Bridge Report:(4634)Toyo Ink SC the first half of the Fiscal Year ending December2023
![]() Satoru Takashima President | Toyo Ink SC Holdings, Co., Ltd. (4634) |
![]() |
Company Information
Market | TSE Prime Market |
Industry | Chemical (Manufacturing) |
President | Satoru Takashima |
HQ Address | 2-2-1 Kyobashi, Chuo-ku, Tokyo Kyobashi Edogrand |
Year-end | End of December |
Homepage |
Stock Information
Share Price | Shares Outstanding | Total Market Cap | ROE Act. | Trading Unit | |
¥2,385 | 58,286,544shares | ¥139,013 million | 4.3% | 100shares | |
DPS Est. | Dividend Yield Est. | EPS Est. | PER Est. | BPS Act. | PBR Act. |
¥90.00 | 3.8% | ¥113.19 | 21.1x | ¥4,133.90 | 0.6x |
* Share price as of closing on September 14. Shares Outstanding is based on the financial results for the first half of the fiscal year ended December 2023. ROE and BPS are actual results for the fiscal year ended December 2022, DPS and EPS are forecast for the fiscal year ending December 2023.
Earnings Trend
Fiscal Year | Sales | Operating Income | Ordinary Income | Net Income | EPS | DPS |
December 2019 (Act.) | 279,892 | 13,174 | 13,847 | 8,509 | 145.72 | 90.00 |
December 2020 (Act.) | 257,675 | 12,909 | 12,543 | 6,019 | 103.06 | 90.00 |
December 2021 (Act.) | 287,989 | 13,005 | 15,442 | 9,492 | 169.36 | 90.00 |
December 2022 (Act.) | 315,927 | 6,865 | 7,906 | 9,308 | 171.49 | 90.00 |
December 2023(Est.) | 330,000 | 11,000 | 9,500 | 6,000 | 113.19 | 90.00 |
*Unit: million yen, yen. Estimates are those of the Company. Net income is net income attributable to the shareholders of the parent company. Hereinafter the same shall apply.
This Bridge Report provides Toyo Ink SC Holdings, Co., Ltd.’s earnings results for the first half of the Fiscal Year ending December 2023, and more.
Table of Contents
Key Points
1. Company Overview
2. First Half of the Fiscal Year ending December 2023 Earnings Results
3. Fiscal Year ending December 2023 Earnings Forecasts
4. Progress of the medium-term management plan "SIC-II" (2021-2023)
5. Future Focuses
<Reference 1: Mid-Term Management Plan SIC-II (2021-2023)>
<Reference 2: Regarding Corporate Governance>
Key Points
- In the first half of FY December 2023, sales were 153.6 billion yen, down 0.7% year on year. Despite the effects of exchange rates and price revisions, sales decreased due to sluggish electronics market conditions and a downturn in the Chinese economy. In the polymers/coating segment, the sales of products for panels and smartphones were stagnant as inventory adjustments from the previous year continued. Operating income increased 3.0% to 4.7 billion yen. The effects of price revisions (+4.2 billion yen) and cost reductions (+700 million yen) contributed, absorbing the decrease in sales volume (-3.1 billion yen) due to market downturns and the rise in raw material prices (-1.6 billion yen), resulting in an increase in profit. Further price revisions are being made to absorb the impact of rising raw material costs. Through the price revisions, quarterly operating income has been on a clear recovery trend since it bottomed out in Q3 of FY December 2022, in which their business was heavily affected by rising raw material costs. Net income decreased 54.3% to 3.8 billion yen. This was a reactionary decline from the sale of shares in Sakata Inx Corporation due to the termination of the capital alliance with the company in the same period of the previous year, resulting in a gain on sale of investment securities of 5.4 billion yen.
- There are no revisions to the full-year forecast, with sales expected to increase 4.5% year on year to 330 billion yen and operating income expected to increase 60.2% year on year to 11 billion yen. From the second half of the fiscal year, sales volume is recovering, mainly in overseas markets, and both sales and profit are projected to grow steadily. In terms of products, the performance of high value-added products is expected to recover as inventory adjustments are completed in the second half of the fiscal year. Regarding environmentally friendly products, sales expansion is underway in India. In the field of polymer materials related to environmental themes, there are many inquiries about laminating adhesives for LiB exteriors in China, following Japan and South Korea. The expansion of production capacity on a global basis, which has been promoted so far, is expected to contribute to the performance in the second half of the fiscal year.
- The ongoing Medium-term Management Plan "SIC-II" is in its final year, and sales are expected to exceed the initial forecast of the Medium-term Management Plan for all segments. The sales target and investment amount for LiB dispersions in FY December 2026 were revised upwardly. In addition, the corporate name will be changed to Artience Corporation in January 2024, and the next Medium-term Management Plan will be announced in February 2024.
- The recovery of profits after reaching bottom in Q3 of FY December 2022 is now evident, as raw material and energy prices stabilized while they were reflected in prices. The recent upward revision of the sales target for LiB dispersion materials can be taken as a sign of confidence in the company's ability to expand future sales. Considering the recent recovery of performance and the growth driven by LiB dispersions, we believe that the stock price that significantly falls below a PBR of 1 is undervalued. In the Medium-term Management Plan to be announced next February, measures are expected to be taken to improve PBR.
1.Company Overview
Toyo Ink SC Holdings is Japan’s top manufacturer of printing inks. Using the processing technologies of pigments and polymers that are the raw materials of inks, the Company manufactures various products such as LCD color filter materials (CF) and electromagnetic shielding films. The Toyo Ink Group is comprised of Toyo Ink SC Holdings, 57 consolidated subsidiaries in and outside Japan, and 6 equity method affiliate companies (The end of June 2023). They are operating business in 24 countries around the world.
Under the long-term scheme “Scientific Innovation Chain 2027 (SIC 27),” whose concept is to contribute to the improvement of sustainability of ordinary citizens, life, and the global environment by innovatively thinking, scientifically executing, and connecting each activity by each employee, it is aiming for a transformation to have a corporate structure that enables sustainable growth towards 2027.
1-1 Corporate History
The origin of Toyo Ink dates back to 1896, when founder Kamataro Kobayashi opened Kobayashi’s Ink Shop as sole proprietorship in Nihonbashi, Tokyo. In 1907, it was reorganized and renamed as Toyo Ink Manufacturing Co., Ltd. During the Meiji period, many newspapers and magazines, including the Yomiuri Shimbun (founded in 1874) and the Asahi Shimbun (founded in 1879), were launched. The government also printed an increasing number of materials including textbooks to enhance educational levels under the policy of increasing wealth and military power. Under these circumstances, the demand for printing inks expanded rapidly.
Initially, inks in the Japanese market were mostly imported products; however, as the national policy favored high quality domestically produced inks, the Company, with its advanced technological skills, successfully expanded its business with clients such as the Printing Bureau of the Ministry of Finance and other government bodies, in addition to private printing companies. Exports also grew during the same time. The Company’s rapid growth was also due in part to the early introduction of integrated manufacturing system from raw materials (pigments, polymers) to finished products (printing inks). Another contributing factor may be that the Company, since its inception, had strong ties with Toppan Printing Co., Ltd., which, by then, was among Japan's largest printing companies. The Company survived the difficult times of the Great Kanto Earthquake and the World War II and experienced rapid growth again during the period of high economic growth after the war. The Company was listed on the Second Section of the Tokyo Stock Exchange in 1961 and moved to the First Section of the Tokyo Stock Exchange in 1967.
The Company is expanding its businesses from manufacturing of printing inks to other fields such as LCD color filters (CF) , using its wide range of technologies and know-how cultivated through manufacturing and processing of raw materials such as pigments and polymers. In 2011, the Company adopted a holding company system for further expansion and growth of the Group, and changed its name to Toyo Ink SC Holdings, Co., Ltd.
In April 2022, the company got listed on the Prime Market of TSE after the market restructuring.
1-2 Management Philosophy etc.
“The Toyo Ink Group’s Corporate Philosophy System” was established in April 1993. It consists of three parts, namely, corporate philosophy, corporate policies, and guiding principles. The Philosophy embodies the original roots of the brand of the corporate group and serves as guidelines that each employee of the Group should always keep in mind and act on as a business professional. In April 2014, “improving shareholder satisfaction” was added to its guiding principles. With this revision, the Company is aiming to improve satisfaction of all stakeholders.
<Toyo Ink Management Philosophy>
Management philosophy | People-oriented management |
|
|
Corporate policies | We, the Toyo Ink Group, endeavor to be a company that contributes to the enrichment of life and culture throughout the world. *Contribute to the affluence and culture of people worldwide. *Create lifestyle value for the new age. *Provide advanced technology and quality products and services. |
|
|
Guiding principles | *Provide knowledge that enhances customer trust and satisfaction. *Respect the materialization of all employees' dreams. *Act as a responsible citizen in harmony with society and the environment *Respect shareholders' rights, improve shareholder value and enhance market valuation. |
1-3 Market Environment
◎ Overview
(Market trend)
The production value of the Japanese printing industry is declining especially in the realm of publication printing of newspapers and magazines because of the increase in digitization and aliteracy. Specifically, it fell sharply in 2020 due to the impact of the novel coronavirus etc. Also, in the realm of commercial printing, demands for posters, catalogues, fliers, POP, etc. were sluggish. On the other hands, printing on food and pharmaceutical packages and plastic containers is steadily increasing at the compound annual growth rate (CAGR) of 2.6% for 17 years from 2004 to 2022.
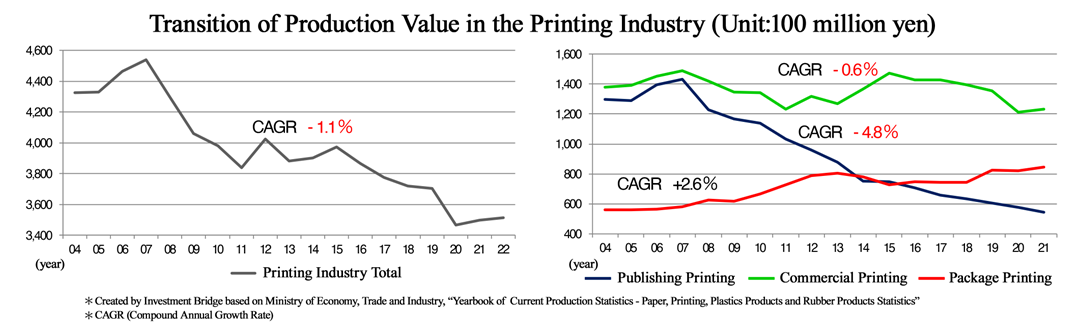
Meanwhile, overseas, especially in newly emerging countries, both printing on papers (offset printing) and printing on film of food packages (gravure printing, flexographic printing) are expected to grow, and the Company is focusing on responding to the demand.
