens) built during the high economic growth period in 1960s will come up for repair in the next 10 years, and besides, each blast furnace manufacturer is integrating their respective production bases and enhancing the equipment there with the aim of increasing price competitiveness.The company will meet demand for dismantling work with their patented demolition methods, their ability to carry out work safely and efficiently, and by offering demolition plans using 3D technology to formulate demolition plans.
<Petroleum/Petrochemical Industry Market size: 28.5 trillion yen (BESTERRA's estimate)>
Japan has 22 refineries in 14 regions; however, demand is falling due to the population decrease, popularization of fuel-efficient vehicles, and fuel change. The petroleum and petrochemical industry, therefore, is being forced to take action, such as corporate restructuring and equipment reduction, and the government is encouraging reorganization through the Sophisticated Method of Energy Supply Structures and the Industrial Competitiveness Enhancement Act.In addition, 15 petrochemical complexes across 9 regions in Japan use naphtha-derived (naphth refined petroleum) ethylene as their raw material. In terms of cost competitiveness, this is inferior to overseas petrochemical complexes, which use cheap ethane-derived (ethane: a by-product of natural gas and petroleum) raw materials. It is also difficult for the Japanese complexes to compete with large overseas complexes in terms of scale, therefore they are forced to go through corporate restructuring and downsizing of facilities.
The company will meet demand for dismantling by taking advantage of its extensive experience in the demolition of refineries, ethylene plants, and plant equipment (a downstream business). Specifically, the company will open offices in the bay area, which is the so-called “Pacific belt zone,” with a focus on proposing and marketing its unique demolition techniques.
| Equipment to dismantle | Strategy | Sales (composition ratio) FY ended Jan. 2019, FY ending Jan. 2022 |
Electric power | Boilers, smokestacks, tanks, transformers (PCB) | Get orders for thermal power station projects, PCB-related projects, wind power plant projects, and break new ground in nuclear power-related projects | 1659 million yen (35%) 2400 million yen (33%) |
Steel | Blast furnaces, smokestacks, re-claimers (machinery) | Cement relationship with existing customers (blast furnace operators), and prospect for new customers (electric furnace operators) | 1928 million yen (41%) 2000 million yen (28%) |
Petroleum/ Petrochemistry | Refineries, ethylene plants | Get orders for refinery-related projects and ethylene industrial complex-related projects | 425 million yen (9%) 1900 million yen (26%) |
Gas and others | Gas holders, various manufacturing plants | Enrich sales activities of the apple peeling demolition method, and get orders for projects of various plants | 747 million yen (15%) 900 million yen (13%) |
Enrichment of demolition methods
The company will keep on proposing competitive patent-based dismantlement methods including the cost competitive “Apple peeling demolition method” and the “Ringo☆Star” (dismantling of tanks), unique fireless method (power related equipment such as transformers), and the windmill dismantling method (wind power generation) that is pending for international patent, and it is making efforts to put them into practical use.
<“Apple peeling demolition method” and fusing robot “Ringo☆Star”>
The “apple peeling demolition method” is a method of dismantling a large spherical tank, such as gas holders and oil tanks, by cutting it in spirals from the center of the ceiling of the enclosure part. The cut part spirals down to the ground gradually under the force of the earth’s gravity (natural energy). The method enjoys superiority in a work period, cost, and safety, and has considerable competitive advantages, realizing “greater promptness, higher cost efficiency, and added safety.” Furthermore, the company offers a robot for the fusing process, “Ring☆Star,” which automates the “apple peeling demolition method.”(The company is also working to expand the range of applications for “Ringo☆Star” by developing a new attachment).
<Environment-related methods>
The company has cultivated experiences and business results of a multitude of environment-related demolition works, using the “fireless methods” which do not require the use of fire. For example, although polychlorinated biphenyls (PCBs) are considered as a toxic substance and therefore totally abolished today, it had been used for many years in transformers and condensers because of its excellent thermal stability and chemical stability (electric insulation characteristics). In many cases, transformers and condensers are disposed of in conjunction with plant demolition works; however, because PCBs gasify when they are treated at the high temperature, posing a risk of inhaling the gas so generated, any firearms (such as gas cutting machines) cannot be used in demolition and withdrawal involving PCBs. The company is skillful at fireless and quasi-fireless methods using saber saws (which cut off objects with their saw blades moving in a reciprocating manner) that can cut off objects thicker than the thickness, which, in the industry, had been considered impossible to cut, through numerous devices, including measures against seizure of motors and recycling of blades. BESTERRA has applied for joint patents with Hitachi Plant Construction, Ltd. for a transformer dismantling method, a transformer dismantling jig, and a cutting device for dismantling a transformer.
<Windmill demolition works>
The number of power-generating wind turbines continues to increase by about 20% annually worldwide, but the demand for dismantling is expected to increase in the future due to wear and tear and economic obsolescence.According to the material presented by the company, the wind power generation volume worldwide is 486,790 MW (by about 340,000 onshore power generation plants and about 4,000 offshore ones) with an annual growth rate of about 20%. In Japan, the number of wind power generation plants stood at 2,225 as of the end of 2017, expanding by about 90 every year. Meanwhile, as the useful life is approximately 15 to 20 years, and the windmills for power generation established in the early stage are reaching the application limit. Moreover, not a few plants need to be dismantled due to damage or fatal failure caused by thunderbolts or typhoons.
How to knock down a power-generating wind turbine (international patent application)
As some windmills have been built in mountain districts and on the sea, demolition of them is highly difficult. The company has devised a method for dismantling wind turbines that does not require scaffolds, and has already acquired a domestic patent for “Method of knocking down a power-generating wind turbine.” International patents are pending for “Method of knocking down towering structures using their bases” and “Method for dismantling tower-shaped equipment for wind power generation.” Safety of workers can be improved dramatically and the work period can be shortened by using these patent-based methods.
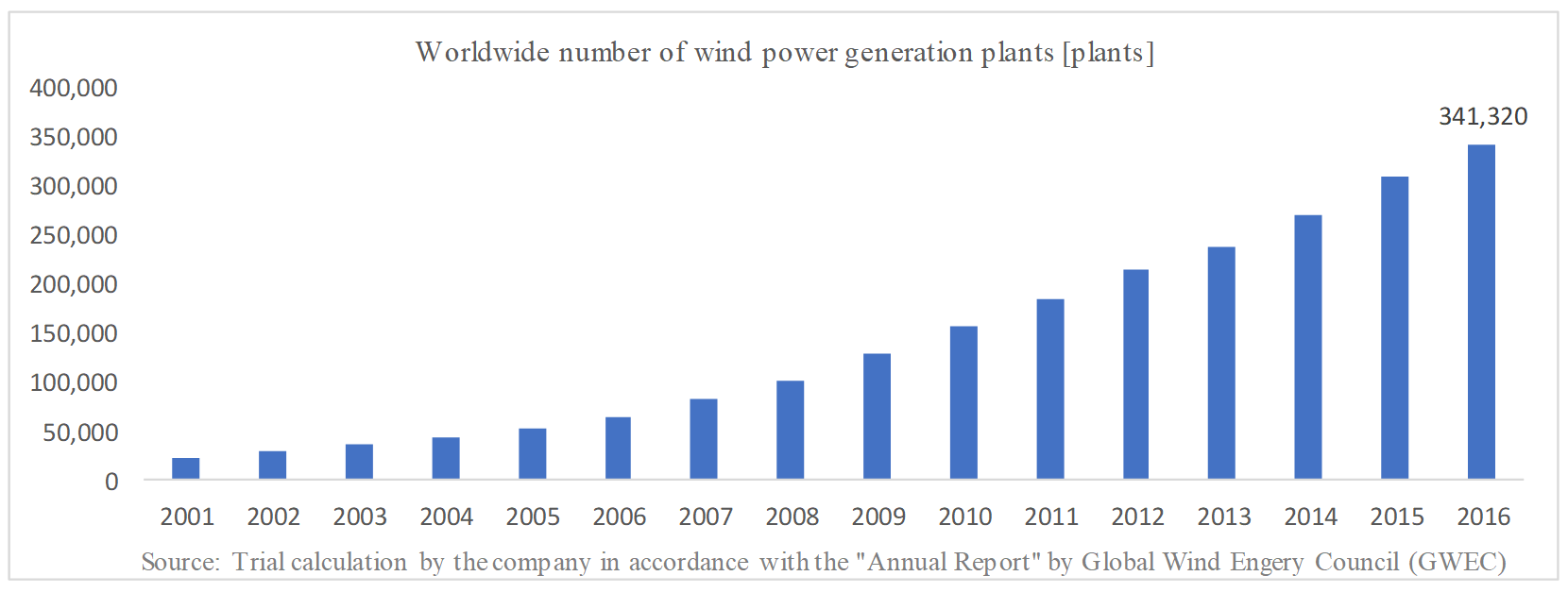
Enhancement of sales capabilities
The company will increase the ratio of demolition works ordered based on prime contracts and enrich sales bases. Currently, the ratio of works as a primary subcontractor entrusted by prime contractors is high. It, therefore, will increase the number of orders received directly from customers and the proportion of prime contract-based works, with the aim of improving earnings ratio. Specifically, the company will enrich advertising media, such as the website, promotional materials, and other various media, as well as present its products and services at exhibitions. BESTERRA is also considering opening new bases.