As innovation of printing machine is progressing, quality of printing is enhancing. Overseas local inks, in many cases, cannot respond to such demand for high quality, which may lead to more demand of excellent Japanese ink.
Also, with the growing global awareness of the environment, the needs for environmentally friendly products such as biomass inks are expanding, and ink companies are working on the development of new products that utilize their unique technologies.
◎ Other companies in the industry
There are six major listed companies including Toyo Ink in the ink industry in Japan.
While (4631) DIC is the number one company in the world, (4634) Toyo Ink SC Holdings, Co., Ltd. is the top runner in Japanese printing ink industry, and ranks first or second in most product categories. Globally, the Company is ranked fifth.
|
| Sales | Sales growth rate | Operating income | Profit growth rate | Operating margin | Total market value | PER | PBR | ROE |
4116 | Dainichiseika Color & Chemicals Mfg. Co., Ltd. | 128,000 | +4.9% | 5,200 | +97.3% | 4.1% | 44,057 | 9.4 | 0.4 | 44,057 |
4631 | DIC | 1,060,000 | +0.6% | 25,000 | -37.0% | 2.4% | 238,415 | 59.2 | 0.6 | 238,415 |
4633 | SAKATA INX | 226,000 | +4.9% | 10,000 | +142.4% | 4.4% | 73,457 | 8.5 | 0.7 | 73,457 |
4634 | Toyo Ink SCHD | 330,000 | +4.5% | 11,000 | +60.2% | 3.3% | 139,013 | 21.0 | 0.5 | 139,013 |
4635 | Tokyo Printing Ink Mfg. Co., Ltd. | 47,400 | +9.2% | 1,000 | - | 2.1% | 7,681 | 8.4 | 0.3 | 7,681 |
4636 | T&K TOKA | 49,180 | +12.6% | 1,400 | +229.7% | 2.8% | 33,137 | 24.0 | 0.7 | 33,137 |
*Sales and operating income are based on forecasts of each company for this FY. ROE are based on actual results of the previous term end.
*Unit: million yen, times. Total market value and PER,PBR is as of closing on September 14, 2023.
1-4 Business Description
◎ Concerning “printing inks”
Followings are the summary of printing inks, one of the major product categories of the Company, categorized by “raw materials” and “types and purposes of use.”
<Composing elements of printing inks>
Pigments (organic pigments, inorganic pigments, etc.) | Pigments are powders that are used to provide color and are insolvent to water and oil. |
Varnish (synthetic polymers, lipids, fluxing materials, etc.) | Varnish is a combination of lipids, natural polymers, synthetic polymers, etc. in a solvent. It diffuses pigments, transfers and fixes them to printing materials. |
Additives (lubricant, hardening agent, etc.) | Additives used to adjust so-called printability such as drying performance and fluidity, as well as printing effect. |
High-level dispersion technologies are required when various inks are produced by combining the above three raw materials.
Since its foundation, the Company has also been expanding its business categories by exploring application of these raw materials in the process of manufacturing them.
<Types and intended use of major printing inks>
Types | Characteristics and Intended Use |
Planographic inks | Typical printing ink on paper. They are used for printing magazines, posters, fliers, etc. |
Gravure inks | Because of their capacity to express detailed gradation, it is suitable for printing photo images. Currently, they are mainly used for printing films such as food wrapping materials. |
Screen inks | They are mainly used for printing on materials that are difficult to be printed with other methods, including electronics fields such as meters and gauges of cars, circuit board formation, and CDs/DVDs. |
Flexographic inks | They are used to print on the surface of cardboard boxes, films and clothes. |
UV curing inks | Because they dry instantly without using a heat drier in the drying process, they are used for UV curing printing that does not directly generate CO2. They are environmentally friendly inks that do not generate Volatile Organic Compounds (VOC). |
◎ Business segments
The business activities of the Company are classified into four segments: the “Colorants & Functional Materials Related Business,” “Polymers & Coatings Related Business,” “Printing & Information Related Business”, and “Packaging Materials Related Business”.
The “Printing & Information Related Business” mainly deals with planographic inks that are used for printing on papers (offset inks, etc.). The “Packaging Materials Related Business” deals with gravure inks and flexographic inks that are used for printing on films of food packages. The “Colorants & Functional Materials Related Business” deals with products related to pigments that are also the raw materials of printing inks as core materials. The “Polymers & Coatings Related Business” began with polymers that are the main raw materials of inks and their design technologies.
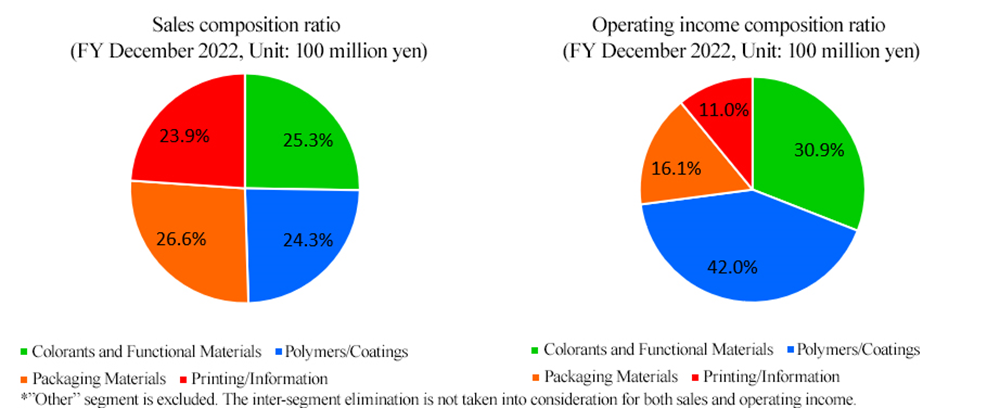
☆Colorants and Functional Materials Related Business
| FY Dec.22 |
Sales | 79,380 |
Operating Income | 1,846 |
Operating Margin | 2.3% |
*Unit: million yen
Main segment | Main products | Main uses |
Materials for CF (Materials for Display) | Display materials (Resist ink), paste, and high- performance pigments | Displays and sensors |
Plastic Colorants | Masterbatches and compounds | Containers, automobiles, home appliances/OA, and building materials |
Pigments | Pigments and pigment dispersions | Printing inks and automobile paints |
Inkjet | Inkjet inks | Signage advertisements, labels, and cardboard |
Functional Dispersions | Lithium-ion battery materials and functional dispersions | Lithium-ion batteries for xEVs* |
(*) xEV: A general term for electric vehicles that includes EV, hybrid vehicles, and plug-in hybrids

(Taken from the Company’s material)
Based on the organic pigments that are the main raw materials for printing inks, and by integrating their color material technologies, organic chemical synthetic technologies and high-level dispersion technologies, the Company offers materials that are used in various fields. Especially, it created higher functional LCD color filter materials using their nano-level dispersion technologies through integration of technologies that have been accumulated from their ink and painting materials production experiences.
Furthermore, the Company’s dispersion processing technologies are used not only for organic pigments but also for inorganic materials such as carbon nanotube (CNT), which leads to expansion of its business in the new energy field such as secondary battery materials.
◎ Rapid Growth of the LiB CNT Dispersion Business
The dispersion technology accumulated for many years has been applied to materials for LiB (Lithium-ion batteries). They have a long track record in automotive LiBs and have been adopted for hybrid vehicles (HEV) LiBs since 2015. The battery brand "LIOACCUM®" was created. In 2019, LIOACCUM®, a next-generation conductive material CNT (carbon nanotubes) dispersed using proprietary technology, was adopted for use in electric vehicles (EVs). With the expansion of the EV market, rapid growth is expected in the future.
LiB Production Process and CNT Dispersion "LIOACCUM®"
■LIOACCUM® excels in CNT dispersion and distribution within an electrode, forming a uniform and efficient conductive network on an active material surface.
■It contributes to the high capacity, high output, and long lifespan of LiB.
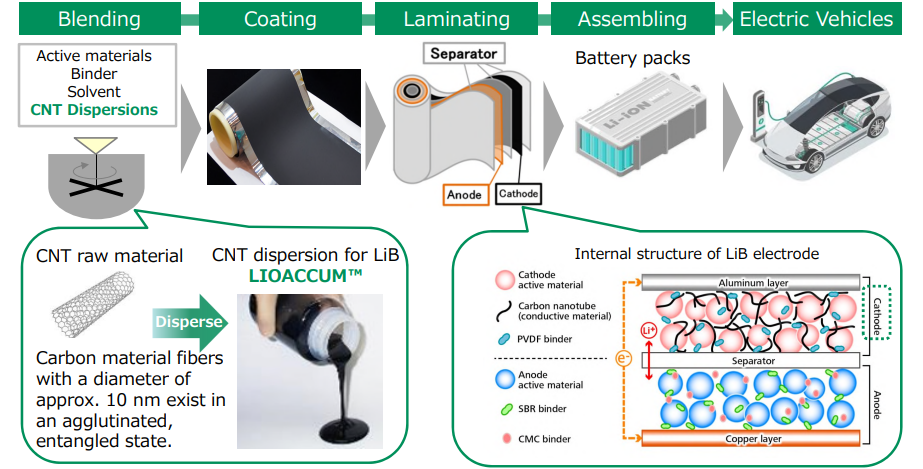
(Taken from the Company’s material)
☆Polymers & Coatings Related Business
| FY Dec.22 |
Sales | 76,240 |
Operating Income | 2,504 |
Operating Margin | 3.3% |
*Unit: million yen
Main segment | Main products | Main uses |
Packaging & Industrial Materials | Adhesives, laminating adhesives, hot melts, can coatings and polymers | Labels, film packaging, solar cells, plastic bottle labels, beverage cans, and building materials |
Electronics | Functional films, adhesives, double-sided tape, and hard coats | Smartphones, displays, and tablets |
Medical & Healthcare | Medical products, adhesives, and natural extracts | Transdermal drugs, sports tapes, foods, and feeds |
![]() |
![]() |
![]() (Taken from the Company’s material) |
For this segment, the Company develops functional polymers as the core materials with different functional features. Using unique technologies that have been developed for many years, the Company creates new functions to cultivate new demand and open new markets in electronics, energy, health care and other fields.
☆Packaging Materials Related Business
| FY Dec.22 |
Sales | 83,464 |
Operating Income | 963 |
Operating Margin | 1.2% |
*Unit: million yen
Main segment | Main products | Main uses |
Liquid inks | Gravure inks | Film packaging (food packaging and refills of daily necessities) and building materials |
flexographic inks | Sanitary products, cardboard, and paper bags |
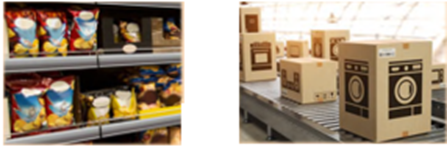
(Taken from the Company’s material)
For this segment, the Company deals with printing inks and equipment used in packages such as gravure printing and flexographic graphic printing.