The company’s current bases and their respective sales as of the end of the term ended January 2019 are: Tokyo Headquarters (3,561 million yen in FY January 2018 → 3,590 million yen in FY January 2019); JFE Chiba factory office (Chiba City, Chiba Prefecture, 550 million yen → 461 million yen); Chiba Office (Ichihara City, Chiba Prefecture, 221 million yen → 271 million yen); West Japan Office (Fukuyama City, Hiroshima Prefecture, 164 million yen → 257 million yen). Currently, the company is planning to expand their West Japan office, and is preparing to open a Keihin office (the company had 180 million yen in sales in the Keihin area in the January 2019 term). They are also considering opening an office in Sendai. The establishment of new bases will lead to an increase of orders for projects with recurring revenue (continuous orders from customer groups, being stationed at factories, etc.).
4-2-2 Reform of the human resources structure
In order to cope with lingering labor shortages, BESTERRA will implement three measures: 1) the increase of personnel through M&A; 2) the creation of a system where employees can work with peace of mind; and 3) the establishment of an employee training program, and then the company aims to increase personnel becoming essential to growth. In the case of 1), personnel increase through M&A, the company will seek business partnerships and M&A with industrial plant-related companies, aiming for mutual lending of staff in order to cope with personnel shortages in construction management. For 2), in order to create a worry-free working environment, the company has made it the standard for all employees to have two days off per week (in this industry, working on Saturday is common, as the work needs to be completed as soon as possible). In addition, in order to promote ease of work, the company has introduced various systems like “shift management by management-level members” and “job rotation,” and initiatives have also been made towards “health management.” By taking steps such as these, they aim to create an environment where employees can work with peace of mind. Finally, for 3), the establishment of an employee training program, BESTERRA plans to create a human resources system that focuses on individual employees’ working styles, introducing an “expert dismantling course” and a “management course” to serve as an evaluation system that matches the actual situations dismantlement supervisors experience. They will also expand the system for employees to acquire specific job qualifications, and promote an employee training program as a means of passing skills and knowledge down to less-experienced workers.
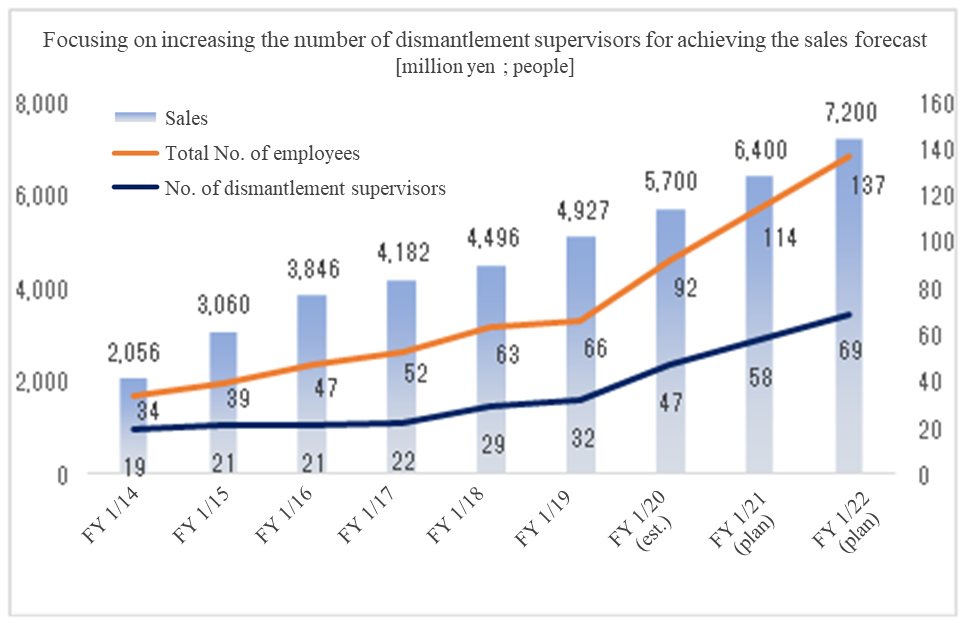
Creating a worry-free work environment
BESTERRA has established a number of frameworks as part of creating an environment where employees can work with peace of mind. This includes things such as retirement benefits, generous subsidies to holding companies, annual paid leave that carries over, and Japan's best income compensation insurance (This of course serves to reduce employee turnover, but also contributes to recruitment activities). In order to support employee asset formation, the company has set up a holding company where employees purchase stock in installments, and are refunded 15% of the paid amount (through bonuses). The annual paid leave system allows employees to save up to 80 days off in preparation for medical treatment or illness (in general, the maximum number of days for paid leave under the Labor Standards Law is 40 days). The income compensation insurance is a fully company-paid insurance that compensates for the decrease in income when employees are unable to work for long periods due to illness. At BESTERRA, 50% of monthly pay is compensated for until retirement age (60 years old).
4-2-3 Pursuit of the value of the 3D business
Using services such as layout simulation, strain/bending/torsion measurement, comparison of structures before and after improvement, and video walkthroughs, the company converts physical data taken when plants were established (more than 30 years ago) into the latest 3D data, and uses that to provide detailed information about the dismantling process. They also provide unique 3D measurement services for dismantling work using the latest measuring technology and simulation systems that are capable of drawing data as 2D diagrams, handling BIM/CIM modeling, Perfect 3D, and 3D printing.
“Visualize” the dismantling process
Layout simulation
Equipment models created with 3D CAD are arranged into 3D data, enabling interchangeable simulations. Dynamic interference and collision checks can be performed while moving the models.
Strain, bending, and torsion measurements
Measuring change in shape is possible. This is useful for making a tentative assessment of a building’s frame, such as whether the building’s shape has been altered due to earthquake or aging.
Comparison of structures before and after installation
A comparison is made between the condition of piping, conveyors, furnaces, etc. at the time of installation and after they have been in operation. The 3D data can intuitively pick up changes due to heat and vibration.
Video walkthroughs
A video walkthrough is created using synthesized point cloud data. It can be used to present construction plans and building information, as well as for public relations.
Unique 3D measurement service
Draws a two-dimensional diagram
3D CAD models based on point cloud data can be drawn as two-dimensional diagrams. Diagrams can also easily be drawn directly from point cloud data.
Handles BIM/CIM modeling
Objects are modeled in 3D CAD based on point cloud data. It is also possible to create parts necessary for construction and repair as BIM data (Building information modeling).
Perfect 3D
A large-scale three-dimensional data measurement service that combines MMS (Mobile Mapping System, done by car), laser measurements taken from the air, and measurements of water areas.
3D printing
After using the point cloud data to create a model, the data is processed and arranged so it can be modeled by a 3D printer. The 3D printer is capable of an extremely fine lamination pitch of 15 μm.
4-2-4 M&A strategy
BESTERRA actively promotes partnerships and M&As, seeking to generate a synergistic effect. In particular, the company plans to utilize business partnerships to create a “decommissioning-related business platform” for the purpose of decommissioning nuclear reactors. (The company will become the platformer, and partner companies will be able to work together and make use of each other’s strengths to create a system for decommissioning-related business.)
In July 2018, with the goal of boosting its competitiveness in work related to the decommissioning of nuclear reactors, the company entered a business partnership with Hitachi Plant Construction, Ltd., which utilizes their technology and know-how in sales, site management, and nuclear power plant-related work (decommissioning, repair, etc.) to handle dismantling using equipment such as large band saws, as well as radiation control. In September 2018, the company also partnered with DAI-ICHI CUTTER KOGYO, which has superb work quality and provides cutting technology utilizing diamonds and water jets.