In the field of food packaging materials, etc., the Company is dedicated to developing environmentally friendly products using water-based ink to assure their safety to the consumers.
☆Printing & Information Related Business
| FY Dec.22 |
Sales | 75,180 |
Operating Income | 654 |
Operating Margin | 0.9% |
*Unit: million yen
Main segment | Main products | Main uses |
Offset inks (General inks) | Offset inks, newspaper inks | Books, newspapers, and flyers |
Functional inks | UV curable inks | Paper containers, labels, and books |
metal decorating inks | Drink cans and food cans | |
Screen inks | Electronics and stickers | |
![]() |
![]() |
![]() |
This segment is the base segment of the Company since its establishment. For this segment, the Company deals mainly with printing inks used for printing on paper.
The Company offers not only printing inks but also sales of machinery/equipment, support for streamlining customers’ printing process, and support and tools for color management and color universal design.
◎ Overseas expansion
While the Company is improving profitability by offering high-value-added products in the Japanese market, where a rapid growth is not expected, it is aggressively expanding its business from both production and sales perspectives in the overseas market where future growth is expected.
Development of its overseas manufacturing structures was almost completed during the previous Midterm Business Plan, and the Company is carrying out both raw material procurement and production at local sites.
As of the end of December 2022, the Company has about 44 overseas consolidated subsidiaries in a wide range of countries around the world.
(Sales in each region, FY 12/2022)
| Sales | YoY | Operating Income | YoY |
Japan | 1,770 | +2.0% | 29 | -60.3% |
Asia | 1,269 | +11.7% | 37 | -22.9% |
Europe | 269 | +27.5% | 5 | -61.5% |
The Americas | 227 | +40.1% | -1 | - |
Adjustment | -376 | - | -1 | - |
Consolidated total | 3,159 | +9.7% | 69 | -46.9% |
*Unit: 100 million yen
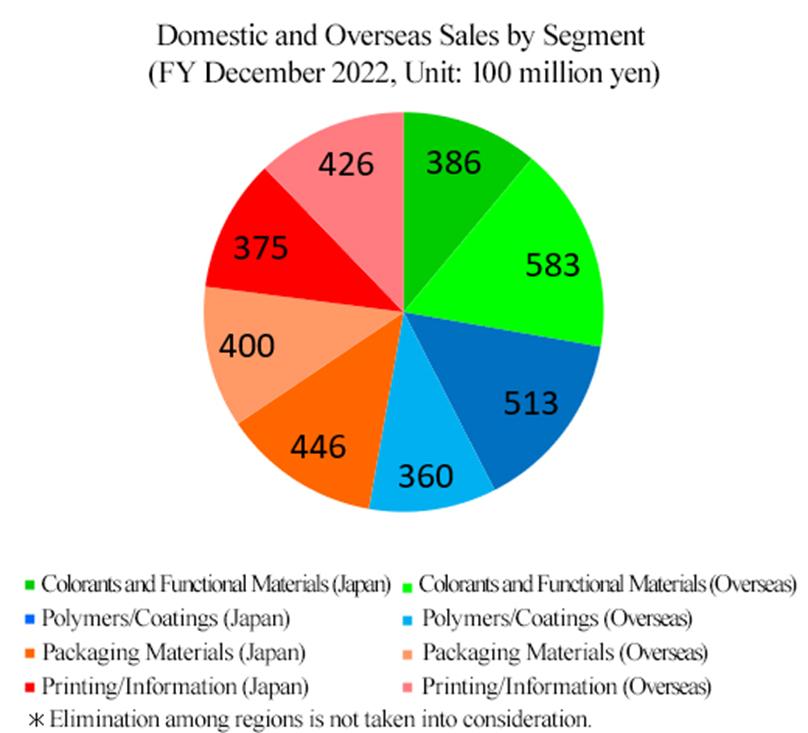
1-5 ROE Analysis
| FY 12/ 17 | FY 12/ 18 | FY 12/ 19 | FY 12/ 20 | FY 12/21 | FY12/22 |
ROE (%) | 4.8 | 5.4 | 3.9 | 2.8 | 4.4 | 4.3 |
Net income margin (%) | 4.32 | 4.08 | 3.04 | 2.34 | 3.30 | 2.95 |
Total asset turnover [times] | 0.65 | 0.77 | 0.75 | 0.68 | 0.73 | 0.77 |
Leverage [times](x) | 1.72 | 1.72 | 1.72 | 1.76 | 1.84 | 1.87 |
Further improvement of profitability and efficiency is continuously desired to achieve an ROE of 8%, which is the generally recommended goal for Japanese enterprises, as a step toward achieving a P/B Ratio of over 1.0.
1-6 Characteristics and Strengths
(1) Strong technological edge
As described above, the Company has been manufacturing in-house its core materials, pigments and polymers, which are the raw materials of printing inks. Its technological capacities form the basis of high-quality printing ink production and lead to expansion of business areas and product range such as, LCD color filter materials, adhesive bonds and adhesive compounds.
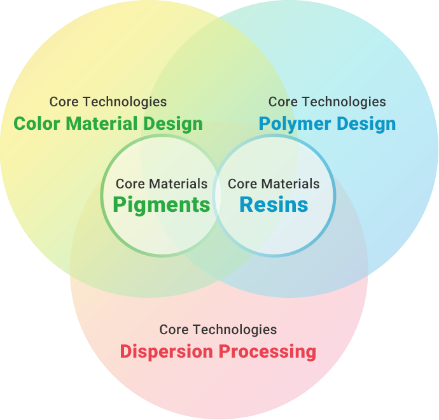
(From the Company’s HP)
(2) Excellent problem-solving skills
One of the reasons for the Company to be at the top of the Japanese printing inks industry is its excellent problem-solving capability in all aspects of printing.
The Company not only produces and supplies printing inks but also studies elements related to “printing” as a whole including plate making and images. Such efforts enable the Company to make technological proposals, demonstrate advanced service skills, and obtain high customer satisfaction.
(3) Environmental concerns
The Company is a forerunner in CO2 emission reduction as well as production of eco-friendly inks such as non-VOC inks, water-based inks, and UV inks. In the newly developed countries, too, the environmental regulations are becoming tighter, and the needs for environmentally friendly products are increasing. The Company is also working on assuring safety such as chemical substances control and manufacturing a line of products that meet the Swiss Ordinance, ahead of other companies.
(4) Uniqueness of management strategies
The Company considers M&A as one of the options for exploring new markets with its technological edge, if M&A is expected to bring synergy effects to the Company. However, it is not intending to implement M&A just to increase the size of businesses. It is also taking an initiative in the printing ink industry to establish “local production for local consumption” policy in the overseas market for enhancing efficiency (e.g., reduction in transport mileage) and social contribution (e.g., utilization of local products) purposes.
2. First Half of the Fiscal Year ended December 2023 Earnings Results
(1) Business Results
| FY 22/12 1H | Ratio to sales | FY 23/12 1H | Ratio to sales | YoY |
Sales | 154,758 | 100.0% | 153,676 | 100.0% | -0.7% |
Gross profit | 27,870 | 18.0% | 28,910 | 18.8% | +3.7% |
SG&A | 23,254 | 15.0% | 24,157 | 15.7% | +3.9% |
Operating Income | 4,615 | 3.0% | 4,752 | 3.1% | +3.0% |
Ordinary Income | 6,728 | 4.3% | 5,365 | 3.5% | -20.2% |
Net Income | 8,410 | 5.4% | 3,842 | 2.5% | -54.3% |
*Unit: million yen. Accounting Standard for Revenue Recognition has been applied from the first quarter of the term ended December 2022.
Sales slightly decreased, while operating income increased.
Sales declined 0.7% year on year to 153.6 billion yen. Despite the effects of exchange rates and price revisions, sales decreased due to sluggish electronics market conditions and a downturn in the Chinese economy. The performance of the polymers/coating segment, products for panels and smartphones was stagnant, as inventory adjustments from the previous year continued.
Operating income increased 3.0% to 4.7 billion yen. The effects of price revisions (+4.2 billion yen) and cost reductions (+700 million yen) contributed, absorbing the decrease in sales volume (-3.1 billion yen) due to market downturns and the rise in raw material prices (-1.6 billion yen), resulting in an increase in profit.
Over the two years of 2021 and 2022, the price revision effect was +25.2 billion yen, but the rise in raw material costs was -33.3 billion yen, and the increased costs could not be fully absorbed. In 2023, further price revisions are being made to absorb the impact of rising raw material costs.
The quarterly performance trend is as shown in the table below. Regarding operating income, there is a clear recovery trend after hitting the bottom in Q3 of FY 2022, in which their business was heavily affected by rising raw material costs.
Net income decreased 54.3% to 3.8 billion yen. This was due to a decrease in foreign exchange gains from 2.1 billion yen in the same period of the previous year to 900 million yen, and the reactionary decline from the sale of shares in Sakata Inx Corporation due to the termination of the capital alliance with the company in the same period of the previous year, resulting in a gain on sale of investment securities of 5.4 billion yen.
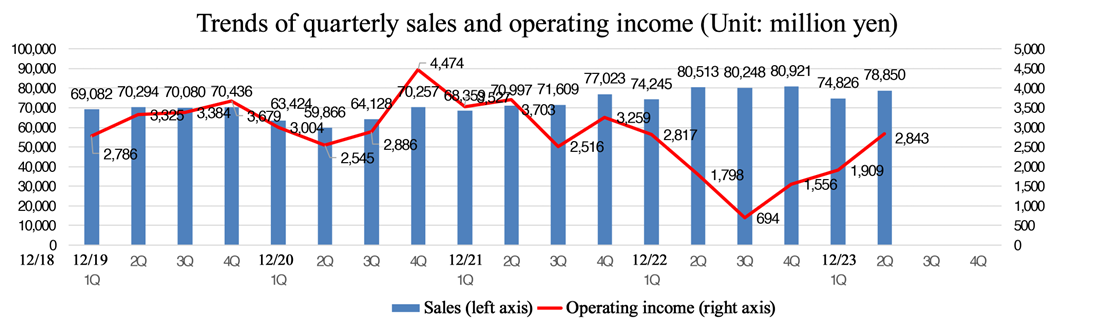
(2) Trends by Segment
| FY 22/12 1H | Ratio to sales | FY 23/12 1H | Ratio to sales | Year on Year |
Sales |
|
|
|
|
|
Colorant/Functional materials | 39,373 | 25.4% | 39,364 | 25.6% | -0.0% |
Polymers/Coatings | 38,144 | 24.6% | 36,349 | 23.7% | -4.7% |
Packaging materials | 39,988 | 25.8% | 40,361 | 26.3% | +0.9% |
Printing/Information | 36,332 | 23.5% | 36,344 | 23.6% | +0.0% |
Others/Adjustments | 921 | - | 1,258 | - | - |
Total | 154,758 | 100.0% | 153,676 | 100.0% | -0.7% |
Operating Income |
|
|
|
|
|
Colorant/Functional materials | 1,501 | 3.8% | 1,465 | 3.7% | -2.4% |
Polymers/Coatings | 1,497 | 3.9% | 1,917 | 5.3% | +28.1% |
Packaging materials | 470 | 1.2% | 1,418 | 3.5% | +201.2% |
Printing/Information | 588 | 1.6% | -41 | - | - |
Others/Adjustments | 559 | - | -7 | - | - |
Total | 4,615 | 3.0% | 4,752 | 3.1% | +3.0% |
*Unit: million yen. Operating income is composed of the ratio of profit to sales.