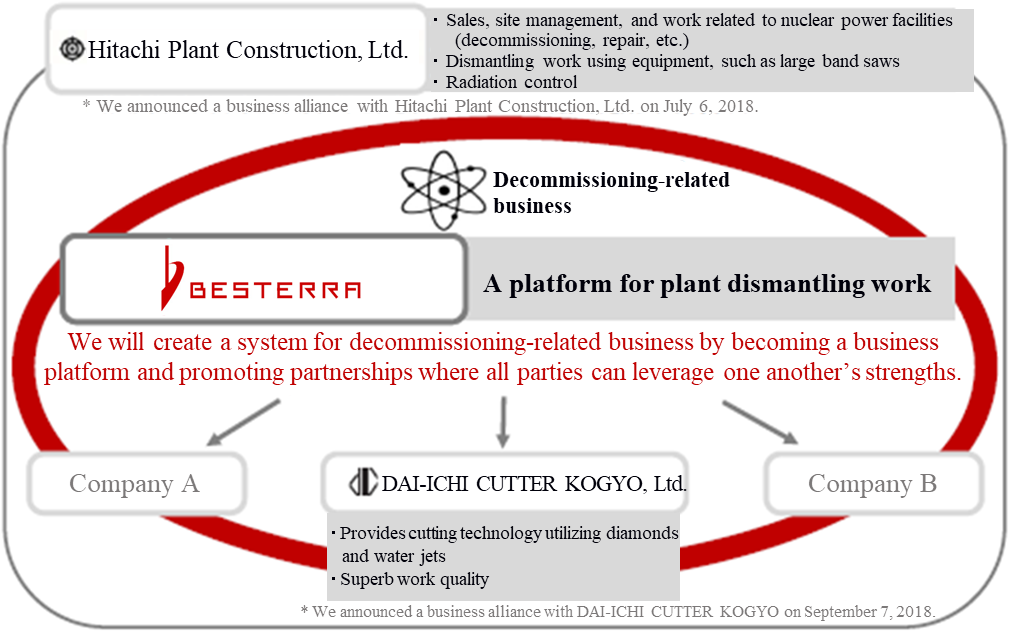
(Taken from company’s material)
4-3 Profit-sharing policy/shareholder return
As described above, while taking account of “investment in future growth(Human resources, technology development, systems, M&A, etc.)” and “retained earnings for strengthening the business bases,” the company plans to distribute dividends at a payout ratio of about 40%.
In addition to dividends, the company provides shareholder benefits in the form of QUO prepaid cards worth 1,000 yen to shareholders holding 1 unit (100 shares) or more and 2,000 yen to shareholders holding 3 units (300 shares) or more.
5.Conclusions
For the foreseeable future, business performance will depend on the development of human resources, but the business environment is sound. The demand for dismantlement and upgrade is expected to rise as a result of deterioration of equipment established after the period of rapid economic growth in 1960s, economic obsolescence, reorganization of companies, overseas transfer, etc. Also, 24 nuclear reactors out of 60 nuclear reactors in 19 different locations in Japan are to be decommissioned, and the number will grow further with the progress of conformity assessment of the new regulatory standards. Dismantlement of nuclear power generators is challenging as it must be carried out efficiently while preventing radiation exposure, but its potential demand is high. As for decommissioning, the surrounding equipment of nuclear reactors must be dismantled first, which is the same process as it is for the thermal power generators, in which the company has excellent achievements and accumulated know-how. The patent for a special method of dismantlement will demonstrate its strong points when dismantling tanks, boilers, smokestacks, cranes, etc. It will be a task as well as the focus point for the company to materialize the effects of collaborating with Hitachi Plant Construction and DAI-ICHI CUTTER KOGYO with the business related to dismantlement of nuclear reactors in mind.