☆Colorants and Functional Materials Related Business
The performance of functional dispersions grew, but colorants are facing a market downturn, and materials for CF are in the process of recovery, with sales unchanged from the previous year. Although there was a slight decrease in profit, large-sized materials for CF were on a recovery trend, even though small and medium-sized ones recovered slowly. The global market recovery of inkjet ink and price revisions of colorants are progressed.
(Materials for Liquid Crystal Display Color Filters)
In addition to expanding sales in China and improving market share in Taiwan, production at LCD panel manufacturers headed toward recovery in the latter half, and shipments were on the rise.
(Colorants for Plastics)
In Japan, there was a decline in demand for containers and building material films due to consumer restraint and a decrease in the number of housings start. However, outside Japan, there was strong demand for solar cells.
(Inkjet Inks)
There was an impact from inventory adjustments in overseas markets, but it was in a recovery trend in the latter half.
(Materials for Automotive Lithium-ion Batteries)
Sales have been expanding as the company intensified supply in the U.S. and Europe. In the U.S. and China, facility enhancements are being made in preparation for future demand increases.
☆Polymers & Coatings Related Business
For panels and smartphones, inventory adjustments from the previous year continued, leading to poor performance. For packaging and industrial materials, both domestic and international markets experienced a decline in sales due to consumer restraint associated with rising prices, especially with the sluggish market conditions in China. In terms of profit, despite the downturn in the electronics market causing high-value-added products to underperform, recovery was seen due to price revisions both domestically and internationally.
(Coating Materials)
Adjustments in the smartphone and LCD panel markets continued, leading to a decline in demand for electromagnetic shielding films and heat-resistant micro-adhesive films.
(Adhesives)
For adhesives, there was a decline in demand for labels and displays in Japan. However, sales expanded in the U.S. and India due to facility enhancements. In Japan, adhesives for packaging remained steady, but overseas, there was a slowdown in demand for food packaging due to reduced consumption.
(Can coatings and polymers)
In Japan, operations at customers’ sites were stagnant, leading to a subdued performance. Outside Japan, there was a decline in demand for food cans due to factors such as a decrease in fish catch. On the other hand, in Thailand, the company acquired a local paint manufacturer to expand its business and strengthen its base.
☆Packaging Materials Related Business
While there was a slight increase in sales, significant profit growth was achieved through price revisions both domestically and internationally.
(Liquid Ink)
In Japan, due to rising prices, consumers refrained from purchasing, affecting the demand for food packaging materials. However, with the lifting of restrictions on activities, the sales of products for seasonal products and souvenirs remained steady. Cardboard packaging faced a decline, especially for beverages and processed foods, due to consumers' inclination to save. Outside Japan, demand in India remained robust, and sales were steady. However, in China, the downturn in consumption led to a decline in demand for food packaging materials. On the other hand, profit improvement progressed with the advancement of sales price revisions in response to rising raw material prices both domestically and internationally.
(Gravure Cylinder Plate-making Business)
The performance of products for packaging remained steady due to the demand for new plates, but the performance of precision plate-making related to electronics was sluggish.
☆Printing & Information Related Business
While sales increased, profit declined.
(Japan)
The structural shrinkage of the information printing market continued, with the business for flyers, advertisements, and publishing facing a downturn. However, paper packaging for travel-related demand remained steady. Given the persistent high costs of energy and raw materials, the company continues to pursue cost reduction through collaborations with other companies in the same industry and business structural reforms. Price revisions are also being advanced for costs that cannot be absorbed through self-help efforts.
(Overseas)
Outside Japan, sales were sluggish due to the deteriorating real estate market in China and a decline in exports. However, functional coatings for paper packaging saw an expansion in sales.
(3) Financial standing and cash flows
◎Main Balance Sheet
| End of December 2022 | End of June 2023 | Increase /Decrease
|
| End of December 2022 | End of June 2023 | Increase /Decrease
|
Current Assets | 229,247 | 221,930 | -7,317 | Current liabilities | 113,463 | 120,813 | +7,350 |
Cash | 55,117 | 49,213 | -5,904 | Payables | 70,738 | 60,152 | -10,586 |
Receivables | 100,390 | 99,945 | -445 | ST Interest Bearing Liabilities | 24,022 | 38,976 | +14,954 |
Inventories | 67,582 | 67,971 | +389 | Noncurrent liabilities | 69,836 | 59,880 | -9,956 |
Noncurrent Assets | 181,930 | 204,141 | +22,211 | LT Interest Bearing Liabilities | 59,851 | 45,520 | -14,331 |
Tangible Assets | 122,366 | 130,081 | +7,715 | Total Liabilities | 183,300 | 180,693 | -2,607 |
Intangible Assets | 2,619 | 4,730 | +2,111 | Net Assets | 227,877 | 245,378 | +17,501 |
Investment, Others | 56,944 | 69,330 | +12,386 | Retained Earnings | 151,414 | 152,873 | +1,459 |
Total assets | 411,177 | 426,072 | +14,895 | Total liabilities and net assets | 411,177 | 426,072 | +14,895 |
|
|
|
| Interest Bearing Liabilities Balance | 83,873 | 84,496 | +623 |
*Unit: million yen
Total assets increased 14.8 billion yen from the end of the previous term to 426.0 billion yen, mainly owing to an increase in inventories, and tangible assets, intangible assets, despite a decrease in cash.
Total liabilities decreased 2.6 billion yen from the end of the previous fiscal year to 180.6 billion yen due to an decrease in trade payables. Net assets grew 17.5 billion yen from the end of the previous fiscal year to 245.3 billion yen due to an increase in valuation difference on available-for-sale securities and a reduction in the deficit of the foreign exchange translation adjustment account.
As a result, equity ratio increased 2.2 points from the end of the previous fiscal year to 55.5%.
◎Cash Flow
| FY 22/12 1H | FY 23/12 1H | Increase/Decrease |
Operating Cash Flow | -262 | 5,631 | +5,893 |
Investing Cash Flow | 1,512 | -9,367 | -10,879 |
Free Cash Flow | 1,250 | -3,736 | -4,986 |
Financing Cash Flow | -6,155 | -3,506 | +2,649 |
Term End Cash and Equivalents | 58,802 | 47,642 | -11,160 |
*Unit: million yen
The decrease in gains from the sale of marketable securities and the reduction in inventory assets turned operating cash flow (CF) positive. Due to increased expenditures for the acquisition of tangible fixed assets, the investment CF turned negative. The reduction in expenditures for the acquisition of treasury shares reduced the deficit in financial CF.
(4) Topics
◎ Investment in the biotechnology company VLP Therapeutics
VLP Therapeutics is a U.S. biotechnology company that researches and develops vaccines for malaria, dengue fever, and cancer.
Investments were made in VLP Therapeutics, Inc. and VLP Therapeutics Japan Co., Ltd., a group company of VLP Therapeutics.

(Taken from the Company’s material)
Purpose of the investment:
✓Acquisition of the world's most advanced drug discovery-related know-how.
✓Acquisition of sales channels in the drug discovery market for the company's products.
✓Leveling up the company's bio-related products through joint development.
✓Acquisition of bio-related manufacturing process technology with a view to the future.
Examples of products for the bio market by VLP Therapeutics:
■Polymer materials for cell aggregation control
■Near-infrared fluorescent probe dyes.
◎Change their corporate name
Aiming for their own reform, they will change the company name. The change is scheduled for January 1, 2024.
The company announced in Dec. 2022 that they would change their corporate name.
The new name will be “artience Co., Ltd.
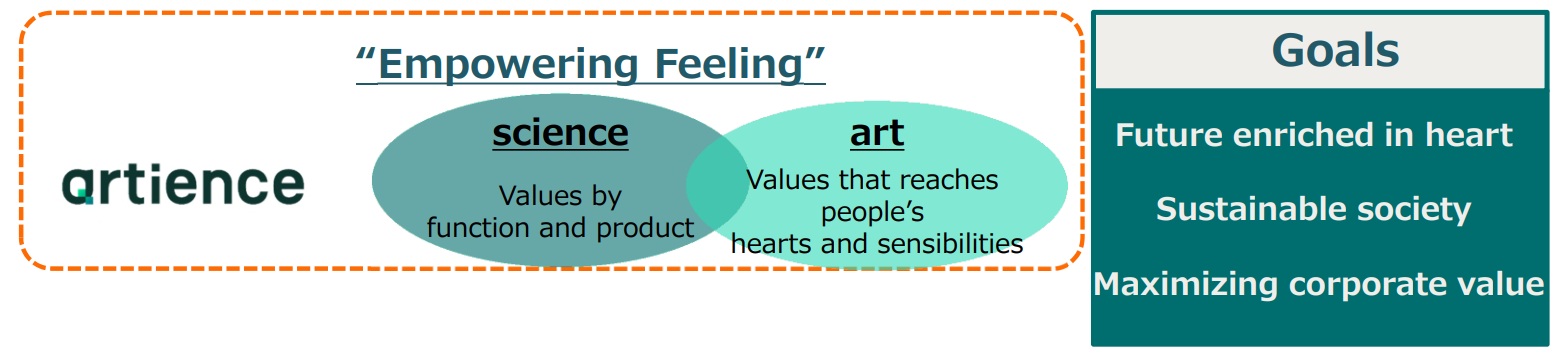
(Basic Philosophy)
●Reform of the business portfolio
●Maximization of capital efficiency and cash flow
●Building a corporate foundation and practicing sustainability management
◎ Next Medium-Term Management Plan
A new Medium-term Management Plan is scheduled to be announced in February 2024.
Next Medium-Term Management Plan:
✓Revenue expansion.
✓Target ROE of 7%, aiming for 10% in the future.
3. Fiscal Year ending December 2023 Earnings Forecasts
(1) Earning forecasts
| FY 12/ 22 | Ratio to sales | FY 12/ 23 Est. | Ratio to sales | YoY |
Sales | 315,927 | 100.0% | 330,000 | 100.0% | +4.5% |
Operating Income | 6,865 | 2.2% | 11,000 | 3.3% | +60.2% |
Ordinary Income | 7,906 | 2.5% | 9,500 | 2.9% | +20.2% |
Net Income | 9,308 | 2.9% | 6,000 | 1.8% | -35.5% |
* Unit: million yen. Forecasts are the figures announced by the Company.
Sales Increase, Operating Profit Rises
In the term ending Dec. 2023, sales are forecast to grow 4.5% year on year to 330 billion yen and operating income to increase 60.2% year on year to 11 billion yen. It is forecast that sales will decrease, and profit will increase in the Printing & Information segment, while other segments are expected to increase in sales and profit. From the second half of the fiscal year, sales volume has been recovering mainly in overseas markets, and both sales and profit are expected to grow steadily. In terms of products, high value-added products such as liquid crystal panels, electronics, and smartphone-related materials are on a recovery trend as inventory adjustments are projected to be completed by the second half. In the growing area of environmentally friendly products, sales of master batches for encapsulants for solar cells are expanding mainly in China, and sales are also expanding in India. In polymer materials related to environmental themes, full-scale adoption of laminate adhesives for LiB exteriors began in July in China, following Japan and South Korea, and there have been many inquiries. The global production capacity expansion that has been promoted so far is expected to contribute to the second half. CF (Color Filter) materials are on a recovery trend in the Chinese market, and a full-scale recovery is expected in the second half. For rapidly growing LiB materials, the company will be in the upfront investment stage in FY December 2023, and aims to move into the black in FY December 2024.
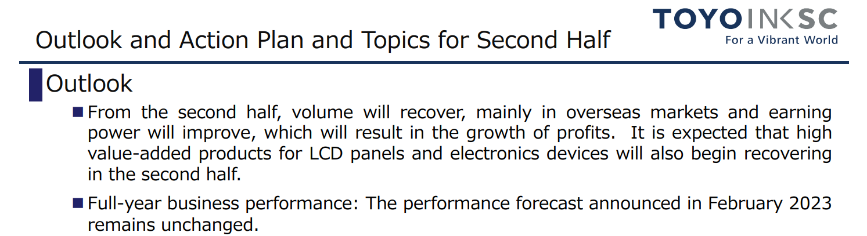
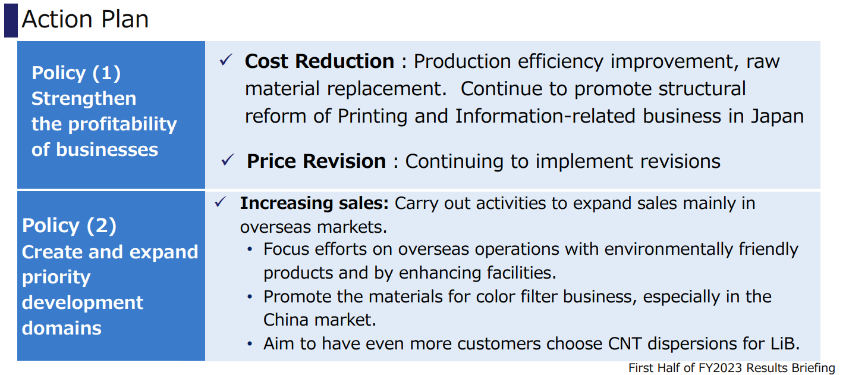
(Taken from the Company’s material)
The company plans to pay a dividend of 90.00 yen/share, like in the previous term. The estimated payout ratio is 79.5%.
(2) Trends by Segment
Sales | FY 12/22 | FY 12/23 Est. | YoY |
Colorant/Functional materials | 794 | 870 | +9.6% |
Polymers/Coatings | 762 | 780 | +2.3% |
Packaging materials | 835 | 880 | +5.4% |
Printing/Information | 752 | 750 | -0.2% |
Others/Adjustment | 17 | 20 | - |
Total | 3,159 | 3,300 | +4.5% |
Operating Income |
|
|
|
Colorant/Functional materials | 18 | 36 | +95.0% |
Polymers/Coatings | 25 | 45 | +79.7% |
Packaging materials | 10 | 25 | +159.6% |
Printing/Information | 7 | 12 | +83.5% |
Others/Adjustment | 9 | -8 | - |
Total | 69 | 110 | +60.2% |
* Unit: 100 million yen.
(Second half measures in each segment)
☆Colorants and Functional Materials Related Business
Increase in income and profit.
The company will expand supply of LiB dispersions to the markets in Europe, the U.S., China, and Japan. The company will discuss production of CF materials in the Chinese market. The company will aggressively develop environmentally friendly products for colorants. The company will focus on packaging applications for ink-jet printers.
☆Polymers & Coatings Related Business
Increase in income and profit.
For adhesives and bonding agents, the company will expand overseas operations and continue to implement price revisions in response to rising energy and other costs. To aggressively develop products in growing areas (environment, semiconductors, and medical) and reform the revenue structure.
☆Packaging Materials Related Business
Increase in income and profit.
They will promote price revisions , in addition to expanding mainly environmentally friendly products. They will strive to enhance their shares and improve revenues on the overseas market.
☆Printing & Information Related Business
Sales decreased, while profit grew.
The company will engage in expanding overseas business centered on functional ink in addition to promoting cost reduction and price revision through a continuous structural reform in Japan.
4. Progress of the medium-term management plan "SIC-II" (2021-2023)
(1) Progress until the term ended Dec. 2022
Amid the significantly changing business environment, the company proceeded with the following initiatives in the two years of 2021 and 2022 regarding the three policies of “Measures to Strengthen Profitability,” “Create and Expand Priority Development Domains” and “Enhance the Value of Management Resources for Sustainable Growth.”
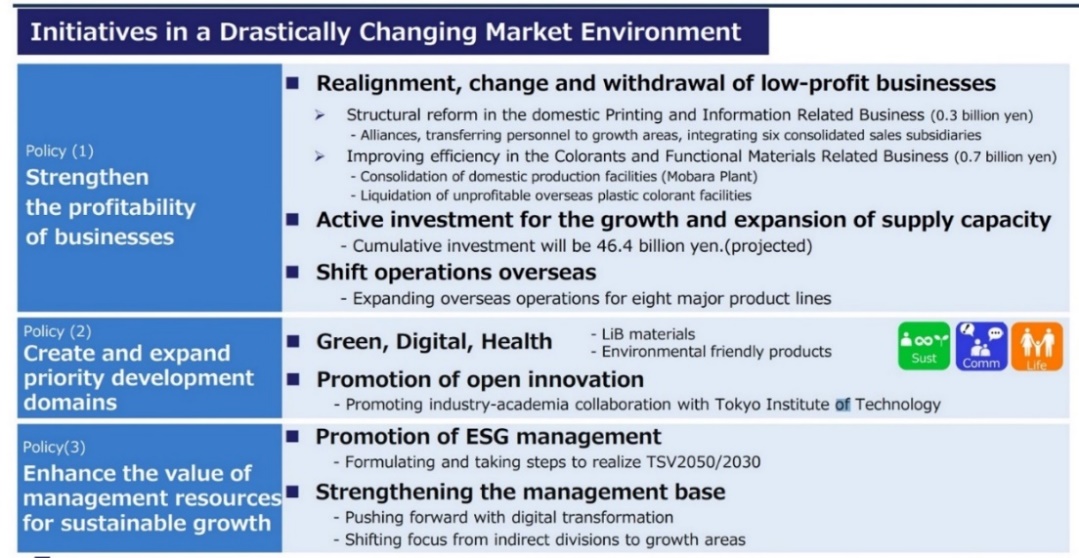
(Taken from the Company’s material)
They are forecasting “sales of 330 billion yen and an operating income of 11 billion yen” in the term ending Dec. 2023. Although sales will exceed the “sales of 300 billion yen and an operating income of 22 billion yen” set at the beginning of the mid-term management plan, operating income is projected to fall short of the goal.
(2) Future initiatives
Initiatives regarding each policy for the term ending Dec. 2023, which is the last term, are outlined below.
Policy 1 Measures to Strengthen Profitability
They will expand business based on environmentally friendly products on the continuously growing overseas market in regard to the eight core products.
They are expecting an overseas ratio of 54.2% in 2023, rising further from 49.9% in 2021 and 52.8% in 2022.
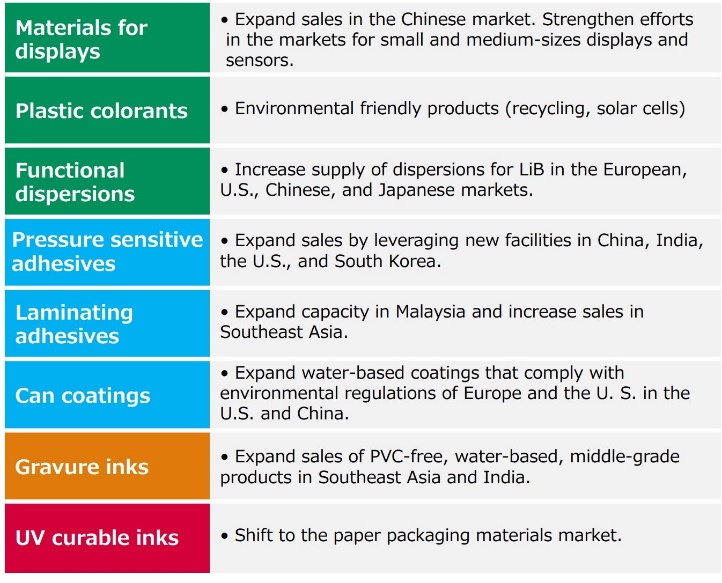
(Taken from the Company’s material)
Regarding materials for display, they will flexibly respond to the changes on the liquid crystal panel market.
While the liquid crystal panel market has been sluggish since the latter stages of the first half of fiscal 2022, the company assumes that it will recover from the second half of 2023, following a pause in inventory adjustment.
While the shift to China is quickly progressing and the competition will grow even fiercer, they will continue mass production tests, aiming for the adoption by clients.
Regarding the market for large panels, which are commodities, they will focus on enhancing cost competitiveness and operating systems in China in order to expand sales on the Chinese market, which is the largest in the world.
In the high-end market, they will boost thoroughly differentiated and functional products to expand their shares. Concretely, they will proactively launch small and medium finely designed thin film panels, CMOS, wavelength-controlling sensors, products for reducing environmental burdens such as pigments without dispersion and low-temperature curing products, etc.