<Reference: Regarding Corporate Governance>
◎ Organization type and the composition of directors and auditors
Organization type | Company with an audit and supervisory board |
Directors | 7 directors, including 2 outside ones |
Auditors | 3 auditors, including 3 outside ones |
◎ Corporate Governance Report Update date: October 16, 2018
Basic policy
In order to promote sound business administration and win social trust sufficiently, our company recognizes corporate governance as the most important issue, puts importance on the improvement of the soundness, transparency, and fairness of business administration, and complies with laws and regulations thoroughly, and all executives operate business while keeping in mind that “the violation of laws or regulations would lead to management responsibility.” In detail, our company disseminates and executes business pursuant to laws, regulations, and in-company rules thoroughly, by developing appropriate systems for making decisions about business administration, fulfilling duties, supervising work, conducting internal control, etc.
It is also important to reform management systems for “achieving appropriate share price” and “increasing share price sustainably” to emphasize shareholders and strengthen the function to check business administration, to establish global-level corporate governance. The results of such efforts would win the trust of society, increase corporate value, and satisfy shareholders.
<Reasons for Non-compliance with the Principles of the Corporate Governance Code (Excerpts)>
【Supplementary principle 4-1-3】
There is no concrete plan regarding the succession of the CEO (chief executive officer). As a policy for the selection of a successor in the Board of Directors meeting, we will select a suitable candidate by taking his/her character, insight and achievements into account. The Board of Directors will actively take part in activities of making and carrying out a succession plan.
【Supplementary principle 4-3-3】
Our company has not established a clear procedure ensuring objectivity, timeliness and transparency for dismissal of the president or CEO, but we strive to realize a mutual assessment by involving outside directors in the process of evaluation of nomination and remuneration of the Board of Directors, in order to carry out the assessment of effectiveness of the Board of Directors appropriately.
【Supplementary principle 4-10-1】
Our company appoints two independent outside directors who state their opinions to the Board of Directors or each director and give advices as necessary, based on their expertise and extensive experiences as corporate managers. Our company does not have any arbitrary advisory committee, but we consider that we have been receiving appropriate advices and participation from the independent outside directors in meetings of the Board of Directors at present.
【Supplementary principle 4-11】
The Board of Directors of our company is composed of directors having expertise in each department and outside directors who are also corporate managers. We believe the size of the Board is appropriate, but we will make efforts in selecting candidates while placing emphasis on diversity, as our company lacks diversity in terms of gender and internationality. In addition, we strive to improve the function and effectiveness of the Board of Directors through regular discussions on direction and operation of the Board of Directors in the board meetings with outside directors. The board of auditors of our company is composed of three independent officers including ones with experience of corporate management and licensed tax accountant, and they have experience and expertise in management, financial affairs, accountancy, sales, auditing, etc.
【Supplementary principle 4-11-3】
In our company, the Board of Directors meeting is held monthly, and important matters adopted in the Rules of the Board of Directors are deliberated and decided timely and appropriately. Also, the directors receive reports about business conditions on a regular basis and conduct audits for appropriate risk management and business execution. For a highly important matter, outside directors and auditors are explained the details beforehand and an adequate time is taken out for deliberation and active discussion at the Board of Directors meeting. As mentioned above, we believe the operations of the Board of Directors of our company are effective, but we will make efforts in improving the effectiveness further.
<Disclosure Based on the Principles of the Corporate Governance Code (Excerpts)>
【Principle 5-1 Policy on constructive dialogue with shareholders】
Regarding requests from shareholders for dialogue (interviews), our company believes that we should express a positive attitude within a reasonable scope in order to contribute to sustainable growth and medium- and long-term improvement of the corporate value of our company. Aiming to promote constructive dialogue with shareholders, with the planning department designated as a department in charge of IR activities, our company holds financial results briefings targeted at financial institutions and investors semiannually and discloses corporate information as needed on our website and through the system of optional disclosure offered by Tokyo Stock Exchange.
This report is intended solely for information purposes, and is not intended as a solicitation for investment. The information and opinions contained within this report are made by our company based on data made publicly available, and the information within this report comes from sources that we judge to be reliable. However, we cannot wholly guarantee the accuracy or completeness of the data. This report is not a guarantee of the accuracy, completeness or validity of said information and opinions, nor do we bear any responsibility for the same. All rights pertaining to this report belong to Investment Bridge Co., Ltd., which may change the contents thereof at any time without prior notice. All investment decisions are the responsibility of the individual and should be made only after proper consideration.
Copyright(C) 2019 Investment Bridge Co.,Ltd. All Rights Reserved.