Policy 2 Create and Expand Priority Development Domains
The demand for conductive carbon nanotube (CNT) dispersions for lithium-ion battery cathodes is growing in China and North America, and the company is gradually starting mass production.
In China, the dispersions is now used in next-generation, high-volume lithium-ion batteries for high-end EVs with a long cruising range, the largest car battery manufacturer in the world. They will expand facilities at their Zhuhai Base in China and enhance their production capability. Lithium-ion batteries are scheduled to be equipped with the dispersions from the 2024 mass-production model.
As the U.S. market for car batteries is rapidly expanding in North America, they newly established LioChem e-Materials (new company) as their second base in North America, in addition to their existing Georgia Plant. They are planning to start mass production in 2025.
The company will expand their business as the sole CNT dispersions manufacturer with original technologies and a production system in four centers, five-base, with Japan and Europe added to China and North America.
Regarding the market in Europe, they will start mass production in the first quarter of 2023 in Hungary, where they have finished second-stage construction works, while starting third-stage construction works. In Japan, they are currently upgrading their facilities in Fuji, Shizuoka Prefecture.
The company, which possesses original technologies, will also promote the development of high-performance CNT dispersions (for cathodes) achieving both performance and safety based on technology innovation, as well as related materials such as materials for anodes.
They will aim for sales of 40 billion yen by 2026.
Policy 3 Enhance the Value of Management Resources for Sustainable Growth
Regarding ESG management, they will promote the following initiatives in each field.

(Taken from the Company’s material)
Regarding the reinforcement of business foundations, they will introduce reskilling and recurrent education in addition to setting up a specialized organization for creating a new business. They will shift staff from back-office divisions to growing domains.
Regarding the reinforcement of foundations based on DX, they will promote DX in the fields of marketing, technology development, production, and management.
Capital Investments
They will make capital investments to promote growth.
They first planned to make capital investments a total of 40 billion yen in the three years of SIC-II, but they raised the amount to 46.4 billion yen.
In 2023, they are planning investments of 16.8 billion yen, including 8.8 billion yen for facilities for dispersions for LiB batteries.
Major capital investments
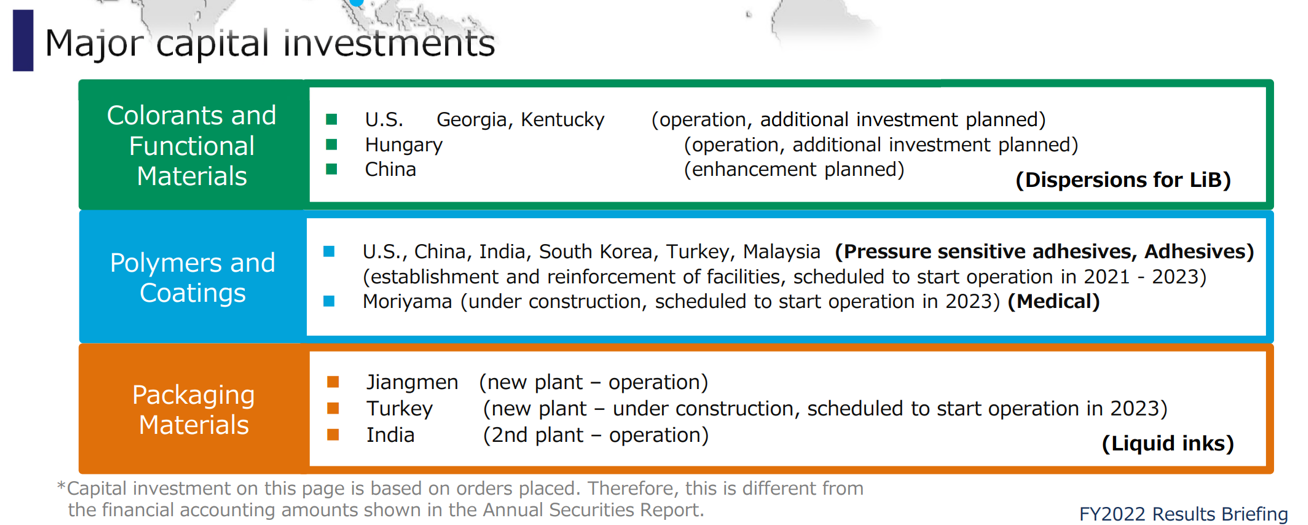
(Taken from the Company’s material)
For dispersions for LiB (LIOACCUM®), the company revised sales targets and investment amounts upwardly.
Recruitment activities for the steady expansion of LiB dispersions are underway. The product has received high praise from customers. Initially, the sales target was set at over 35 billion yen, but this has been revised upwardly to over 40 billion yen. Furthermore, to enhance production capacity, capital investment has been increased.
■The sales target for the fiscal year 2026 has been set at over 40 billion yen, and the capital investment has been revised to over 25 billion yen, with an increase of 5 billion yen each.
■Three new companies in North America have adopted their products, and production in Europe, the U.S., and Japan is progressing smoothly.
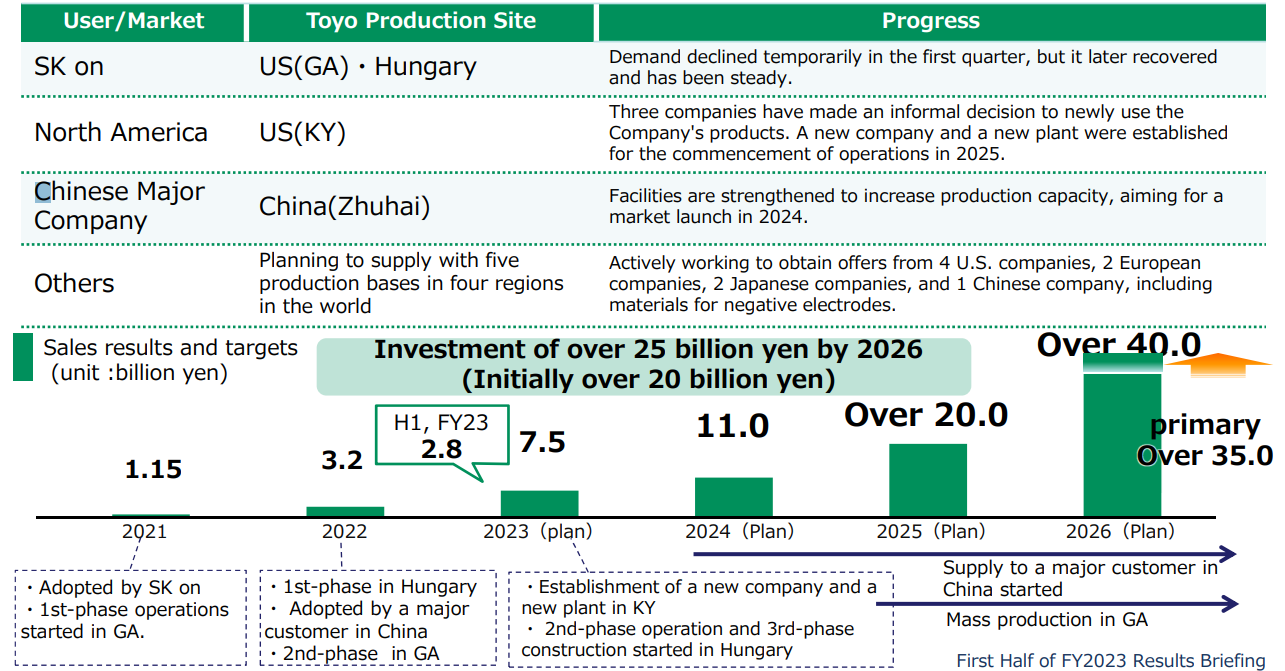
(Taken from the Company’s material)
Next Medium-term Management Plan:
As mentioned above, the next Medium-term Management Plan is scheduled to be announced in February 2024.
5. Future Focuses
In the term ending Dec. 2023, which is the last term of the Mid-Term Management Plan “SIC-II,” sales are projected to exceed the figures set at the beginning of the mid-term management plan period in all segments. However, the company's profit, which bottomed out in 3Q of FY December 2022, are showing a remarkable recovery as raw material and energy prices have become stable while they have been reflected in prices.
The company has recently revised its sales target for LiB dispersion upwardly. The EV market is expanding rapidly, and we take this as a sign of confidence in the company's ability to expand sales, including its technological competitiveness. In fact, business negotiations appear to be progressing. However, due to upfront investment, it may take time for LiB dispersions to make a full-scale contribution to profit.
Considering the recent recovery of performance and the growth driven by LiB dispersions, we believe that the stock price level that significantly falls below a PBR of 1 is undervalued. In the Medium-term Management Plan to be announced next February, measures are expected to be taken to improve PBR. President Takashima also sees this as a "serious problem" and expects in-depth measures to be taken.
| 2023 (original plan) | 2023 (Forecast for this term) | balance |
Sales | 3,000 | 3,300 | +300 |
Colorant/Functional materials | 815 | 870 | +55 |
Polymers/Coatings | 755 | 780 | +25 |
Packaging materials | 800 | 880 | +80 |
Printing/Information | 645 | 750 | +105 |
Operating income | 220 | 110 | -110 |
Colorant/Functional materials | 69 | 36 | -33 |
Polymers/Coatings | 85 | 45 | -40 |
Packaging materials | 56 | 25 | -31 |
Printing/Information | 13 | 12 | -1 |
* Unit: 100 million yen.
<Reference 1: Mid-Term Management Plan SIC-II (2021-2023)>
Under the 10-year long-term scheme, Scientific Innovation Chain 2027 (SIC27), aimed at achieving sustainable growth by 2027, the company breaks down the scheme into three 3-year mid-term management plans. They hope to clarify problems and roles in each stage, and to act steadily to realize an ideal future. Following the first stage of the scheme, Mid-Term Management Plan SIC-I (FY 2018-FY 2020), the second stage, Mid-Term Management Plan SIC-II (2021-2023) began in Jan. 2021.
<Summary of the Previous Mid-Term Management Plan SIC-I (2018-2020)>
Due to the significant changes in the external environment, including the skyrocketing of material prices, the changes in the market structure, and the coronavirus pandemic, the company failed to achieve its goals, but it was able to shift revenue sources to the polymers/coating and packaging material businesses, which are the prioritized area, and allocated resources to new businesses.
In addition, the company was able to proceed with the priority measure of promoting environmentally friendly products and distributed them in overseas areas too. With this, the company thinks they were able to produce results to some extent.
On the other hand, it was clarified that the company needs to further accelerate structural reform mainly in the Printing & Information Related Business, create pillars of new products and businesses, and respond to rapid changes in the market structure amid the coronavirus crisis.
<Recognition of the External Environment>
As for the novel coronavirus, the situation is improving gradually in FY 2021, but we must wait for the economic recovery to the pre-pandemic level until FY 2022 or later. The overseas market is expected to recover earlier than the domestic market.
The future outlook remains uncertain, and the business and market environments will remain harsh, but the company recognizes this adverse condition as a chance to change.
They set the keywords of the growing markets as “Green”, “Digital”, and “Health”.
<Ideal State>
The company aims to become “a company that contributes to a new era through the enrichment of life and culture.”
As mentioned above, the company defined the keywords of the growing markets as “Green”, “Digital”, and “Health”, and set their priority development areas as “sustainability”, “communication”, and “life”.
The company aims to realize an ideal state under the three policies: (1) Strengthen the profitability of businesses (2) Create more priority areas of development, and (3) Enhance the value of management resources for sustainable growth.
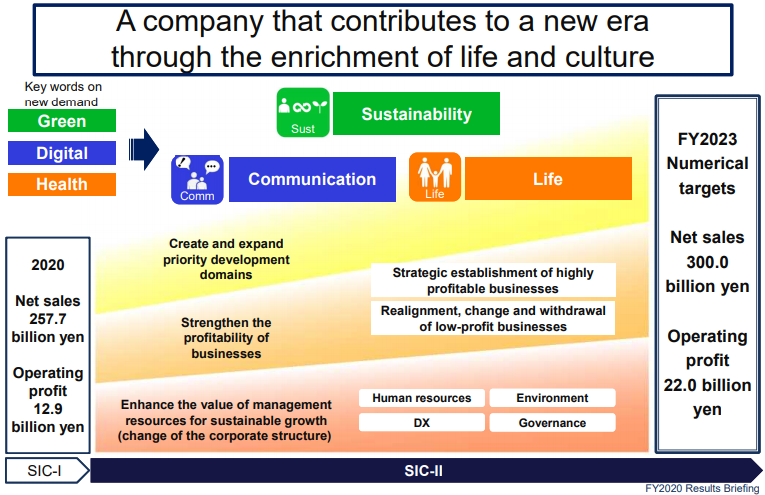
(Taken from the Company’s material)
<Numerical Goals>
The company aims to achieve sales of 300.0 billion yen, an operating income of 22.0 billion yen, an operating income margin of 7% or higher, and a ROE of 7% or higher in the term ending Dec. 2023.
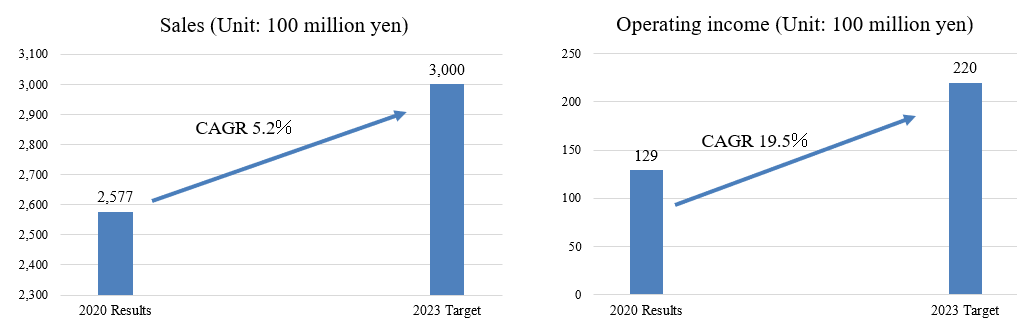
<Basic Policy 1: Measures to Strengthen Segments’ Profitability>
⊚ Measures for increasing revenues in each segment
Colorant/Functional materials | ◆Establish an earning pillar in growing markets -EV: To handle materials related to lithium-ion batteries -Digital: To expand the market share of resist inks for flat panel display (FPD) in China, and handle resist inks for image sensors and inkjet inks -Plastic colorants: To reorganize facilities and promote products with high added value |
Polymers/Coatings | ◆ Overseas expansion of the adhesives business and the entry to growing markets with new polymers -Packaging/industrial materials: To expand business outside Japan, by enhancing its production capacity and enriching the lineup of environmentally friendly products -5G and IoT: To establish a position in the 5G market and enter the semiconductor market -Medical/healthcare: To expand and develop the lineup of related products |
Packaging materials | ◆ Make products environmentally friendly and expand its business mainly in the Asian market -To commercialize the recycling of packages -To intensively invest in overseas growing markets in China, India, Turkey, Southeast Asia, etc. |
Printing/Information | ◆ Evolution into a profitable business that has adapted to the market environment -To promote functional inks for packages, such as paper containers, and the industrial field -To launch the color/communication business |
*From FY 2021, inkjet inks are included in the business of colorants/functional materials business rather than the printing/information business.
The target sales and operating income in each segment are as follows.
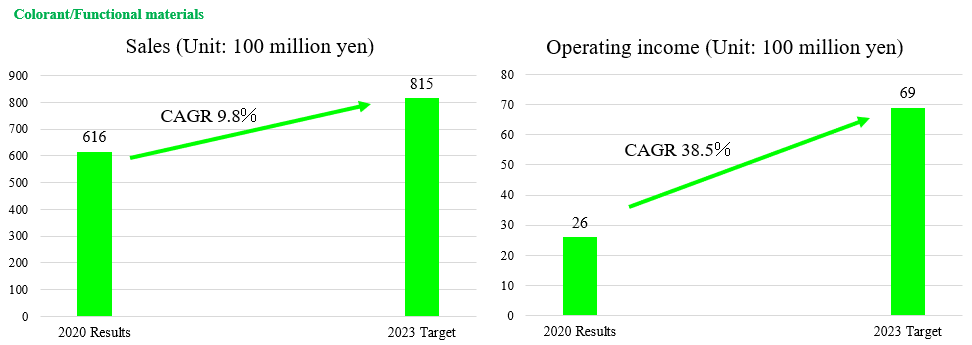
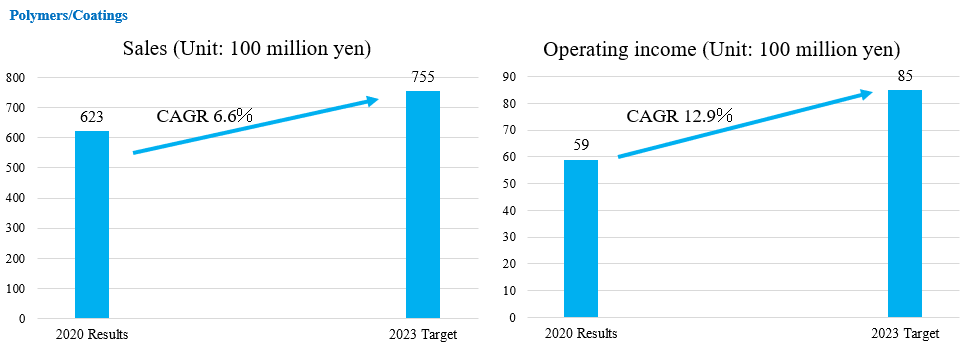
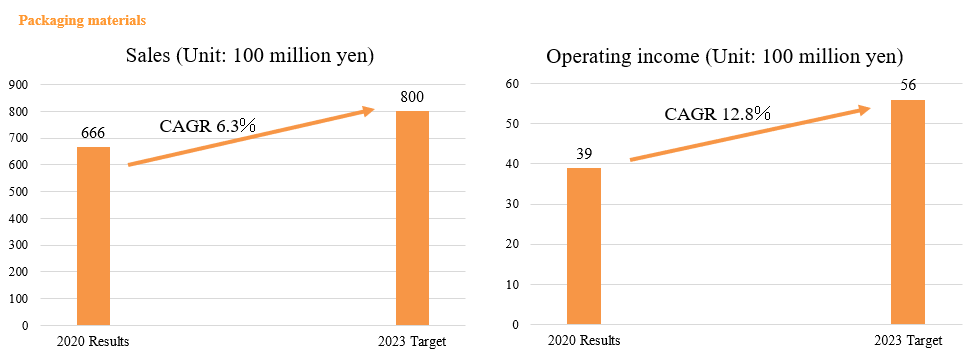
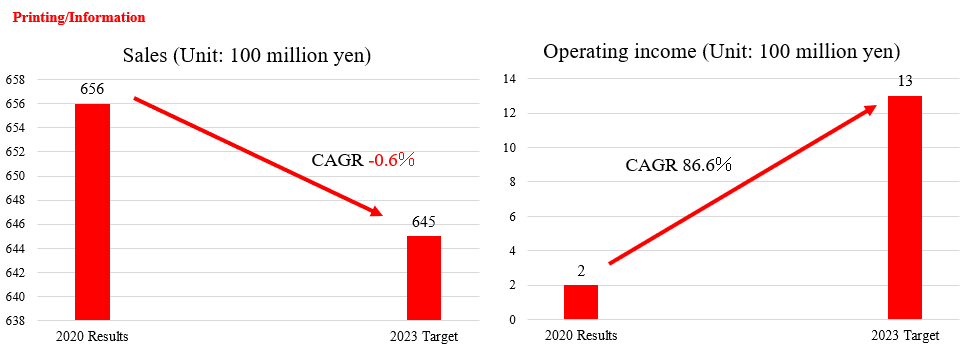
<Basic Policy 2: Create and Expand Priority Development Domains>
⊚ Three priority development domains
In the three priority development domains, the company will focus on the following points.
Sustainable Science | ◆ Realization of a sustainable society
(Major items to be developed) -Environmentally friendly packages made from biomass and recycled materials -Materials of lithium-ion batteries for EVs and new energy |
![]() | |
Communication Science | ◆ Contribute to 5G and IoT societies with key materials
(Major items to be developed) -Optical control materials for IoT and sensors -Low-dielectric materials, functional films, etc. for 5G and semiconductors |
![]() | |
Life Science | ◆ Make the lives of people affluent and healthy
(Major items to be developed) -Patch-type medicines -Inkjet inks for digital printing |
![]() |
⊚ Reform of the development structure
The company will strengthen the R&D structure in the priority development domains.
Research institutes will be established in the main company of each segment. These institutes will act as the specialized department for mid-term development strategies, dealing with them in a span of two to five years, and accelerate the creation of new products and businesses.
Colorants/Functional materials | Advanced Material Development Laboratory |
Polymers/Coatings | Polymer Material Development Laboratory |
Packaging materials | Functional Material Development Laboratory |
Printing/Information |
For longer-term development, Holdings R&D laboratories and Production Technology Research Laboratory will be in charge, and proceed with R&D in cooperation with other institutes.
⊚ Investment plan
The company will concentrate investments in growing markets.
For SIC-II, it plans to invest a total of 40 billion yen. In detail, 29% will be invested in colorants/functionals materials, 31% in polymers/coatings, 25% in packaging materials, and 11% in printing/information.
In six years, with the focus on the next three years (SIC-III), the company plans to invest about 20 billion yen in colorants/functional materials, about 30 billion yen in polymers/coatings, and about 40 billion yen in packaging materials.
The company plans to construct/upgrade factories for each segment as follows: (1) For colorants/functional materials, factories for EV-related materials in Japan, China, the U.S., and Europe, (2) for polymers/coating, factories for pharmaceuticals (Moriyama Factory), new polymer synthesis (Kawagoe Plant), and adhesives (the U.S., China, and India) and (3) for packaging materials, factories in Turkey, India, China, and Indonesia.
<Basic Policy 3: Enhance the Value of Management Resources for Sustainable Growth>
For reforming the corporate culture, the company will implement the following measures.
⊚ Reform of workstyles and HR systems
The company will strengthen a performance-based evaluation system.
Based on the declaration of empowerment of women, the company will raise the ratio of female managers in Japan from 4% to 8%.
It will recruit not only new graduates, but also various workers throughout the year.
It will discern the optimal scale of workforce and conduct appropriate staffing.
As remote work has become common, the company will reform its offices for innovation.
⊚ Promotion of Digital Transformation (DX)
The company recognizes DX as an important management mission for achieving sustainable growth and will promote it in each department.
Department | Measures |
Sales | -Digital marketing -Development of new business models |
Production | -Smart factories -Improvement of processes by IoT |
Technology development | -Materials informatics -Acceleration of development |
Management | -Promotion of Robotic Process Automation (RPA) -Education for promoting DX |
⊚ Transformation of the governance structure
In particular, the company will improve the independence of directors and auditors, secure transparency, adopt a performance-based remuneration system, strengthen risk management, and reduce strategically held shares.
⊚ Promotion of environment-conscious management
As the company is deeply aware of environmental issues, it will focus on the development and promotion of environmentally friendly products and contribute to the development of a sustainable society.
Social issues | Products/services |
Energy saving | -High-sensitive UV curing -EB (electron beam) curing |
Measures for VOC | -To make them water-base -To make them solvent-free |
Reduction of CO2 emissions | -Biomass products |
Reduction of food loss | -To retain freshness -To supply of materials for retort pouches |
Recycling of waste plastics | -Biodegradation -Recycling system |
In addition, the company will actively address the problem of climate change, by reducing CO2 emissions and saving energy, to realize the Carbon Neutrality 2050 vision, which is promoted by the government. In (FY)2022 following (FY)2020, Kawagoe Plant received the Chairperson Award of The Energy Conservation Grand Prize, Japan.
⊚ Cash flow policy
The company puts importance on the balance between financial soundness and investment/return to shareholders.
For financial soundness, the company will keep capital-to-asset ratio at the appropriate level and secure liquidity on hand.
It will actively conduct the investment in equipment, technologies, and human resources, and M&As.
It will also continue to pay dividends stably. In Feb. 2021, the company purchased treasury shares at a price of 5 billion yen, respectively. The company will plan to purchase more treasury shares depending on the situation.
<Reference 2: Regarding Corporate Governance>
◎ Organization type, and the composition of directors and auditors
Organization type | Company with an Audit and Supervisory Committee |
Directors | 11 directors, including 6 external ones(5 of which are independent directors) |
(As of August 23, 2023)
◎ Corporate Governance Report
The latest update: April 3, 2023.
<Basic Views>
The Toyo Ink Group (“the Group”) aims to enhance the overall value of the entire Group under a holding company system by strengthening groupwide strategic capabilities, speeding up management, and striking a balance between optimization on a groupwide scale and for individual lines of business.
The Group’s management framework revolves around the “Toyo Ink Group’s Philosophy System,” which takes the Group’s basic position on Group company management and distils it into a Corporate Philosophy, Corporate Policy and a set of Guiding Principles, and a “CSR Value System,” which consists of a CSR Charter and CSR Action Guidelines that clearly underline the Group’s commitment to social responsibility.
By putting the Toyo Ink Group’s Philosophy System and CSR Value System into practice, the Group will contribute to improving the sustainability of consumption, life and the global environment through science-driven manufacturing, with the aim of being “a company that contributes to the enrichment of life and culture throughout the world,” as stated in the Group’s Corporate Policy.
To achieve that, the Group has made it a top priority to evaluate its own corporate activities from the same point of view as its stakeholders, and to ensure balanced management from an economic, social, human and environmental standpoint, in order to create tangible and intangible corporate value and fulfill its social responsibilities.
To make that a reality, the Group is implementing the following measures.
- Adequately implementing approval and affiliate management regulations applicable to Group companies, to enable delegation of executive capabilities to individual operating companies and to strengthen corporate governance
- Improving internal control systems
- Strengthening the legal functional capabilities of General Meetings of Shareholders, the Board of Directors, the Audit and Supervisory Committee, accounting auditor and other such parties, in order to improve leadership and monitoring capabilities
- Disclosing information quickly, accurately and widely, in order to improve management transparency
- Strengthening and improving compliance systems
- Promoting environmental preservation on a global scale
These and other measures are intended to establish good relationships with all of the Group’s stakeholders,
including shareholders, suppliers, local communities and employees, and to enhance corporate governance.
<Reasons for Non-compliance with the Principles of the Corporate Governance Code>
The Company is implementing all of the principles under the Corporate Governance Code.
<Disclosure Based on the Principles of the Corporate Governance Code(excerpt)>
【Principle 1.4 Cross-Shareholdings】 | The Company holds shares of companies as it deems necessary for policy reasons as part of its management strategy, including business alliances, the maintenance and strengthening of business relationships and the stable procurement of raw materials. The Board of Directors examines the benefits of holding these cross-held listed stocks every year, comparing them with the cost of capital and the status of transactions of each individual stock, and the Company reduces the number of stocks it holds when it determines that it is no longer appropriate to hold the stocks, taking into consideration the situation of the companies and market trends. In FY2022, the Company sold all of the shares of nine stocks that it held and some of the shares of three stocks that it held. Voting rights in relation to cross-shareholdings for listed shares will be exercised in an appropriate manner on a case-by-case basis, taking into account whether or not the relevant proposal will help to enhance the corporate value of the issuing company over the medium to long term, whether or not it will contribute to the profits of all shareholders, including the Company, and the qualitative and overall impact it will have on the Group in terms of management and business. Where an issuing company has special circumstances, such as the occurrence of significant damage to its corporate value or a serious compliance violation, or where there is a concern that an suing company may damage the corporate value of the Company as its shareholder, judgment over whether or not to approve will be made carefully by collecting sufficient information through dialogues with the issuing company or by other means. |
【Supplementary Principle 2.4.1 Ensuring the Diversity in Promotion to Core Positions】 | The Group set itself a target of increasing the percentage of managers in Japan that are women to 8% by FY2023. The Group will provide career training for female future leaders and implement other initiatives to encourage female employees to take the first step in trying new jobs and duties with confidence and courage. In the Group's view, it is unnecessary to set a numerical target for the percentage of managers in Japan that are foreign nationals and midcareer hires given that its policy is not to discriminate on the basis of nationality or career background in the context of employment and career development. The Group endeavors to ensure diversity in accordance with the policy described later in this report. As of January 2023, the percentage of managers in Japan that are women was around 4.5%, the percentage that are foreign nationals was less than 1% and the percentage that are midcareer hires was around 32%. The Group's policies to cultivate human resources and develop an internal environment to ensure diversity are follows. <Cultivate human resources that have global perspectives and abilities> The Group cultivates human resources based on a policy of developing abilities through diverse practical work experience related to overseas business both in Japan and overseas. In anticipation of future needs, the Group also cultivates human resources through practical training at overseas subsidiaries aimed primarily at young and middle-ranking employees. <Foster diversity to invigorate the organization> In order to (i) provide information and training for mutual respect and the effective use of differences among employees and (ii) promote diversity, the Company established the Diversity and Inclusion (D&I) Promotion Office, a dedicated organization, to promote diversity and inclusion in 2023 to develop an environment, design programs and consider measures that will enable the active participation of diverse human resources. |
【Supplementary Principle 3.1.3 Sustainability Initiatives】 | In its long-term corporate vision, SIC27, the Group defines the concept of “sustainable growth” as the Toyo Ink Group growing sustainably and contributing to improvement of society's sustainability. In addition, and the Group has set the basic vision of promoting a range of sustainability activities centered on the achievement of carbon neutrality in 2050 and interim goals in 2030 by formulating its sustainability vision, TSV2050/2030, as a practical long-term goal for the Group’s sustainability activities. Framework to promote sustainability and disclosures of climate change-related financial information based on the TCFD recommendations are published in the Company’s website and Integrated Report 2022. With respect to human capital, the Group sees human resources as its most important management capital and actively invests in them, establishing the “Toyo Ink Vocational College”, introducing a human resource rotation program, promoting women's participation and advancement in the workplace to increase diversity, and ensuring safety and health in the workplace as a manufacturer. Similarly, in terms of the creation of new intellectual property, the Company has renewed its R&D structure to promote the development of new products and the creation of new businesses which meet the needs of society. In addition, the Group is endeavoring to promote open innovation and strategically acquire patents, and is actively disclosing information about these activities through its integrated report and other means. |
【Principle 5.1 2 Policy for Constructive Dialogue with Shareholders】 | The Company regards shareholders and investors as key stakeholders and makes every effort to respect shareholders’ rights and improve shareholder value, based on its Guiding Principle to “enhance shareholder satisfaction (SHS).” In particular, constructive dialogue with shareholders and investors is positioned as an important factor. The Company has appointed a Director in charge of IR, in order to effectively share information through organic cooperation between related divisions. The General Affairs Department and the Corporate Planning Division work to promote dialogue with shareholders and investors, respectively. If feedback obtained through dialogue is deemed to be important, it is then reported to the relevant Director as necessary. In terms of managing insider information, there are regulations in place such as Insider Trading Prevention & Management Regulations and Information Protection & Management Regulations. The Group has also set out specific action guidelines in the form of its Business Code of Conduct, and distributes guidebooks to all Group employees, as well as providing regular education in an effort to effectively raise awareness. |
This report is not intended for soliciting or promoting investment activities or offering any advice on investment or the like, but for providing information only. The information included in this report was taken from sources considered reliable by our company. Our company will not guarantee the accuracy, integrity, or appropriateness of information or opinions in this report. Our company will not assume any responsibility for expenses, damages or the like arising out of the use of this report or information obtained from this report. All kinds of rights related to this report belong to Investment Bridge Co., Ltd. The contents, etc. of this report may be revised without notice. Please make an investment decision on your own judgment. Copyright(C) Investment Bridge Co., Ltd. All Rights Reserved. |